COVID-19: Incodema Uses MC Machinery’s CO2 Laser, Wire EDM and Press Brake to Make Innovative PPE for Healthcare Workers
New York precision cutting and forming sheet metal manufacturer developed prototype and produced sanitizable, reusable face shields for front-line healthcare workers.
Incodema, an Ithaca, N.Y.-based precision cutting and forming sheet metal manufacturer specializing in prototypes, was approached by Ithaca's Cayuga Medical Center (CMC) in early April to produce face shields.
Most fast-turnaround personal protective equipment (PPE) uses non-sanitizable materials like foam or low-quality plastic and can only be worn once. Incodema decided to make face shields that could be sanitized and reused.
Incodema developed a design using stainless steel for the face shield's headband and Mylar plastic for the shield itself—both of which are materials that can be sanitized and reused. The stainless-steel headbands have holes in each end so that users can tighten them with a piece of removable elastic if desired.
The headbands were cut using MC Machinery's Mitsubishi 3015 LVPlus CO2 laser. The Mitsubishi MV1200-R wire EDM was used to create tooling that could bend parts on the Mitsubishi Diamond BB4013 press brake. However, the face shield design doesn't require use of a press brake machine—simple hand tools can also do the job.
Within a week, Incodema was able to produce and evaluate three different revisions, with user input from CMC, before settling on a final design. Incodema presented the face shields to the CMC team right before they headed to New York City to treat coronavirus patients. The company has made the designs and instructions available to everyone on its website, https://www.incodema.com/about-us/face-shield.
Featured Product
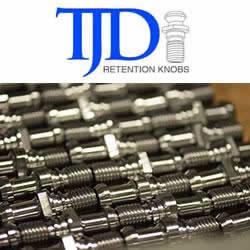
T.J. Davies' Retention Knobs
Our retention knobs are manufactured above international standards or to machine builder specifications. Retention knobs are manufactured utilizing AMS-6274/AISI-8620 alloy steel drawn in the United States. Threads are single-pointed on our lathes while manufacturing all other retention knob features to ensure high concentricity. Our process ensures that our threads are balanced (lead in/lead out at 180 degrees.) Each retention knob is carburized (hardened) to 58-62HRC, and case depth is .020-.030. Core hardness 40HRC. Each retention knob is coated utilizing a hot black oxide coating to military specifications. Our retention knobs are 100% covered in black oxide to prevent rust. All retention knob surfaces (not just mating surfaces) have a precision finish of 32 RMA micro or better: ISO grade 6N. Each retention knob is magnetic particle tested and tested at 2.5 times the pulling force of the drawbar. Certifications are maintained for each step in the manufacturing process for traceability.