PEKO to Host Webinar to Discuss DFMA for Machine Frames
PEKO Precision Products announces that its engineering and manufacturing experts will be discussing how to design welded and sheet metal machine frames for more cost-effective and consistent production in a workshop called "DFMA Crash Course for Machine Frames" on Wednesday, May 4 at 1:00 PM EST.
Design for manufacturability and assembly (DFMA) is a critical process that engineers can use to examine various aspects of a product's design prior to (and during) manufacturing to look for opportunities for improvement and ensure efficient manufacturing and assembling processes.
DFMA initiatives can take place at different stages of the commercialization process, but often prove most valuable following prototype efforts and scaling to "beta" or pilot units. Companies that follow DFMA guidelines are typically able to lower product cost, increase product reliability, and shorten time to market.
To help engineers navigate these considerations and deliver optimal product design with respect to frame DFMA, PEKO has prepared a webinar: DFMA Crash Course for Machine Frames. This free, one-hour webinar, led by PEKO Engineer Mark Frosino, will discuss everything from material selection and welding to print callouts and the impact of functional features when optimizing designs for frame fabrication.
Participants will gain an understanding of the basic concepts and principles of DFMA, the benefits and challenges of DFMA on machine frames, some common design considerations for machine frames, and how such challenges can be overcome with successful adoption of the principle. This perspective will help you introduce ways to incorporate these features into your product for the best price and repeatable manufacturing.
You Will Learn:
- Why DFMA is so important in product development
- Expert tips and tricks from a contract manufacturer
- Common fabrication and assembly checks
- How DFMA affects your design process
- How to solve DFMA issues during design
All interested engineers, project managers, and machine designers and builders are encouraged to register for this free online webinar
Featured Product
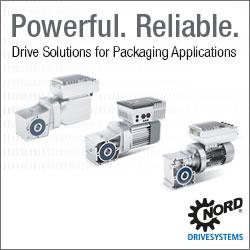