Interplay Learning highlights the importance of employee training during volatile times with new white paper, “The Downtime Dilemma”
In "The Downtime Dilemma," Interplay Learning consolidates third-party analysis underscoring the various factors that can contribute to manufacturing downtime, from equipment failure to operator errors.
Austin, Texas — May 13, 2025 — Interplay Learning, the leader in immersive learning for the skilled trades, presents "The Downtime Dilemma," a white paper exploring unplanned downtime in the manufacturing sector and the role of effective technical training in mitigating unwanted interruptions.
In "The Downtime Dilemma," Interplay Learning consolidates third-party analysis underscoring the various factors that can contribute to manufacturing downtime, from equipment failure to operator errors. The cost of lost productivity can be astronomical, surpassing $25,000 an hour even for small-scale manufacturers. That's to say nothing of reputational damage, a serious concern for manufacturers who face disruptions on a regular basis.
"Unplanned downtime has always posed a threat to manufacturing companies, especially when it becomes a pattern or a routine issue," said Doug Donovan, CEO at Interplay Learning. "Our white paper summarizes some of the factors that can exacerbate the risk of downtime, while also suggesting some important safeguards, including an intentional and thorough investment in training."
According to the data documented in "The Downtime Dilemma," human error is one of the leading causes of equipment outages, with common examples including improper maintenance, delayed response times and inconsistent procedures.
Meanwhile, Interplay Learning's paper demonstrates that the right training can equip technicians to mediate these issues and avert unplanned downtime. An immersive training program can empower technicians to proactively identify issues, troubleshoot more efficiently, and handle equipment with the requisite care—all contributing to a manufacturing environment in which equipment lasts longer and functions more reliably.
"We live in an era of uncertainty due to economic, political, and even technological factors," said Donovan. "For manufacturers, it's crucial to mitigate this uncertainty and to control those things that can be controlled, such as employee training and development, an essential bulwark against recurring downtime."
For more information about Interplay Learning, visit www.interplaylearning.com.
Featured Product
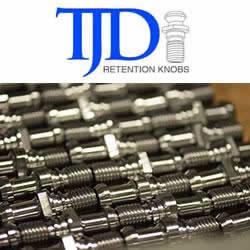
T.J. Davies' Retention Knobs
Our retention knobs are manufactured above international standards or to machine builder specifications. Retention knobs are manufactured utilizing AMS-6274/AISI-8620 alloy steel drawn in the United States. Threads are single-pointed on our lathes while manufacturing all other retention knob features to ensure high concentricity. Our process ensures that our threads are balanced (lead in/lead out at 180 degrees.) Each retention knob is carburized (hardened) to 58-62HRC, and case depth is .020-.030. Core hardness 40HRC. Each retention knob is coated utilizing a hot black oxide coating to military specifications. Our retention knobs are 100% covered in black oxide to prevent rust. All retention knob surfaces (not just mating surfaces) have a precision finish of 32 RMA micro or better: ISO grade 6N. Each retention knob is magnetic particle tested and tested at 2.5 times the pulling force of the drawbar. Certifications are maintained for each step in the manufacturing process for traceability.