DSM sharpens focus on Additive Manufacturing
New organization builds on deep sector expertise and collaboration
Royal DSM, a global science-based company active in health, nutrition and materials, today announces a new approach for its additive manufacturing (AM) activities. By aligning all its AM activities within the Materials cluster and promoting a partnership approach, DSM can provide customers an open and flexible infrastructure. This will help customers to find exactly the right materials and production systems for their applications.
The new customer-centric organization will build on experience and expertise from all of DSMs existing materials businesses, combining deep market segment-specific application understanding and expertise in all polymer AM processing technology platforms.
After two decades in which DSM established itself as a major player in the AM area with its Somos® business in resins for stereolithography (SLA) and Digital Light Processing (DLP), the company is now forming an integrated business - DSM Additive Manufacturing. By aligning all of its AM activities beyond SLA and DLP, DSM will offer Fused Filament Fabrication (FFF) as well as experience from years of research in Selective Laser Sintering (SLS), Multi Jet Fusion, Ink Jet and Binder Jet processes.
DSM will initially focus on four market segments in particular: healthcare, transportation, apparel and tools & electronics - all areas on the cutting edge of manufacturing and with strong commitments to AM. The aim is to help customers find exactly the right materials and production systems for their applications.
"Somos has provided us with a deep understanding of key market segments and end-customer needs in the AM space," says Hugo da Silva, VP of Additive Manufacturing at DSM. "We continue to introduce major innovations in SLA and DLP materials, but this is only a part of the total AM picture, and we want to cover the entire area."
"Right now, there is a lot of excitement around Fused Filament Fabrication and DSM has a growing portfolio of materials for this technology, including Novamid® polyamide and Arnitel® thermoplastic elastomer. But we intend to go much further, extending our innovation efforts - supported by technology partnerships and industry collaboration - to develop new solutions for SLS, Multi Jet Fusion, Ink Jet and Binder Jet. We also want to explore new and emerging technologies in AM as they graduate from research, giving us the industrys broadest solutions portfolio."
DSM Additive Manufacturing will have a strong focus on R&D and continuous innovation that will enable it to develop a broader, sustainable solutions portfolio.
Integral to DSMs future strategy in AM is what the company calls the ‘ecosystem approach. Having partnerships and collaboration as part of the foundation of the new organization allows DSM to provide customers with an open and flexible infrastructure. "Providing the right material and the right platform for specific applications is key to accelerate adoption of 3D Printing into manufacturing. Collaboration in the industry will allow more applications to benefit from the great advantages of AM, at an affordable cost", says da Silva.
Taking AM into the industrial manufacturing mainstream
"AM is quickly evolving from a prototyping technology on the fringes of manufacturing into a mainstream discipline, offering tangible value and economically viable benefits to large industrial companies and eventually through to end-users," says Da Silva. "Mass customization and small volume production using AM are now a reality, and as the sector evolves and matures to reflect new, disruptive business models and shifting customer behaviours, so must we. SLA is our heritage; however we can play in all polymer printing technologies, we can deliver in all areas. What is important is what is best for the customer."
DSM has already various collaborations through-out the additive manufacturing ecosystem such as the recent "One DSM" framework technology partnership agreement with Toyota Motorsport GmbH (TMG), a 100% subsidiary of the Toyota Motor Corporation. The agreement involves all DSM businesses active in supplying materials and technology to the automotive sector - Somos, Engineering Plastics, and also Dyneema® ultrahigh molecular weight polyethylene fiber.
DSM has also acquired the HP Multi Jet Fusion Materials Development Kit in an effort to jump-start 3D powder development for HPs Jet Fusion 3D printing solution. DSM plans to collaborate with HP in the development of materials and bring innovative solutions to the market.
DSM Additive Manufacturing at formnext 2017
DSM will be exhibiting at formnext 2017, the leading trade fair for Additive Manufacturing and the next generation of intelligent manufacturing solutions, taking place in Frankfurt, Germany on 14 - 17 November. Exhibits will emphasise the companys market focus in AM on transportation, medical, tools and electronics and apparel.
In Hall 3.0 on Stand C29, DSM will highlight:
Somos Taurus for under-the-hood applications. Somos Taurus is the first SLA material to bring the combination of thermal resistance, mechanical strength and impact performance that until now has only been achieved in AM using techniques such as FDM and SLS.
Novamid ID 1030-KS is the first material for FDM/FFF with a UL 94 V-0 rating, which makes possible the creation of UL-certified small-series FFF/FDM parts for industrial applications. Target applications include fuse boxes, low voltage switch gear, electronic housing, control gear, casings and connectors.
Arnitel ID 2060-HT offers an excellent combination of heat resistance (Continuous Use Temperature is 150°C), resistance to chemicals such as EGR (Exhaust Gas Regeneration) condensate and mechanical properties for demanding automotive applications under the hood such as hot and cold charge air ducts. Arnitel ID 2060-HT is easy to process and can easily be welded. This new filament can significantly reduce the development time of such engine components.
________________________________________
Featured Product
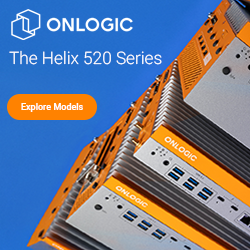
OnLogic's Helix 520 Series of Scalable Fanless Computers
The Helix 520 series utilizes the latest Intel Core Ultra processors with integrated edge AI capabilities to deliver exceptional performance and industrial-grade reliability for demanding applications in automation, robotics, machine vision, and more. Its unique modular design allows for flexible scaling of CPU and GPU performance, while robust connectivity and expansion options ensure seamless integration.