Dolomite's Fluidic Factory recognized with R&D 100 Award
Dolomite, a world leader in microfluidics innovation, is celebrating the success of its Fluidic Factory 3D printer in the ‘Processing and Prototyping' category this year's R&D 100 Awards.
Dolomite, a world leader in microfluidics innovation, is celebrating the success of its Fluidic Factory 3D printer in the ‘Processing and Prototyping category this years R&D 100 Awards. This innovative system - the first commercially available 3D printer for fluidically-sealed devices - offers rapid, straightforward and reliable prototyping of microfluidic components, including chips, manifolds, connectors and other devices. Using cyclic olefin copolymer (COC) makes it easy and affordable to 3D print devices for almost any application.
The prestigious R&D 100 Awards are the ‘Oscars of Invention, providing a benchmark of excellence and identifying the top technology products of the past year. The winners are chosen by an independent panel of judges and the editors of R&D Magazine, who this year recognized the significant contribution the Fluidic Factory is making to the fast growing field of microfluidics. Its success highlights the potential of this system to further research and development in areas such as medical diagnostics, drug development, chemical synthesis, enzymatic bioconversion, biomedical assays and education.
Mark Gilligan, CEO of Blacktrace Holdings, commented: "The entire Blacktrace Group is delighted that we have once again been successful at the esteemed R&D 100 Awards, highlighting our strengths in innovation and developing novel technologies with real world applications. This award recognizes how the Fluidic Factory is helping to push the boundaries of microfluidics, enabling faster and more cost-effective prototyping and opening up new avenues of research."
To find out more, please visit www.dolomite-microfluidics.com/webshop/fluidic_factory
Featured Product
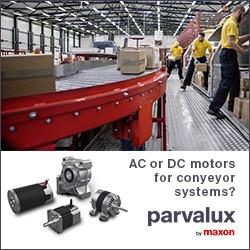