New Digital Servo Driver Improves Speed and Precision for Laser Beam Steering
Cambridge Technology Launches DC3000 Plus for laser marking applications
BEDFORD, Mass., Oct. 2, 2017 /PRNewswire/ -- Cambridge Technology, a business unit of Novanta Corporation ("Novanta"), announced today the launch of the DC3000 Plus, a new digital servo driver, adding to its product family of components and scan heads for laser beam steering.
The DC3000 Plus builds on the success of its predecessor, the DC3000, which applies digital state space controller technology to optimize speed in laser marking applications. With increased drive current and improved thermal management, the DC3000 Plus now offers higher marking speed and it accurately drives larger mirrors faster. These improvements expand the product line's capabilities in laser converting, micromachining, high power welding, and additive manufacturing applications.
"The new servo driver offers significant speed and performance advantages to our customers, including superior tracking performance and greater efficiency in high duty cycle applications," said Phil Martin, President, Cambridge Technology and Photonics Group President, Novanta. "Customers also benefit from the new self-calibration feature which streamlines integration of the DC3000 Plus into customers' systems and reduces machine downtime, simplifying service requirements."
The DC3000 Plus is part of a suite of products designed to meet the demands of advanced manufacturing applications. Key features include:
Increased precision for micro-vector scanning patterns in micromachining, wobble welding, and trepanning
Up to twice the throughput in high speed marking applications
Ease of integration and support with system diagnostics at each power-on and added protection from overheating during operation
For more information about the DC3000 Plus digital servo driver, visit www.cambridgetechnology.com. Cambridge Technology offers a broad range of analog, digital, and hybrid laser beam steering solutions, partnering with customers to enable maximum performance in fully-integrated systems.
About Cambridge Technology and Novanta
For almost 50 years, the Cambridge Technology business of Novanta has developed innovative beam steering solutions, including polygon- and galvanometer-based optical scanning components, 2-axis and 3-axis scan heads, scanning subsystems, high power scanning heads, and controlling hardware and software.
We collaborate with key OEMs to engineer products that meet their needs. Key market applications include advanced industrial processes including additive manufacturing, laser converting, laser marking, and via-hole drilling, and medical applications such as laser treatment and optical coherence tomography. Novanta (which trades publicly under its parent entity, Novanta Inc., NASDAQ: NOVT) is a trusted technology partner to original equipment manufacturers in the medical and advanced industrial technology markets, with deep proprietary expertise in photonics, vision and precision motion technologies.
Featured Product
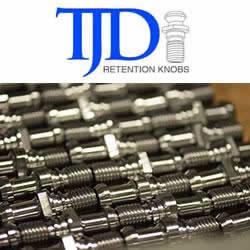
T.J. Davies' Retention Knobs
Our retention knobs are manufactured above international standards or to machine builder specifications. Retention knobs are manufactured utilizing AMS-6274/AISI-8620 alloy steel drawn in the United States. Threads are single-pointed on our lathes while manufacturing all other retention knob features to ensure high concentricity. Our process ensures that our threads are balanced (lead in/lead out at 180 degrees.) Each retention knob is carburized (hardened) to 58-62HRC, and case depth is .020-.030. Core hardness 40HRC. Each retention knob is coated utilizing a hot black oxide coating to military specifications. Our retention knobs are 100% covered in black oxide to prevent rust. All retention knob surfaces (not just mating surfaces) have a precision finish of 32 RMA micro or better: ISO grade 6N. Each retention knob is magnetic particle tested and tested at 2.5 times the pulling force of the drawbar. Certifications are maintained for each step in the manufacturing process for traceability.