Compacting aBrazing stand out as key joining methods for the module connectors in the production of electric vehicles
Ever wondered how electric vehicles (EVs) come together? Well, there's an interesting world of joining and welding processes behind the scenes. Let's stroll through the basics of EV manufacturing, focusing on the pack level.
Levels of Joining
Module-to-Module Connections
Modules need to connect, and most of the time, it involves copper busbars or a mix of busbars and cables. The go-to technology for this is either resistance welding or resistance brazing - these methods bring the parts together like a high-tech puzzle.
Compacting
When cables are in the mix, we've got to consolidate their ends before the big join. This process, called compacting, uses special ceramic jaws to hold the wires tight. It takes a bit of time (usually more than 500 milliseconds), and we rely on resistant electrodes (materials such as tungsten or molybdenum alloys) to create the heat. Keeping the compacted wire stable involves a clever process control, that include electrode displacement and part thickness feedback loop.
Copper Busbars Joining
For copper busbars, resistance brazing is the right choice. Brazing enables joining of copper and copper alloy parts with high conductivity and big contact areas. The typical brazing material ingredient, between the parts to be brazed is a low-melting copper-based tape, with a bit of phosphorus.
Easy Control
Brazing isn't just efficient; it's also easy on the eyes. Visual quality control is the confirmation that the brazing material has melted just right. To make sure the visual check can be accompanied by tensile strength and electrical resistance values.
Challenges and Clever Solutions
Challenges include braiding without harming insulation and dealing with an enormous diversity of product types. The industrial solution includes an effective cooling system and a modular approach to successfully deal with these challenges.
This was our sneak peek into the world of joining and welding in electric vehicle manufacturing. From compacting wires to brazing busbars, it is all about technology working together.
AMADA WELD TECH will be happy to discuss your welding challenges in manufacturing EVs.
About AMADA WELD TECH
AMADA WELD TECH is a leading manufacturer of equipment and systems for Laser Welding, Laser Marking, Laser Cutting, Resistance Welding, Hermetic Sealing and Hot Bar Reflow Soldering & Bonding. We design and manufacture industry-leading product families for the global market and customize our products around specific micro-joining applications. AMADA WELD TECH product markets include medical devices, battery, automotive, solar industry, electronic components and aerospace. AMADA WELD TECH Europe is headquartered in Germany and has additional production facilities in The Netherlands and UK, as well as sales offices in France, Hungary and Italy and part of the worldwide AMADA Group, with over 8.500 employees worldwide. More on products and services: https://www.amadaweldtech.eu/
About Cyberjoin
Cyberjoin serves as a transformation hub, which helps companies in the automotive and supplier industries on their path to electromobility. The hub promotes the collaboration and knowledge exchange of joining, materials and manufacturing technologies. It was initiated in 2023 by the German Federal Ministry for Economic Affairs and Climate Protection. https://cyberjoin.de/
Featured Product
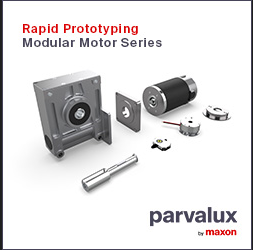
Rapid Prototyping with the Modular Motor Series
Quick to configure. Quick to build. Quick to deliver. Parvalux understands the importance of getting product in the hands of customers quickly and efficiently. The Modular Range does just that allowing customers to configure their own solution, selecting motor and gearbox, adding encoders and brakes to create a solution perfectly suited for their specific applications such as conveyor belt systems, picking systems, parcel sorting equipment, pallet shuttles and automated storage and retrieval systems (ASRS). Read our modular range guide for specifics.