Tethon 3D Launches Flexalite 3D Printing Resin Material
Flexalite is a new transparent flexible polymer resin for SLA and DLP 3D Printing
Tethon Corporation Inc. ("Tethon 3D") announces the release of a new 3D printing material. Flexalite® is a transparent and flexible photo-curing polymer resin for use in SLA and DLP 3D printing.
Flexalite is a polymer resin that requires no post processing steps after UV-based 3D printing, other than cleaning and additional UV curing as needed based on the design thickness. It is manufactured at Tethon 3Ds facility in Omaha, Nebraska and is immediately available worldwide in liter bottles by ordering from tethon3d.com.
About Tethon 3D
Tethon 3D is the world leader in ceramic materials for additive manufacturing. The company manufactures all its products in the United States and distributes globally. Tethon 3D manufactures resins and powders for SLA, DLP, CLIP and powder/jet binder 3D printing.
Additionally, the company provides service in 3D modeling, scanning and ceramic 3D printing, as well as 3D printing educational workshops and a residency program.
Tethon 3D holds several patents related to ceramic 3D printing materials, 3D printing processes and 3D printer hardware. For more information on Tethon 3D, visit http://www.tethon3d.com.
Except for statements of historical fact, all statements in this press release, including, but not limited to, statements regarding future plans, objectives and payments are forward-looking statements that involve various risks and uncertainties.
Featured Product
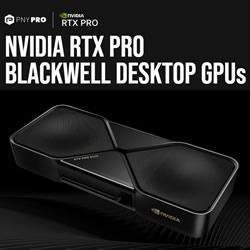
NVIDIA RTX PRO™ BLACKWELL DESKTOP GPUs N
NVIDIA RTX PRO™ - Built for Professionals - NVIDIA RTX PRO Blackwell Desktop GPUs feature the latest breakthroughs in AI, ray tracing, and neural rendering technology to power the most innovative workflows in design, engineering, and beyond.