U.S. Air Force Advanced Manufacturing Olympics and AFWERX Base of the Future Competition Selects 300 Below, Inc. as Top Team
300 Below also became a top 10 finalist at the U.S. Air Force Rapid Sustainment Office's (AFRSO's) Advanced Manufacturing Olympics' material hurdles technical challenge, held virtually from October 20-23, 2020.
300 Below, Inc., recipient of 2019's Innovation of the Year in Manufacturing Technology, was announced as one of the top 92 participating teams selected from across the globe competing in AFWERX's Base of the Future Challenge, as a catalyst for fostering innovation within the U.S. Air Force (USAF) by using its technology to triple the life of at-risk metals for ~20% cost of the item. 300 Below also became a top 10 finalist at the U.S. Air Force Rapid Sustainment Office's (AFRSO's) Advanced Manufacturing Olympics' material hurdles technical challenge, held virtually from October 20-23, 2020.
The USAF's Advanced Manufacturing Olympics is centered around five technical challenges, including reengineering of legacy parts, 3D-printed part re-creation, material hurdles (advanced manufacturing techniques to improve aluminum and polymer materials), part certification and approval sprints, plus supply chain management. The Grand Prize winner receives a $100,000 check, plus opportunities to field their technology globally across the U.S. Air Force enterprise.
The USAF's AFWERX Challenge is centered around six topics - Base Security, Installation Resilience, Leveraging Technology for Operational Effectiveness, Reverse Engineering, Culture of Innovation, and Airman and Family Wellbeing. The proposals selected to advance represent innovative solutions ranging from additive manufacturing, reverse engineering, innovation culture, facility resiliency, virtual and augmented reality, and autonomous systems. Notable finalists alongside 300 Below, Inc. include AT&T, Booz Allen Hamilton, Coursera, CTC, IBM, Innovatrium, Leidos, Sales Force, and Siemens.
300 Below, Inc. is competing in the Improving Installation Resilience Amid COVID-19 AFWERX Challenge with its cryogenic treatment process alongside a diverse group of teams - originating from the vast regions of North America, Europe, Australia and other allied countries, comprised of entrepreneurial startups, small businesses, large enterprises, academic institutions and research labs - all vying to build the Base of the Future and modernize the Department of Defense.
"The AFWERX Base of the Future Challenge is critical to our mission of increasing collaboration between large businesses and entrepreneurs to accelerate solutions for the Air Force," stated Mark Rowland of AFWERX. "On behalf of AFWERX and the Department of Defense, we congratulate the teams advancing to the next phase. Their contributions are invaluable and have the potential to create game-changing results across the Air Force enterprise."
The Improving Installation Resilience Amid COVID-19 Challenge focuses on ways in which the U.S. Air Force can counter a global health crisis and better prepare for future crises of this magnitude. This Challenge aims to create robust and resilient Air Force bases that can withstand all types of disastrous events ranging from adverse weather conditions to pandemics. The Challenge seeks solutions including predictive analytics and technologies to defeat and mitigate risk.
300 Below, Inc. received multiple AFWERX Small Business Innovation Research (SBIR) contracts totaling ~$1.5 million for the improvement of at-risk metal parts within the Department of Defense, including firearms and vehicle brake rotors, typically adding 300% longer life for about 20% cost of the item. 300 Below's cryogenic treatment technology uses a liquid-nitrogen-based process to slowly release vapors into a computer-controlled treatment chamber, which permanently and irreversibly rearranges the molecular structure of metal to be more uniform and evenly distributed, thus promoting longer life and stability while reducing maintenance expenses, part failure and metal deterioration caused by corrosion.
To qualify for the AFWERX Challenge competition, 300 Below, Inc. submitted a proposal in conjunction with Prof. Diran Apelian, of the Institute of Design and Manufacturing Innovation (IDMI) at the University of California, Irvine (UCI). 300 Below's research aims to improve aircraft shelters and other military base materials, and was selected for its potential to improve strength and durability of building structures, imparting better structural resiliency for joints, weldment areas, and other weak points in building materials while simultaneously reducing corrosion and improving wear resistance up to 300%.
A second project is proposed between 300 Below, Inc. and ITAMCO, another AFWERX SBIR contract recipient building a 3D Printed Runway Project at Tyndall Air Force Base, which uses a honeycomb architecture with Phase Transforming Cellular Matrix (PXCM) geometry to mitigate loading and shear stresses. ITAMCO's energy absorbing material may be further stress reduced, and strengthened, by applying 300 Below's cryogenic treatment process to the 17-4 PH stainless steel and aluminum composition.
For the AFRSO Advanced Manufacturing Olympics, 300 Below emerged as a top 10 finalist for efforts improving aluminum alloys used in 3D-printed metal parts. In prior testing, additive manufacturing using 316 Stainless Steel, arguably the most utilized stainless steel in the US Air Force, yielded a 30% improvement in Micro-Vickers hardness post-cryogenic treatment, along with a 35% increase in residual compressive stress, plus a 17% decrease in the coefficient of friction, which indicates significant abrasive wear resistance improvements.
"Never before has our military been able to print a broken part on demand and ensure that its structural integrity attains similar properties to the same high expectations for a previously cast or machined item. 300 Below is proud to contribute to battlefield transformation, as we give our Warfighters a new magic wand to improve durability and reduce downtime for critical combat gear by 3D printing replacement parts in hours and days at the edge versus weeks and months spent waiting on parts to be sent from back home," said Peter Paulin, CEO of 300 Below.
The AFWERX Fusion 2020 Showcase featured 370 participating teams selected from a record breaking 1,500+ submissions received for the Base of the Future Challenge. 300 Below was one of 22 Panelists invited to showcase its technology live. Throughout the event teams pitched their solutions to a panel of subject matter experts from the relevant sectors of the Air Force. The top 92 selections were identified and invited to further engage with the Air Force during the week of August 31 with the hope of obtaining contracts. For a complete list of participating teams visit fusion.afwerxshowcase.com.
The Base of the Future theme was inspired by Tyndall Air Force Base in Florida, which was decimated by Hurricane Michael, a Category 5 storm that occurred in 2018. For decades, Tyndall was home to many generations of Airmen and their families. In the storm's aftermath, nearly 500 buildings were destroyed or damaged beyond repair. Fortunately, Congress approved a $3 billion military construction rebuild program, sparking hope that Tyndall would re-emerge stronger than ever before. The aspirational initiative seeks to create a robust installation that will become a universal symbol of innovation and excellence that can scale across the U.S. Air Force. To learn about Base of the Future Challenges, click here.
ABOUT 300 BELOW, INC.
300 Below, based in Decatur, Illinois, is the world's largest and oldest cryogenic processing company, in business since 1966. 300 Below's technology is an extension of metal heat treatment, imparting a -300˚F liquid-nitrogen-based quench over 36 hours to permanently and irreversibly rearrange molecular structures. Stronger, more stable parts are the result of using 300 Below's technology to extend life, reduce corrosion, and relieve stress imparted during manufacturing. 300 Below's technology is used by thousands of clients including DoD, NASA, aerospace and defense contractors, and major U.S. automotive manufacturers.
Learn more about 300 Below:
https://www.300below.com/
An overview of 300 Below's process for tooling:
https://www.300below.com/files/discovercryo.pdf
White paper and video about 300 Below's manufacturing technology innovation:
MetalUpgrade.com.
ABOUT AFWERX
Established in 2017, AFWERX is a product of the U.S. Air Force, directly envisioned by former Secretary of the Air Force Heather Wilson. Her vision of AFWERX — to solve some of the toughest challenges that the Air Force faces through innovation and collaboration amongst our nation's top subject matter experts. AFWERX serves as a catalyst to unleash new approaches for the warfighter through a growing ecosystem of innovators. AFWERX and the U.S. Air Force are committed to exploring viable solutions and partnerships to further strengthen the Air Force, which could lead to additional prototyping, R&D, and follow-on production contracts.
Featured Product
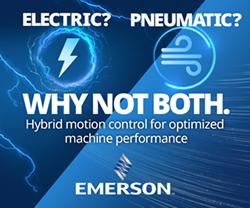