New 1-Axis and Multi-Axis Motion Controllers with EtherCat® Connectivity, based on ACS Intelligent Drive Modules
These new controllers from PI optimize the performance of linear stages, rotary stages, and gantry robots, equipped with direct-drive servo motors, stepper motors, and voice-coil motors.
High performance motion control is a key requirement for many high-tech industries, from laser processing, medical device manufacturing, bio-genomics, aerospace, photonics alignment, and semiconductor manufacturing, to name a few. High precision nano positioning stages, designed for high-duty-cycle operation are crucial here, but the positioning hardware also requires state-of-the-art motion controllers to extract the maximum of performance. Precision motion systems leader PI recently expanded its motion control families with new ACS-hardware-based closed-loop controllers, providing EtherCat® connectivity.
A-811, Compact 1-Axis Controller
Equipped with ultra-low noise PWM drives, the A-811 single axis controller integrates a closed loop servo controller with drive in a compact case. It can handle voice coil drives, DC motors, and brushless 3-phase motors, as well as high-resolution incremental encoders with sine/cosine output and absolute measuring encoders based on BiSS-C protocol. The ultra-low noise PWM drives allow for high-resolution motion with nanometer resolution.
G-901, Multi-Axis Industrial Motion Controller Family for High Power Applications
The new G-901 controllers are also based on ACS hardware and EtherCat® connectivity, providing up to 1500W output per axis. Many advanced control features, such as STO (safe torque off), Servoboost, NanoPWM, and special algorithms for gantry control, laser triggering, and high-speed contouring, are available and improve the throughput and performance in applications from laser machining to 3D printing.
Why EtherCat® Standard?
EhterCat® is an open standard that allows easy extension and scaling of existing control hardware with additional controller modules or 3rd party peripherals such as I/O, cameras, sensors, etc. Unlike with proprietary communication standards, EtherCat® -based controllers provide their users with much higher flexibility and significantly lower costs in the long run.
More information: G-901 Multi-Axis Industrial Motion Controller
More information: A-811 1-Axis Industrial Motion Controller with EtherCat
About PI
PI is a privately held company that designs and manufactures world-class precision motion and automation sub-systems including air bearings, hexapods and piezo drives at locations in North America, Europe, and Asia. The company was founded 5 decades ago and today employs more than 1400 people worldwide. PI's customers are leaders in high-tech industries and research institutes in fields such as photonics, life-sciences, semiconductors, and aerospace.
Featured Product
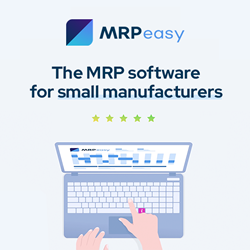