IMTS 2016 -- SPRING Technologies highlights NCSIMUL MACHINE and NCSIMUL CAM as manufacturers usher in Industry 4.0
See full demonstrations of these advanced, award-winning software solutions and more in Booth E-3267
Jun 28, 2016 -- SPRING Technologies, vendor of software that optimizes the use of CNC machines, will show visitors at IMTS 2016 how its "NCSIMUL SOLUTIONS 10" all-in-one digital suite can truly usher in the "smart" factory. In Booth E-3267, the company is focusing on its most popular modules in the suite - NCSIMUL MACHINE and NCSIMUL CAM.
NCSIMUL MACHINE
NCSIMUL MACHINE is an innovative CNC software solution providing realistic simulation of the machining process. Users can simulate, verify, optimize and review machine programs based on the actual characteristics of the machine tools. Three-dimensional graphics help to avoid machining crashes while powerful algorithms and embedded process-based knowledge enable cutting conditions to be optimized. NCSIMUL MACHINE verifies programs in three steps: investigates and corrects coding errors, simulates to locate collisions and correct motion errors, and validates the program. The benefits are many, including reducing the time spent on debugging programs; preventing the costly risk of spindle collision, tool breakage and scrap; and improving cycle times and process optimization efficiencies.
SPRING Technologies has also addressed the increased use of composite materials in manufacturing by developing NCSIMUL Composites and welcomes inquiries about this product at IMTS 2016. New algorithms in NCSIMUL MACHINE enable the simulation of fiber lay-ups with the initial media, the already laid material and roller position taken into account. The software offers a realistic display of the complete 3D model of the final part, selectively displaying each layer.
NCSIMUL CAM
This module, introduced last year and recent winner of the "Innovation Trophies" award at France's PARIS INDUSTRIE 2016 trade show, streamlines the existing CAM process to simplify CNC programming. It allows users to change, in one click, the target machine without any reprogramming efforts. From the main CAD/CAM program or machine controller G-code, NCSIMUL CAM generates programs for any machine tool that are verified and optimized without an external post-processor. It takes into account the kinematics of the machine tool, machine controller, cutting tools and conditions. This efficiency results in lead-time reduction from prototype to production and in repurposing legacy programs to new machines.
"We are excited about IMTS 2016," said Silvère Proisy, North American Operations Director for SPRING Technologies. "In North America, our customers on average save 90% of their machine setup time, a $500,000 a year in production time by optimizing feed rates and more than $100,000 dollars annually on machine crash avoidance. We invite all who are looking to improve their machining OEE (Overall Equipment Effectiveness) to see our demonstrations and for those moving towards the completely digital environment in their shops. It's often easier to show than explain our products, and we enjoy seeing the light go on in visitors' eyes when they quickly understand the new level of advancement and benefits that NCSIMUL solutions can bring to their factories in a very cost-effective way."
Mr. Proisy will be touching on all of these topics during the IMTS Conference on Monday, September 12 at 11:00 am in Room W194-A with a presentation entitled, "Boost Your Traditional Programming Process: Simplicity and Flexibility".
Featured Product
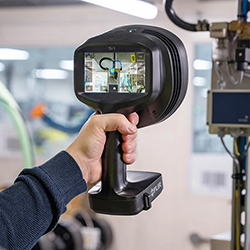
Affordable Excellence: The Go-To Tool for Finding Compressed Air Leaks
Find compressed air leaks fast with FLIR's new cutting-edge Si1-LD acoustic imaging camera. Leveraging advanced ultrasonic technology and onboard analytics, this affordable camera pinpoints leaks and quantifies incurred losses even in the nosiest environments. Upgrade your maintenance routine with the cost-effective FLIR Si1-LD - significantly reduce energy costs and increase system uptime. Get Started Today.