ABB expands flexible manufacturing portfolio with innovative magnetic levitation shuttle system
Strategic partnership with Planar Motors Inc. (PMI) enhances B&R’s adaptive machine offering, integrating PMI’s new production technology milestone in open, adaptive manufacturing
ABB is partnering with Canada's PMI to expand its machine automation offering: The integration of PMI's magnetic levitation technology into the company's Machine Automation Division's (B&R) portfolio will accelerate industry's transition from strictly linear production to an open, adaptive manufacturing space. This will support B&R customers in the transition to highly flexible and precise manufacturing in response to the fundamental shift to batch size one production and shorter product lifecycles. Furthermore, ABB has taken a significant equity stake in PMI as part of the agreement.
ACOPOS 6D is a rail-free product transportation system, with intelligent shuttles that move independently between stations, without being bound to a rigid, sequential production flow. The ACOPOS 6D shuttles are contactless, noiseless and precise, gliding freely above a surface, accelerating and maneuvering in every direction with six degrees of freedom - they can even move vertically on walls.
With no mechanical friction or resulting contamination, the technology is particularly timely given rapid shifts in manufacturing accelerated by the current pandemic and the need for a sterile environment in industries that are accelerating automation as a result, including food & beverage, healthcare and pharmaceuticals.
Similar to automated guided vehicle systems (AGV's), customers benefit from the freedom of movement of objects carried within or between several machines. With ACOPOS 6D, machines can simultaneously manufacture different product variants or even entirely different products, with each shuttle able to navigate its own way through the production process, amongst a swarm of other shuttles, taking its individual product on a unique path to the stations it needs for customized production.
"With ACOPOS 6D we are once again pushing the boundaries of technology by capitalizing on our strong partner network. The capability of ACOPOS 6D delivers unprecedented flexibility for a wide range of industries, allowing sectors such as healthcare and pharma to benefit from our flexible manufacturing solutions," said Sami Atiya, President of ABB Robotics & Discrete Automation. "Through our partnership, we are complementing our industry-leading robotics and machine automation portfolio and fostering our position as the only company to offer machine manufacturers and industrial customers the entire range of integrated hardware and software solutions from a single source."
Xiaodong Lu, President and co-founder of PMI, said: "Partnering with ABB will ensure we can further develop our technology and revolutionize industrial manufacturing. Our technology will work seamlessly with ABB's machine automation solutions, allowing customers to benefit from unrivaled flexibility, precision and intelligence. We are excited to jointly continue the success story of our technology together with ABB's global presence and domain expertise."
B&R is a unit of ABB's Robotics and Discrete Automation business and a global technology leader in machine automation. It combines state-of-the-art technology with advanced engineering to provide customers in virtually every industry with complete solutions for machine and factory automation, motion control, HMI and integrated safety technology.
ABB Robotics & Discrete Automation is a pioneer in robotics, machine automation and digital services providing innovative solutions for a diverse range of industries, from automotive over electronics to logistics. As one of the world's leading robotics suppliers, we have shipped over 400,000 robot solutions. We help our customers of all sizes to increase productivity, flexibility and simplicity and to improve output quality. We support their transition towards the connected and collaborative factory of the future. ABB Robotics & Discrete Automation employs more than 10,000 people at over 100 locations in more than 53 countries. www.abb.com/robotics
ABB (ABBN: SIX Swiss Ex) is a leading global technology company that energizes the transformation of society and industry to achieve a more productive, sustainable future. By connecting software to its electrification, robotics, automation and motion portfolio, ABB pushes the boundaries of technology to drive performance to new levels. With a history of excellence stretching back more than 130 years, ABB's success is driven by about 110,000 talented employees in over 100 countries. www.abb.com
Featured Product
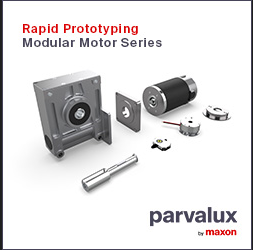