ASTM International Supports Two New Research Projects for Additive Manufacturing
For the first time, the CFP allowed non-AM CoE partners to propose and receive support for projects focused on closing AM standardization gaps. A review process was conducted by a panel of experts from the ASTM F42 additive manufacturing group on research and innovation, resulting in the selection of two high-impact projects.
W. CONSHOHOCKEN, Pa., Feb. 22, 2021 - ASTM International's Additive Manufacturing Center of Excellence (AM CoE) announced awardees of its Call for Projects (CFP) in support of its Research to Standards initiative to further accelerate standards development for additive manufacturing (AM).
For the first time, the CFP allowed non-AM CoE partners to propose and receive support for projects focused on closing AM standardization gaps. A review process was conducted by a panel of experts from the ASTM F42 additive manufacturing group on research and innovation, resulting in the selection of two high-impact projects.
"The broadening of this project call has further strengthened the AM CoE's research and development capabilities and enhanced engagement with the global AM community," said Dr. Mohsen Seifi, ASTM International's director of global additive manufacturing programs. "We received a strong international response with a diverse range of topics, reflecting the high demand to bridge research to standards in the AM industry."
Fraunhofer Institute for Laser Technology ILT (Germany) will generate data required to support a new standard for monitoring the health status of optical systems in laser beam powder bed fusion (LB-PBF) machines. This work has potential to improve the reliability of additive manufacturing systems while reducing maintenance downtime and costs.
"This support provides Fraunhofer ILT with a perfect framework to bolster the industrial adoption of LB-PBF with our continued research," said Christian Tenbrock, group manager for laser powder bed fusion at Fraunhofer ILT. "We look forward to collaborating with ASTM International to further the impact of laser technology in the field of additive manufacturing."
National Research Council Canada (NRC), with partners Swerim (Sweden), Sirris (Belgium), and RISE (Sweden), will develop data to support a new standard for determination of moisture content in AM powder feedstocks, critical to the reliability, stability, and productivity of AM processes. Feedstocks are handled under controlled conditions, however moisture cannot always be avoided, impacting process robustness. This work will help develop data needed to validate methods to monitor moisture and increase process reliability.
Through valuable partnerships, the AM CoE has initiated 22 R&D projects to date, covering a broad range of topics such as AM data, feedstock, process qualification, in-situ monitoring, inspection, and testing. For more information on the AM CoE, visit www.amcoe.org.
About ASTM International
Committed to serving global societal needs, ASTM International positively impacts public health and safety, consumer confidence, and overall quality of life. We integrate consensus standards - developed with our international membership of volunteer technical experts - and innovative services to improve lives… Helping our world work better.
Featured Product
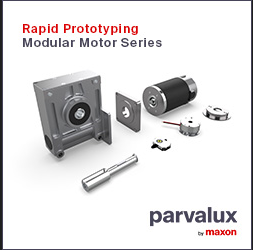