PMAT transforms your assembly tools
Flexible vacuum tooling system excels in automotive body-in-white (BIW) assembly
Hingham, MA - Piabs Modular Automation Tooling, known in short as PMAT, is now available globally. The tooling system has been used mainly for years in North America by leading automotive manufacturers, where it has helped to quickly construct flexible and adjustable vacuum gripper/fixture tooling.
"Experiences from the North American market show that PMAT is particularly advantageous when used for body-in-white (BIW) assembly, mostly in decentralized applications for greater up time, more reliability and ease in troubleshooting, but it can of course also be very useful when applied to general assembly stages," says Josef Karbassi, Vice President of Piabs Automation Division.
Manufacturers can use PMAT to design robot end-effector tools, ergonomic tools or fixture tools for any type of automation equipment. PMAT offers both adjustability and rigidity, and will help producers to transform their assembly tools to meet their specific needs with minimal design time.
The tooling system features connecting parts for welded frames or extruded profiles and swivel arm assemblies with single bolt adjustment for ease of set up with a choice of attachments. Some of these include ejectors based on Piabs energy-efficient COAX technology. The ejector units provide vacuum as well as a release function.
For extra safety, the attachments may also be equipped with a Vacuum Check Valve in case there is an interruption of supply air and the energy saving unit Vacustat that saves up to 98% of air usage. The Vacuum Check Valve addresses both safety concerns and energy savings by securely holding parts in case of power loss or loss of compressed air. . Also available are suction cup attachments that make it easier to correctly position suction cups on objects, especially when these are of varying geometries, as in the case of automotive parts.
The PMAT tooling system is made of high rated aircraft grade anodized aluminum and is machined, not cast, for a quality assembly and fit.. It is lightweight and easy to assemble on site without welding or use of special tools. A proven and reliable technology, PMAT is supported locally on a global basis.
About Piab
Established in 1951, Piab designs innovative vacuum solutions that improve the energy-efficiency, productivity, and working environments of vacuum users around the world. As a reliable partner to many of the worlds largest manufacturers, Piab develops and manufactures a complete line of vacuum pumps, vacuum accessories, vacuum conveyors and suction cups for a variety of automated material handling and factory automation processes. Piab utilizes COAX, a completely new dimension in vacuum technology, in many of its original products and solutions. COAX cartridges are smaller, more energy efficient and more reliable than conventional ejectors, and can be integrated directly into machinery. This allows for the design of a flexible, modular vacuum system. Piab is a worldwide organization with subsidiaries and distributors in almost 70 countries. Its headquarters are in Sweden. For more information about Piab vacuum solutions for a diverse range of applications, visit www.piab.com.
Featured Product
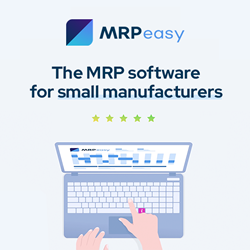
MRPeasy - ERP for Small Manufacturers That Delivers Results
Always know what you have in stock and what you'll need to fulfill orders. Never forget to order parts on time or fail to notice a late delivery from your vendor. Easily create manufacturing orders and schedule them automatically according to resource availability or delivery deadline. Generate accurate cost and lead time estimates and provide customers with quick quotes. Receive notifications when orders are late or inventory levels reach a critical point. Ensure seamless communication between sales, production, warehousing, procurement, administration, and finance. Integrate with popular accounting, CRM, and e-commerce apps. MRPeasy is an ERP software for small manufacturers that gives you all that and more. Our users report a 54% average improvement in the overall performance of their business and a 42% increase in on-time deliveries. Try for free, no credit card needed.