ADDERE RELEASES WHITEPAPER ON LWAM MANUFACTURING
In the paper, ADDere addresses some of the more important aspects to consider, from beginning the design phase into using the systems for production. Knowing what’s possible and the best practices for the process reduces surprises and ensures success. It also opens an array of opportunities where the large-scale additive system can really make an impact in the production process.
With the increase in demand for very large metal component additive manufacturing, ADDere has put together a few best practices for the 3D metal printing process. This whitepaper aims to streamline and enhance the printing experience for potential customers.
Although ADDere works differently than powder-based systems, it also has the potential to change the way modern manufacturing operates as much or more than current SLS technologies. With the ability to make casting-grade parts at sizes that go well beyond what people think is possible in metal additive today, ADDere could vastly reduce product development time. It can also play a critical part in speeding up production times for large scale, low run industries like off-highway machines, aerospace, defense and energy production.
"When a company needs to test iterations of metal parts at scale, that process doesn't have to look like half a year or more. It can look like a few weeks or months with ADDere," says Pete Gratschmayr VP Sales & Marketing. "It's hard to put a price on saving that much time. "
In the paper, ADDere addresses some of the more important aspects to consider, from beginning the design phase into using the systems for production. Knowing what's possible and the best practices for the process reduces surprises and ensures success. It also opens an array of opportunities where the large-scale additive system can really make an impact in the production process.
"The ADDere system has proven its capability in reducing time to market for products that would previously rely on casting processes," mentions Scott Woida, ADDere president, "delivering the same grade part in days rather than months - and we're talking about a part that can be the size of a truck transmission or larger. That's a game-changer."
While using the LWAM process may not require large changes to existing processes or parts, there are aspects that help ensure the best possible outcomes, like factoring the same sort of finishing necessary for cast parts.
To get the most out of ADDere's Laser Wire Additive Manufacturing process, download Five Design Tips of Laser Wire 3D Printing Today.
ADDere is a division of Midwest Engineered Systems Inc. (MWES), an innovator and leader in complex production systems integration. MWES has been providing custom robotic automation solutions for over 28 years. Its extensive industry experience, broad range of product knowledge, and customer-focused approach make Midwest Engineered Systems a leading production line supplier with a solid reputation for quality, service, and value. The firm's customers include some of the largest manufacturing companies not only in the Midwest, but across the globe who rely on MWES to provide and support large production systems.
Featured Product
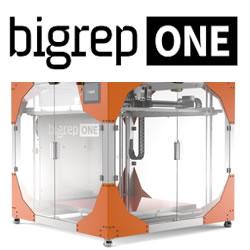