3D Systems and Antleron Collaborating to Accelerate 3D Printing Biomedical Breakthroughs
3D Systems' MultiJet Printing (MJP) and Figure 4 technologies combined with Antleron's bioengineering expertise lay foundation for groundbreaking bioprinting solutions with potential to improve personalized patient care
Today, 3D Systems (NYSE: DDD) and Antleron are announcing a collaboration, intended to play a pivotal role in advancing and accelerating breakthroughs in the biomedical industry. Bringing together two industry pioneers - 3D Systems for 3D printing technologies and healthcare expertise, and Antleron for leadership and innovation in the development of regenerative products and personalized patient care - the companies will collaborate to support Antleron's development of bioprinting solutions utilizing 3D Systems' printing technologies.
Antleron has created an R&D facility at their headquarters in Leuven, Belgium - a location known as an incubator for medical and life science innovation, including regenerative medicine, to support and validate customer projects in the field of 3D bioprinting. Antleron's 'living therapy factory' merges cells, biomaterials, biologics, bioreactors and 3D Systems printers to accelerate the engineering of living therapies. Using quality-by-design and artificial intelligence the Antleron multidisciplinary specialists translate these core technologies into pioneering workflows that turn cells into therapies.
The 3D Systems/Antleron relationship addresses solutions for medical device and advanced therapy medicinal product (ATMP) applications, incorporating a variety of innovative technologies that are of benefit to biomedical manufacturing process, beginning with 3D Systems' ProJet® MJP 2500 and Figure 4® 3D printers and existing portfolio of 21 biocompatible, USP Class VI materials; 3D Sprint® and 3DXpert® software, and post-processing equipment and processes. The goal is to establish a flexible, scalable Digital Factory approach, built on modular, closed parametric processes which include digital monitoring and quality control for risk mitigation. An example is to advance the way cells and tissues are grown to enable the transition from a static 2D to bioreactor-based 3D cell culture. This can lead to new ways to manufacture functionalized medical implants, vaccines, cell therapies, and living tissues.
According to Antleron CEO, Jan Schrooten, "The vision of Antleron is to sustainably bring living therapies into the clinic. 3D printing is key to this endeavor, and we are eager to collaborate with 3D Systems and its experts. I look forward to the pioneering solutions we'll be able to achieve to elevate the efficacy of bioprinting and extend its biomedical application reach."
"3D Systems is excited about working with Antleron as they explore bioprinting, and especially their capability to develop end-to-end solutions utilizing the 3D Systems' state of the art printing platforms and materials," said Chuck Hull, co-founder and chief technology officer, 3D Systems. "As we look to the future, bioprinting and regenerative medicine are large opportunities for 3D printing, and we look forward to expanding the role 3D Systems will play in these exciting fields."
At Formnext 2019 to be held November 19-22, 3D Systems (booth D03, hall 12.1) and Antleron will exhibit for the first time what is in store for next-generation medical applications with the ProJet MJP 2500 printer and VisiJet® materials.
About 3D Systems
More than 30 years ago, 3D Systems brought the innovation of 3D printing to the manufacturing industry. Today, as the leading AM solutions company, it empowers manufacturers to create products and business models never before possible through transformed workflows. This is achieved with the Company's best-of-breed digital manufacturing ecosystem - comprised of plastic and metal 3D printers, print materials, on-demand manufacturing services and a portfolio of end-to-end manufacturing software. Each solution is powered by the expertise of the company's application engineers who collaborate with customers to transform manufacturing environments. 3D Systems' solutions address a variety of advanced applications for prototyping through production in markets such as aerospace, automotive, medical, dental and consumer goods. More information on the company is available at www.3dsystems.com.
About Antleron
Antleron is a young R&D company on a mission to enable personalized manufacturing 4.0 in the domain of advanced therapies. The company's nimble team is revolutionizing medicine by merging the potential of cells, biomaterials, biologics, 3D printing and bioreactors to accelerate the engineering of living therapies - empowering patients with fully personalized, regenerative care. Antleron translates core technologies including additive manufacturing (AM), quality-by-design and artificial intelligence into pioneering workflows that turn cells into living therapies to eventually make organ manufacturing a reality. To support its mission, Antleron's business philosophy is to create sustainable ventures that bring living, personalized therapies from idea to patient through risk & reward sharing partnerships. From the company's headquarters in Belgium, Antleron operates at the cutting edge between life sciences and technology within Europe's leading biotech ecosystem. More information on the company is available at www.antleron.com.
Featured Product
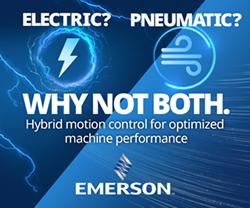