Press Release: Unique Powder Outperforms In Additive Manufacturing Aerospace-Ready Quality Tests
Test results on powder developed by Equispheres, exceed expectations, demonstrating ability for AM production of lighter, stronger parts, faster than ever.
OTTAWA, ONTARIO: Equispheres today released the results from the first phase of powder testing by a facility specializing in the certification of materials for aerospace, space and defense applications. The results confirmed Equispheres' powder allowed for a 50% increase in production speeds and a 20-30% increase in a-basis mechanical performance (a design allowance specification regulated in aerospace applications). These results serve as a major milestone for Equispheres as they validate the bold claims the company has made to date.
"The unique properties of our powder, including the high sphericity, narrow particle size distribution and low surface area results in significantly increased packing density. This allows an increase of powder layer thickness by a factor of 2 which significantly increases build speed." Equispheres' CTO, Dr Martin Conlon, explains, "Most importantly, this boost to build speed does not come with a mechanical performance penalty. Instead, the uniform nature of our powder ensures that parts are produced with reliable and consistent mechanical properties. The minimal variance in our performance results provides design engineers the statistical confidence to produce stronger, lighter parts."
_____________
"The additive manufacturing industry has been struggling with slow production speeds and poor-quality feedstock. We are excited that our unique powder can help resolve both critical issues."
- Kevin Nicholds, CEO, Equispheres
_____________
The comprehensive series of coupon printing and testing provided the following key technical results, contributing to overall faster production speeds and increased performance of produced parts:
- Layer thickness: 60 um
- Mechanical performance ‘as printed':
- Ultimate Tensile Strength (MPA): 449 ± 16
- Yield Strength (MPA): 272 ± 12
- Elongation (%): 6.4 ± 1.7
This news comes on the heels of results from a study by McGill University where Equispheres' aluminum alloy powders were found to enable sintering with binder jet printing technology, a combination which was not previously feasible but has major implications for mass AM production. Now, with impressive third-party validation and strong commercial demand, Equispheres is launching new equity financing to aggressively grow and unlock the vast potential of Additive Manufacturing.
Equispheres CEO, Kevin Nicholds, now aims to get the powder onto the market on a larger scale with a focus on long-term partnerships, "The additive manufacturing industry has been struggling with slow production speeds and poor-quality feedstock. We are excited that our unique powder can help resolve both critical issues."
About Equispheres:
Equispheres is a materials science technology company focused on additive manufacturing applications. Equispheres focuses on engineering and providing ultra-high-performance, mono-sized metal powders and invests heavily in R&D around metallurgy and alloy development.
Contact:
Doug Brouse
613-324-7956
doug.brouse@equispheres.com
Website: www.equispheres.com
Twitter: @equispheres
Featured Product
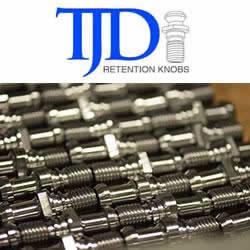