LAM 2016: Exploring the Multi-Faceted World of Additive Manufacturing
LIAs 8th annual Laser Additive Manufacturing (LAM®) Workshop welcomed over 170 attendees – over half of whom were new to the event – from 14 countries. They gathered in Orlando, FL on March 2-3 to discuss the latest developments in 3D printing, cladding and other revolutionary additive manufacturing (AM) methods.
LIAs 8th annual Laser Additive Manufacturing (LAM®) Workshop welcomed over 170 attendees - over half of whom were new to the event - from 14 countries. They gathered in Orlando, FL on March 2-3 to discuss the latest developments in 3D printing, cladding and other revolutionary additive manufacturing (AM) methods.
"New this year was a session dedicated to technologies (electron beam, arc welding and ultrasonic) that compete against lasers for additive manufacturing," said General Chair Paul Denney.
To begin this session, Professor Sudarsanam Suresh Babu from the University of Tennessee at Knoxville gave a keynote presentation that focused on recent advances in metal additive manufacturing, as well as the role in-situ process monitoring, computational monitoring and advanced characterization play in the field. Professor Babus discussion of AMs benefits, compared to traditional manufacturing methods, gave way to an overview of the additive manufacturing process - from geometrical conformity and topography optimization to size specific properties and beyond.
After gaining this background on alternative technologies, attendees learned about the selection process companies use when choosing the premier additive manufacturing processes for their needs. In addition, the first day also featured executives from leading companies, including DMG MORI, Concept Laser, Inc. and Optomec, Inc., who showcased new equipment available for AM.
Focusing on new AM approaches, Christoph Leyens from Fraunhofer IWS discussed precise laser metal deposition with wire and powder filling material, while TRUMPF Inc.s Frank Geyer compared the processes of laser metal deposition and laser metal fusion. After which Daniel Capostagno of SPI Lasers LLC, concluded the day with his presentation on fiber laser welding and cladding using filler wire.
With a focus on bridging the gap between additive manufacturing research and application, the second day began with a keynote address given by Professor David Bourell of the University of Texas at Austin. The Director of the Laboratory for Freeform Fabrication discussed the current status of additive manufacturing.
The days sessions also focused on both the national and global successes and challenges in AM with presenters from around the world. Tim Biermann of Fraunhofer ILT presented on LAM R&D centers in Germany, while Milan Brandt from RMIT University discussed the industry further in Australia.
Sharing the latest and greatest in additive manufacturing, LAM 2016 gave attendees a unique inside look at this rapidly-progressing manufacturing process. Alex Zappasodi of Polymet Corporation remarked, "A great show! Valuable information, great attendees and meticulously organized." James Tomich, who attended LAM for the fourth time this year, agreed and said, "If youre using lasers for AM, you dont want to miss LAM."
"Were looking forward to LAM 2017, when we return to Houston, TX," said Denney. "While the Oil and Gas industry is suffering from lower oil prices, we feel that there will still be a strong interest in laser cladding - a form of laser additive manufacturing - because it can lower production costs."
Visit http://www.lia.org/lam for updates on LAM 2017.
About LIA
The Laser Institute of America (LIA) is the professional society for laser applications and safety serving the industrial, educational, medical, research and government communities throughout the world since 1968. http://www.lia.org, 13501 Ingenuity Drive, Ste 128, Orlando, FL 32826, +1.407.380.1553.
Featured Product
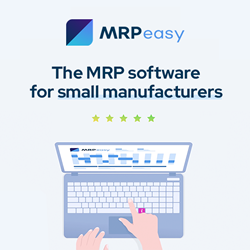