AUVSI 2015: Horizon Unveils the World's First Hydrogen Powered, 4H-Endurance Multi-Rotor UAV
HYCOPTER will be on display starting today at booth 401 at the May 4-7 AUVSI trade show in Atlanta.
ATLANTA--Singaporean company Horizon Unmanned Systems (HUS) unveils HYCOPTER, the worlds first hydrogen fuel cell powered multi-rotor UAV. HYCOPTER is being readied for a record flight endurance of 4 hours, or around 8 to 10 times the average flight duration of equivalent systems today.
Unlike any other rotorcraft, HYCOPTER makes use of its frame structure to store energy in the form of hydrogen instead of air, eliminating energy storage weight. With less lift power required, HYCOPTERs ultra-light fuel cell turns the hydrogen in its frame into electricity to power its rotors.
With HUS breakthrough technology, todays 20-30 minute multi-rotor missions shift to a new paradigm with flights lasting several hours at a time. Aerial survey jobs will become materially cheaper/faster and drone delivery over longer distances, more feasible.
HYCOPTERs special fuel cell was designed by sister company Horizon Energy Systems (HES), which recently announced a new 700Wh/kg solid hydrogen storage system. Newly formed Horizon Unmanned Systems brings together years of knowledge in energy storage optimization, composites, as well as a new breed of autonomous navigation technologies, to show the way forward on innovation in mini-electric UAVs.
"By removing the design silos that typically separate the energy storage component from UAV frame development - we opened up a whole new category in the drone market, in-between battery and combustion engine systems," said CEO Taras Wankewycz. "HYCOPTER is the first result of our efforts and we intend to demonstrate many more platform innovations in the coming months."
HYCOPTER will be on display starting today at booth 401 at the May 4-7 AUVSI trade show in Atlanta.
About Horizon Unmanned Systems www.hus.sg
Featured Product
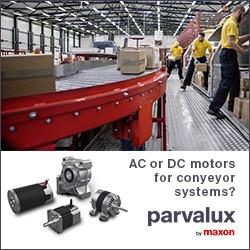
Strain Wave Gearheads by maxon - Highly precise, compact, and efficient.
Strain wave gearheads are ideal for use in applications requiring precision motion control and high torque transmission in a compact design. maxon strain wave gearheads are a specialized type of gearhead where precision and compact design are crucial. This type of gearhead is often used in applications in a confined space. With their advanced gear tooth design, maxon's strain wave gearheads provide high efficiency and good back drivability. Typical applications include:
Robotics, Aerospace, Medical technology and Optical systems
.