Plural Additive Manufacturing Opens New Facility in Oregon
Delivers up to 50% savings on low-volume plastic parts and prototypes to companies in the United States
Plural Additive Manufacturing announces the opening of its new facility at 6455 Lakeview Blvd, Suite B., Lake Oswego, Oregon. The office and production areas will support the US market with equipment and services for a new generation of industrial 3D printing and Additive Manufacturing systems.
Compared to traditional manufacturing processes used for low- to mid-volume parts manufacturing, Plurals technologies achieve up to 50% cost per part savings. Plural achieves their savings and advanced performance through a number of factors such as:
Non-proprietary, open source, engineering grade thermoplastics
Three print nozzles for multi-material and soluble support material printing
A liquid-cooled print head enabling a wider range of materials including hi-temp and clear/FDA approved variants
HEPA air filtration, providing a healthy, particle, and odor free environment
Low acquisition, operation, and maintenance costs
Underscoring Plurals mission, says Tom McKasson, co-founder of Plural: "The terms 3D printing and Additive Manufacturing are often used interchangeably. The fact is, AM includes 3D printing and much more as part of a lean process in order to cost-effectively deliver low- to mid-volumes of plastic parts for end use applications."
ABOUT PLURAL
Founded by industry veterans, Plural is an innovative startup company providing industrial solutions for additive manufacturing and rapid prototyping.They offer a wide range of thermoplastic materials using advanced 3D print technology and processes.
Plurals solutions are available through the company and its technology partners.
Featured Product
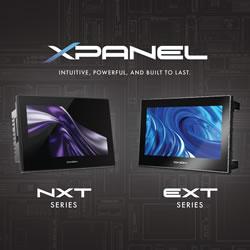
CIMON Xpanel eXT & nXT Series HMI
Introducing the Xpanel eXT and nXT series, advanced industrial HMI solutions that set a new standard for performance and usability. Utilizing our brand new Canvas HMI software for project creation, the Xpanel eXT and nXT series deliver a seamless and efficient user experience. They combine industrial-grade touch technology, powerful embedded OS hardware with a quad-core CPU, and an easy-to-use runtime platform. The Xpanel eXT and nXT series are specifically designed to optimize and streamline industrial operations, enhancing your HMI experience.