Facilities Revisit Lift Covers for Preventive Safety As ISO 14120 Guarding Standard Replaces EN 953
The Liftgard design offers greater durability than traditional stitched covers. Lesser covers use steel rods that must be installed into fabric pockets. Through repeated operation, the ends of those rods often start to work free of the pockets, compromising the durability and the appearance of the cover.
March 3, 2020 - Lift table skirting may be a practical method of guarding pinch point hazards to increase safety and comply with standard ISO14120 ("Safety of machinery - Guards"), yet some varieties of lift skirting provide little more than dust protection. Liftgard(R) bellows completely enclose a scissors lift table to mitigate unintentional contact with pinch points. Dynatect's manufacturing process produces rigid sides free of stitching, protruding rods and/or wires.
The Liftgard design offers greater durability than traditional stitched covers. Lesser covers use steel rods that must be installed into fabric pockets. Through repeated operation, the ends of those rods often start to work free of the pockets, compromising the durability and the appearance of the cover. In contrast, Liftgard Covers feature aluminum extrusions that are formed and attached to the material to reduce potential wear points, improve appearance and increase the structural rigidity of the cover. The stitch-less, pleated bellows results in an attractive appearance for the modern facility. The standard features include traditional safety yellow material, a zipper, and vented corners for uniform air flow during movement. Options include custom colors and logo branding. Pre-assembled Liftgard covers are folded for efficient shipping, then unfolded for easy installation in minutes.
Several mounting options allow customers to choose a convenient attachment point that is suitable to their table design. Liftgard can be easily modified for special applications. Dynatect also manufactures other styles of bellows and protective covers for the bases of medical lift tables and various industrial applications.
Liftgard lift covers are manufactured in New Berlin, Wisconsin and supported by a nationwide network of over 60 technical field sales representatives who can be found on the Dynatect website. More information including a summary brochure, can be found online at: dynatect.com/liftgard.
About Dynatect
Dynatect delivers custom motion and protection for machines with deep application knowledge, diverse product offering, and a customer responsive sales philosophy. Dynatect provides engineering and manufacturing for custom applications which improve human-machine safety and machine uptime. Dynatect continues to build on its customer experience through improving service differentiation, expanding product portfolio, and reducing lead times. Visit www.dynatect.com.
Featured Product
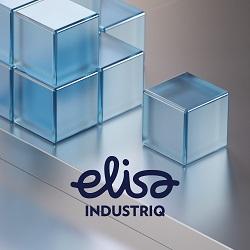