Introduction of automatic cutting equipment for black steel seamless pipes
Black steel seamless pipe automatic cutting equipment includes steel pipe intersecting wire cutting machine and CNC plasma cutting machine.
Black steel seamless pipe automatic cutting equipment includes steel pipe intersecting wire cutting machine and CNC plasma cutting machine.
The CNC plasma cutting machine is a three-dimensional cutting, which is mainly aimed at cutting intersecting holes, intersecting lines at the ends of the tubes, and welding cracks, which is different from the general flat CNC cutting of metal sheets. Therefore, customers have to choose according to their own cutting requirements, so what aspects should be paid attention to in the selection?
The following five points should be considered when choosing a steel pipe intersecting line cutting machine:
1. Cutting pipe diameter
Select the intersecting line cutting machine with corresponding parameters according to the diameter of the cutting pipe. Under normal circumstances, the intersecting wire cutting machines produced by manufacturers are non-standard and configured according to the different needs of customers. Generally, the standard cutting pipe diameter range is 60-600mm, which can be increased according to the customer's pipe diameter requirements. The larger the cutting pipe diameter, the higher the price.
2. Cutting wall thickness
Choose the appropriate cutting method according to the material and wall thickness of the black steel seamless pipe, such as flame, plasma and laser cutting methods. Generally, high precision is required, and the wall thickness is relatively thin, laser cutting can be selected; for cutting alloy steel and stainless steel, plasma cutting is selected; for thicker carbon steel, flame cutting is recommended.
3. Number of intersecting lines
According to the customer's requirements for pipe cutting, the number of axes of the automatic cutting equipment for black steel seamless pipe is selected. Generally, if it is not necessary to cut the crack on the pipe, use a three-axis intersecting wire cutting machine. To cut a break on the pipe, choose four-axis, five-axis, six-axis, seven-axis, etc. according to the different angles of the pipe used for the break.
4. Cutting software
When each intersecting line manufacturer has the same number of equipment linkage axes, the ability to realize the intersecting line groove is not very different. The main difference between them is the intersecting line programming software used. Kaisui is developed by a Canadian company, which can realize functions such as 3D node expansion, key optimization and nesting, pipe splitting and 3D simulation simulation, and the software can be upgraded free of charge.
5. Cutting hardware
Cutting hardware is also a concern for steel pipe intersecting wire cutting machines. The hardware configuration determines the stability and service life of the device. The hardware used by Kasiri uses imported accessories, such as Taiwan Advantech for the host, high control card, and Japanese Panasonic for the servo motor.
For more, please visit: https://www.nan-steel.com/news/black-steel-seamless-pipe.html
Featured Product
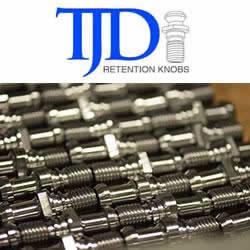
T.J. Davies' Retention Knobs
Our retention knobs are manufactured above international standards or to machine builder specifications. Retention knobs are manufactured utilizing AMS-6274/AISI-8620 alloy steel drawn in the United States. Threads are single-pointed on our lathes while manufacturing all other retention knob features to ensure high concentricity. Our process ensures that our threads are balanced (lead in/lead out at 180 degrees.) Each retention knob is carburized (hardened) to 58-62HRC, and case depth is .020-.030. Core hardness 40HRC. Each retention knob is coated utilizing a hot black oxide coating to military specifications. Our retention knobs are 100% covered in black oxide to prevent rust. All retention knob surfaces (not just mating surfaces) have a precision finish of 32 RMA micro or better: ISO grade 6N. Each retention knob is magnetic particle tested and tested at 2.5 times the pulling force of the drawbar. Certifications are maintained for each step in the manufacturing process for traceability.