Packaging inspired by nature’s principles
Sandvik launches an innovative smart packaging solution
Part of Sandvik Group's machining solutions division, Sandvik Coromant, is launching an optimized packaging solution to level up its operational sustainability. Developed by R&D engineer and system developer Maria Rajabzadeh Namaghi as part of Sandvik Coromant's Automation Platform team, the solution uses artificial intelligence (AI) to determine the smallest possible packaging required to contain a product, reducing costs and CO2 emissions in the process.
Packaging is a necessary evil for manufacturers. It raises many environmental concerns due to its demand for resources, requiring energy, water, chemicals, and materials. Packaging is also a huge source of waste. For example, in the United States, 28 per cent of total municipal solid waste (MSW) is attributed to packaging, according to the Environmental Protection Agency.
Recognising this problem, Rajabzadeh Namaghi was set the task of selecting packages for Sandvik Coromant's products that were as small and lean as possible, with the aim of cutting costs and reducing Sandvik Group's overall carbon footprint.
To solve this, Rajabzadeh Namaghi considered the possibility of applying a genetic algorithm (GA) using AI. GAs are used to solve optimisation problems and they work by imitating natural selection. By repeatedly modifying a selection of possible solutions, the GA allows the solution to ‘evolve' until the ideal result is found, in line with Darwin's theory of evolution. Although GAs are nothing new, applying them to packaging solutions is a less common application.
Rajabzadeh Namaghi's innovative idea has been realised in collaboration with Samir Balic, Product Manager Packaging and Labelling at Sandvik Coromant, as a Package Selector Application (PSA). The PSA analyses a 3D CAD model of the product and by identifying the product's critical points, in combination with the company rules for package selection, the AI algorithm calculates its rotation and recommends the smallest packaging possible. Using PSA also enables centralised and unified package selection across Sandvik Coromant.
"The PSA is incorporated directly to product designers' CAD programs, so the most suitable packaging for a product can be determined before a physical copy of the tool itself has even been created," explained Rajabzadeh Namaghi. "The solution completely automates the packaging process, streamlining operations and supporting Sandvik Group's wider sustainability goals.
"Sandvik Group is committed to making the sustainability shift across all its business areas," added Mats W Lundberg, head of sustainability at Sandvik Group. "Sandvik Coromant's packaging innovation not only results in less waste, but also improves sustainability throughout the value chain.
"Optimised packaging selection avoids excessive packaging use, opening up the potential to transport more products at once, increasing shipment capacity. In turn, increased capacity could result in less loads to transport the same number of products, reducing fuel consumption and supporting Sandvik Group's company-wide target to half its CO2 impact by 2030."
Sandvik Coromant will be launching the PSA in the second half of 2021.
About Sandvik Group: Sandvik is a high-tech and global engineering Group with around 38,000 employees with a strong commitment to enhancing customer productivity, profitability and sustainability.
The business achieves world leading positions in tools and tooling systems for industrial metal cutting equipment and tools, service and technical solutions for the mining and construction industries and advanced stainless steels and special alloys as well as products for industrial heating.
Featured Product
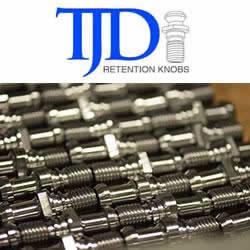
T.J. Davies' Retention Knobs
Our retention knobs are manufactured above international standards or to machine builder specifications. Retention knobs are manufactured utilizing AMS-6274/AISI-8620 alloy steel drawn in the United States. Threads are single-pointed on our lathes while manufacturing all other retention knob features to ensure high concentricity. Our process ensures that our threads are balanced (lead in/lead out at 180 degrees.) Each retention knob is carburized (hardened) to 58-62HRC, and case depth is .020-.030. Core hardness 40HRC. Each retention knob is coated utilizing a hot black oxide coating to military specifications. Our retention knobs are 100% covered in black oxide to prevent rust. All retention knob surfaces (not just mating surfaces) have a precision finish of 32 RMA micro or better: ISO grade 6N. Each retention knob is magnetic particle tested and tested at 2.5 times the pulling force of the drawbar. Certifications are maintained for each step in the manufacturing process for traceability.