FABTECH - Praxair to Unveil New Robotic Cutting System at FABTECH 2015
FABTECH show in Chicago, November 9-12
DANBURY, Conn.--Praxair, Inc. (NYSE:PX) announced today that it will debut a first-of-its-kind Robotic Cutting System, the Praxair ProStar PRS900, at the FABTECH show in Chicago, November 9-12.
Praxair (Booth N14049) will demonstrate how this breakthrough metal-cutting technology can help customers lower equipment investment, cut labor expenses and minimize operating costs, all while improving product quality and productivity.
"Put simply, Praxairs new PRS900 system provides fabricators with the ability to do much more with much less," said Craig Camp, Praxair cutting machine manager. "The systems modular design allows operators to use one machine to cut structural tube and beam as well as 2-D plate and domes. Additionally, its true complex 3-D movement and ability to create, share and acquire evolving cutting parameters online, using the proprietary PRS900 cutting systems web-based operator interface, provide users with new flexibility."
Praxair will also be supporting FABTECH exhibitors by providing the shows nitrogen supply. Through the use of skidded, portable microbulk cylinders and its microbulk supply capabilities, Praxair will ensure all exhibitors have access to nitrogen at the pressures they need.
About Praxair
Praxair, Inc., a Fortune 250 company with 2014 sales of $12.3 billion, is the largest industrial gases company in North and South America and one of the largest worldwide. The company produces, sells and distributes atmospheric, process and specialty gases, and high-performance surface coatings. Praxair products, services and technologies are making our planet more productive by bringing efficiency and environmental benefits to a wide variety of industries, including aerospace, chemicals, food and beverage, electronics, energy, healthcare, manufacturing, primary metals and many others. More information about Praxair, Inc. is available at www.praxair.com.
Featured Product
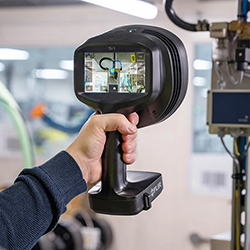
Affordable Excellence: The Go-To Tool for Finding Compressed Air Leaks
Find compressed air leaks fast with FLIR's new cutting-edge Si1-LD acoustic imaging camera. Leveraging advanced ultrasonic technology and onboard analytics, this affordable camera pinpoints leaks and quantifies incurred losses even in the nosiest environments. Upgrade your maintenance routine with the cost-effective FLIR Si1-LD - significantly reduce energy costs and increase system uptime. Get Started Today.