SME, AMT and Leading Companies Partner to Bring Advanced Manufacturing Technology to the Smart Manufacturing Experience in Boston this Spring
This spring, leaders in advanced manufacturing delivering solutions and technology will come together in Boston for the first Smart Manufacturing Experience. With manufacturing evolving at a rapid pace, the Smart Manufacturing Experience 2018 will bring real-world technologies to life through practical applications. The event will focus on topics including: • Automation and robotics • Advanced materials • Precision machining and measurement • 3D printing and scanning • Digital manufacturing • Industrial IoT and big data
SME and AMT, the Association For Manufacturing Technology, are ramping up for the leading smart manufacturing event in the U.S.: the Smart Manufacturing Experience 2018. The event, which will take place April 30 through May 2, at the Boston Convention Center, will be co-sponsored by SME, AMT and founding partners Mazak, The Robert E. Morris Co., and Methods Machine Tools, all leaders in advanced manufacturing delivering solutions in additive manufacturing, digital manufacturing, automation and more to major manufacturers around the world. Smart Manufacturing Experience 2018 was created to ensure that industry players are engaged and fully prepared with the most current smart manufacturing technologies.
This event will focus on how advanced technologies such as additive manufacturing and 3D printing, automation and robotics, advanced materials, precision machining, precision measurement and 3D scanning, digital manufacturing, and the Industrial IoT (Internet of Things)/big data are revolutionizing the industry. These technologies provide full factory visibility, asset tracking, product lifecycle management, enhanced part geometries, improved part performance, reduced complexity, lights-out manufacturing, repeatable quality, responsive work environments and more.
"Partnering with companies such as Mazak, The Robert E. Morris Co., and Methods Machine Tools ensures that the Smart Manufacturing Experience will deliver real solutions to manufacturers that they can use today," said Debbie Holton, vice president, SME Events & Industry Strategy. "These companies are committed to advancing manufacturing productivity, performance, and profitability using smart manufacturing technologies throughout the manufacturing value chain."
The Robert E. Morris Co. and Methods Machine Tools will feature some of their most well-known product lines including 3D Systems, Desktop Metal, Okuma, and Matsuura, while Mazak highlights its commitment to digital manufacturing, which extends to the factory at its U.S. headquarters that is MTConnect enabled and digitally connected.
"It is our goal, every day, to help our customers do more with less," said Lou Olson, president, The Robert E. Morris Co. "The Smart Manufacturing Experience will be an excellent opportunity to engage with area manufacturers and other advanced technology suppliers who share our passion for improving manufacturing productivity, profitability, and quality with the most highly sophisticated tools and resources currently and imminently available to them."
Smart manufacturing encompasses the tools and processes that allow manufacturers to see and react to the performance of their machines and integrated systems with analytics in real time. It enables machines to talk to one another, control operations remotely, predict challenges and even share live data throughout the supply chain. All of this makes way for improved productivity, increased energy efficiency, higher-quality products, safer plant floors, and better employment opportunities.
This manufacturing transformation is also referred to as the Fourth Industrial Revolution. From small shops to global OEMs, the demands of a "smart manufacturing enterprise" require new technologies, as well as the willingness of manufacturers to incorporate advancements as part of their operations. In a 2016 Advanced Manufacturing Media survey, 43 percent of manufacturers polled said they were considering/evaluating the implementation of smart manufacturing solutions into their operations over 24 months. As more manufacturers add new technological advancements to their operations, the industry will realize exponential growth. According to a new Grand View Research study, the global smart manufacturing market is estimated to reach $395.2 billion by 2025 - up from $172.34 billion in 2016.
"Manufacturing is in an era of disruptive transformation unlike anything seen before," said Douglas K. Woods, president, AMT. "It is imperative that companies learn how to best implement and leverage these technologies to stay competitive, whether its advanced robotics, artificial intelligence, machine learning, or any other technology that supports the connected factory. We are excited to have Mazak, the Robert E. Morris Co. and Methods Machine Tools on board to sponsor an event focused on the worlds most advanced smart manufacturing technology."
To learn more about the Smart Manufacturing Experience, visit www.smartmanufacturingexperience.com.
Featured Product
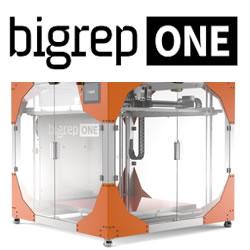