Baker Aerospace Adding 3D Metal Printing Capabilities
Significant expansion to Baker 3D Solutions division
(MACOMB TOWNSHIP, MI) - Established in 1992, Baker Aerospace Tooling & Machining Inc. has held fast throughout growth periods and recessions alike to a rigorous and straightforward philosophy -- continue to reinvest in technology. Capping what founders Scott and Kevin Baker are calling a "defining year," the company with 200+ employees and 220,000 sq. ft. over four plants is announcing new investment in 3D metal printing production equipment and expertise.
Specifically, the company is taking delivery of two M 290 direct metal printing systems from German market leader EOS (with North American offices in Novi, MI) this month along with newly hired additive manufacturing director Mike Misener, who already sees growth for the company in this technology.
"3D metal printing is redefining part processing and production efficiencies in a number of industries were already serving, like aerospace, aircraft, defense, automotive, medical, power generation, and mold tooling," he says. "The impact for our customers will be positive and immediate, and more will follow."
A Technology Bridge
"Weve always considered ourselves leaders in bringing technology to our customers," says company founder Kevin Baker, who along with his brother Scott founded Baker Machining. With a foundation in manual metalworking, the company was one of the first in its area to embrace 5-axis CNC , simultaneous multi-axis milling , and 3D surface processing throughout its existence. "Our customers have always expected us to be at the tip of new technology," he adds.
"There have always been chips on the floor here," adds Scott Baker. "Through the blending of these technologies weve proven through our FDM (fused-deposition modeling) and 5-axis milling technologies that it takes both additive and subtractive manufacturing to make customers successful. In FDM, we bought our first machine and quickly added to it for a total of five plastic printers, with more to be added in 2016. We forecast similar results going forward for our metal printing."
Both company founders confirm that they had been investigating 3D metal printing for the last few years and decided the technology has progressed enough to where it has the most value for Baker customers. Specializing in complex, CNC-machined parts, 3D metal printing holds promise for unconstrained new thinking for design improvements and parts that cannot be made any other way.
Conformal cooling inserts for injection molds are one example. "3D-printed metal inserts allow cooling lines to closely conform to part dimensions," Misener says. "By eliminating hot spots, cooling cycles are cut dramatically. Molds run faster, last longer, and produce more quality parts. Thats only one example where 3D metal printing is changing the business."
With an operating philosophy of continued technology investment backed by a 20-plus year track record of growth, the company expects many innovations to follow from its Baker 3D Solutions Division for its customers.
Featured Product
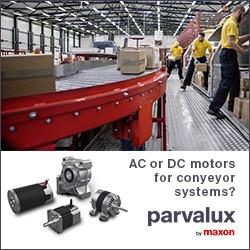
Parvalux by maxon - AC or DC electric motors for conveyor systems?
The material handling industry uses conveyors to ensure that products are distributed effectively, AC or DC motors are chosen depending on the weight it needs to carry and the speed at which it needs to work. Learn which type of conveyor motor might be best for your application and how Parvalux can help you select a geared motor from stock or create a fully custom design.