PostProcess Technologies Automates 3D Post-Printing for Advanced Medical Models at Johns Hopkins School of Medicine
The Johns Hopkins University's Carnegie Center for Surgical Innovation implements the CENTI solution to remove support material from Polyjet parts.
PostProcess Technologies, the Buffalo, NY-based company pioneering automated post-printing solutions for the industrial 3D printing market, announced today an agreement with the Johns Hopkins Universitys Carnegie Center for Surgical Innovation to automate post-printing technologies for the centers 3D printing facility.
Using 3D printing to put patient-specific organ models into the hands of surgeons, the Johns Hopkins facility has significantly decreased their overall cycle time and improved consistency with the PostProcess solution. Johns Hopkins 3D printing efforts extend beyond surgeon models to printing for teaching and education, engineering prototypes, custom printed lab devices, and patient education models.
Juan R. Garcia, MA, CCA, Associate Professor at the Johns Hopkins University School of Medicine and Director of the Facial Prosthetics Clinic and of 3D Printing Services, worked with PostProcess to implement their CENTI solution. The CENTI machine is used to remove support material from PolyJet parts in a compact bench-top footprint. The comprehensive PostProcess solution incorporates custom software, driving optimized agitation and energy delivery, and proprietary detergents formulated specifically for 3D printed materials to remove only the support structure and leave the build material in great condition.
To learn more about 3D printing at Johns Hopkins, please visit: http://medicalart.johnshopkins.edu/3d-printing-advanced-3d-technologies/
Featured Product
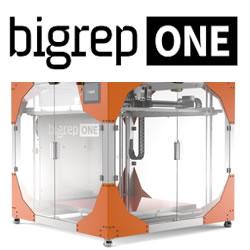
BigRep ONE: Large-Scale 3D Printing
The BigRep ONE is an award-winning, large-format 3D printer at an accessible price point. With over 350 systems installed worldwide, it's a trusted solution for prototyping and production by designers, innovators, and manufacturers alike. Featuring a massive one-cubic-meter build volume, the fast and reliable ONE brings your designs to life in full scale.