ForwardX Max 500 Receives CE Mark
ForwardX's 500kg autonomous mobile robot is clear for use in Europe
BEIJING, CHINA - Aug. 26, 2020 - ForwardX Robotics, a Beijing-based developer of visual Autonomous Mobile Robots, today announced its ForwardX Max 500 robots have achieved CE mark approval and are now certified for use across Europe. CE marking indicates that the Max 500 visual Autonomous Mobile Robots (vAMRs) now adhere to the European Union's directives and standards for health, safety, and environmental protection.
"Our Max 500 vAMRs give warehousing and manufacturing facilities the ability to automate dangerous, time-consuming tasks. While already available across Asia and North America, achieving the CE mark ensures that our Max solutions can be implemented in Europe in the future, where demand for flexible automation solutions is rising quickly," said Viktor Wang, Senior Product Director at ForwardX Robotics. "From speaking to our customers, a key benefit of our Max solutions is the increased safety they provide. With full-coverage 360-degree obstacle detection and avoidance, workers can collaborate with our robots worry- and accident-free. Receiving the CE certification solidifies just how safe our robots are."
With a maximum payload of 500kg (1100lbs), ForwardX developed the Max 500 AMRs to automate a range of costly workflows within manufacturing and logistics environments. Using a vision-first approach to realize a deeper understanding of the environment, Max 500 robots can be used to automate factory workflows like raw material delivery and Work-in-Progress (WIP) movement, in addition to warehouse workflows like putaway and pick-to-pallet.
Designed specifically for high-payload movements, the Max range of vAMRs consists of a number of tailored models designed to fit different customer requirements, with 200kg and 500kg models and lift functionality available. Through ForwardX's f(x) fleet management software, the ForwardX Flex and Max range of vAMRs can be implemented within the same facility operating as an intelligent workforce alongside human workers, with f(x) acting as a data hub and centralized command center responsible for coordinating each vehicle as part of a wider fleet.
In order to conform to the CE standards for health, safety, and environmental protection, ForwardX ensures its Max 500 vAMRs are designed and manufactured to the specific requirements of the directives and standards outlined below:
• Machinery Directive (2006/42/EC) covers the safety aspects of machinery and certain parts of machinery
• Electromagnetic Compatibility (EMC) Directive (2014/30/EU) ensures that electrical and electronic equipment does not generate, or is not affected by, electromagnetic disturbance.
Standards
• EN 61000-6-4:2007 +A1:2011
• EN 61000-6-2:2005
• EN 1525:1998
• EN 1175-1:1998 +A1:2011
• EN ISO 12100:2010
• EN ISO 13849-1:2015
"What we're seeing with regard to automation in Europe is no different than what we're seeing in Asia-Pacific or North America. Demand for flexible automation is growing and ForwardX is determined to make our solutions available to any business looking for a solution that delivers immediate results," said Nicolas Chee, Founder and CEO at ForwardX Robotics. "So far, our customers have been able to achieve amazing results across a number of supply chain functions. We want to continue to deliver these results across the globe to help companies stay ahead in a highly-competitive market."
About ForwardX Robotics
ForwardX Robotics is a global technology leader in the fields of AI and Robotics, possessing over 160 patents pending and a team of over 180, including 120 engineers of which 10 hold PhDs. With team members hailing from top universities and leading companies, ForwardX is comprised of the world's top computer vision scientists and robotics experts as shown by its award-winning work, such as 2 1st-Place Prizes at TRECVID and 1st Place Prize for IEEE's VOT-RT.
Featured Product
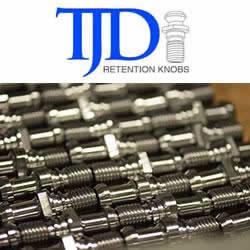
T.J. Davies' Retention Knobs
Our retention knobs are manufactured above international standards or to machine builder specifications. Retention knobs are manufactured utilizing AMS-6274/AISI-8620 alloy steel drawn in the United States. Threads are single-pointed on our lathes while manufacturing all other retention knob features to ensure high concentricity. Our process ensures that our threads are balanced (lead in/lead out at 180 degrees.) Each retention knob is carburized (hardened) to 58-62HRC, and case depth is .020-.030. Core hardness 40HRC. Each retention knob is coated utilizing a hot black oxide coating to military specifications. Our retention knobs are 100% covered in black oxide to prevent rust. All retention knob surfaces (not just mating surfaces) have a precision finish of 32 RMA micro or better: ISO grade 6N. Each retention knob is magnetic particle tested and tested at 2.5 times the pulling force of the drawbar. Certifications are maintained for each step in the manufacturing process for traceability.