Stahlin Enclosures Provides Aesthetic And Product Performance Solutions For Water/Wastewater OEM
This case study highlights HydroClear™ Pro 95 from Full Circle Water®
Stahlin® Enclosures -- the world's most specified non-metallic electrical and industrial enclosures --- announces the release of a new case study featuring solutions for the water/wastewater industry, available for download at no obligation by visiting: https://stahlin.com/case-study/water-wastewater-oem-aesthetic-solution/
This case study highlights HydroClear™ Pro 95 from Full Circle Water® --- a closed loop recycling system featuring an all-in-one design that saves floor space by eliminating the need for a separate holding tank. One of the criteria for selection of an enclosure to protect system components was the need to incorporate eye-catching visual, digitally-printed graphics. Another requirement was that the enclosure should be Made-In-The-USA.
Consequently, Full Circle Water® selected Stahlin® Enclosures as its supplier of a J2020 fiberglass enclosure to meet its challenges for protecting critical instrumentation and electrical components.
This case study features testimonial statements from Full Circle Water® detailing how Stahlin® provided a reliable enclosure solution including a digitally printed cover with a full-color image of the American flag.
The Stahlin® J-Series was designed as an industrial enclosure for harsh, aggressive environments. Originally developed as an electrical junction box for the oil refining and petrochem industries, the J-Series has evolved over the years into a versatile industrial enclosure with varied applications for use from high-end electronics to extreme corrosive applications both indoors and out.
For Additional Information:
www.stahlin.com/
Featured Product
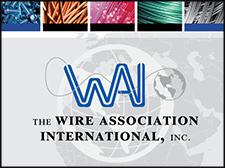
The Wire Association International (WAI), Inc.
The Wire Association International (WAI), Inc., founded in 1930, is a worldwide technical society for wire and cable industry professionals. Based in Madison, Connecticut, USA, WAI collects and shares technical, manufacturing, and general business information to the ferrous, nonferrous, electrical, fiber optic, and fastener segments of the wire and cable industry. WAI hosts trade expositions, technical conferences, and educational programs.