ASTM International Additive Manufacturing Center of Excellence Awarded $1.2M by America Makes
This $1.2-million investment will help address the lack of consensus on best practices and standards for materials handling and post-processing in using Selective Laser Melting (SLM) to make critical parts.
W. CONSHOHOCKEN, Pa., Dec. 21, 2018 - On Tuesday, ASTM International became the first standards development organization to win an award from America Makes, the National Additive Manufacturing Innovation Institute for the U.S. The "Advancing Additive Manufacturing Post-Processing Techniques" (AAPT) award of $800,000, funded through the Air Force Research Laboratory (AFRL), will be supplemented by $400,000 in in-kind support from project team partners.
This $1.2-million investment will help address the lack of consensus on best practices and standards for materials handling and post-processing in using Selective Laser Melting (SLM) to make critical parts. This currently leads to high variability, challenges in qualifying parts, and high post-processing costs which are all barriers to wider adoption of additive manufacturing.
ASTM Internationals Additive Manufacturing Center of Excellence (www.amcoe.org) - one of two awardees - will focus specifically on: determining the mechanical performance debit of using as-built additively manufactured components, understanding how this changes with application of Hot Isostatic Pressing, testing the values by burst-testing thin wall components with narrow flow channels, and ultimately publishing standards based on these results.
In addition to several of the centers existing partners (Auburn University, NASA, manufacturing technology innovator EWI, Wichita State Universitys National Institute for Aviation Research), the project team includes Quintus Technologies, Carpenter Technologies Corporation, Aerojet Rocketdyne, Rolls Royce Corporation, Honeywell Aerospace, GE Aviation, and Raytheon. The project will begin in early 2019.
In making the announcement, America Makes executive director Rob Gorham said, "These project teams have outlined interesting approaches to better understanding mechanical and material properties during heat treatments. As a result, we anticipate the projects will yield important gains in process control, certified processes, and the qualification of materials and parts, which will all be instrumental in reducing post-processing costs, one of the biggest barriers to the wider adoption of AM technologies."
"We are thrilled to take our longstanding partnership with America Makes to the next level through this major award," said Dr. Mohsen Seifi, director of global additive manufacturing programs at ASTM International, which signed a memorandum of understanding with America Makes in 2013. "Our center of excellence is uniquely positioned to illuminate the path toward high-quality, consensus-based standards that support new AM technologies and post-processing techniques."
Dr. Nima Shamsaei, director of the National Center for Additive Manufacturing Excellence at Auburn University, submitted the project teams application as the principal investigator and on behalf of the ASTM International Additive Manufacturing Center of Excellence. He added, "All of the partners, including our world-class researchers here at Auburn, are excited to start collaborating more closely in this crucial area. The potential for this project to help transform sectors and industries in the years to come simply cant be underestimated."
Dr. Alex Kitt, product manager at Buffalo Manufacturing Works (operated by EWI) was also a key contributor to the winning proposal. "This work demonstrates the commitment of government, industry and academia to collaborate on research that will lead to the development of impactful AM standards. We are confident these standards will increase adoption and confidence in this cutting-edge technology. EWI is excited to lend its expertise and capabilities to this joint effort."
About ASTM International
Committed to serving global societal needs, ASTM International positively impacts public health and safety, consumer confidence, and overall quality of life. We integrate consensus standards - developed with our international membership of volunteer technical experts - and innovative services to improve lives… Helping our world work better.
Featured Product
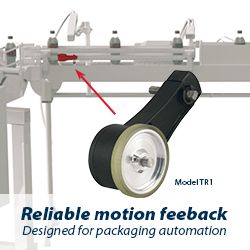