RAM™TECHNOLOGY EMPLOYS REVOLUTIONARY REVERSE AIRFLOW DESIGN
KENT, OHIO - Bison®, a leader in innovative motor technology, proudly announces the issuance of a patent for the revolutionary RAM™ Reverse Air Movement Blower Motor. This cutting-edge invention, spearheaded by esteemed Senior Director of Technology, David Finkenbinder, overcomes the performance shortcomings of traditional thru-flow air blower motors through its novel design.
RAM™ technology is poised to transform various air moving applications, catering to industries that prioritize lower operating temperatures, enabling achievement of reduced noise, and extended motor life. This innovative technology can benefit applications from industrial fume evacuation, floorcare for commercial and residential use, paint sprayers, aerospace air movement, surgical smoke evacuation, and hand dryers.
Unlike traditional thru-flow motors that face overheating challenges, RAM™ technology employs a unique reverse airflow design. The motor side is only exposed to ambient air intake, ensuring optimal cooling even in near-sealed conditions. This innovation eliminates the need for costly thermal protection or energy-inefficient bleed holes, enhancing reliability, sound performance, and overall motor life.
Motors with RAM™ technology operate at significantly cooler temperatures, enhancing brush life, commutator performance, and overall reliability. The technology achieves a remarkable 6.5% reduction in decibel levels and a significant 48% reduction in Sones compared to traditional thru-flow motors. RAM™ technology also completely removes the necessity for a leak path at low flow conditions, leading to increased product performance and reduced noise.
Another key benefit of RAM™ technology is its versatility. The motors support straight air exit, peripheral, and reverse airflow, providing versatile solutions for various applications. The technology can also significantly reduce carbon dust emissions by applying V0 rated foam to surround the motor, which improves product performance and also helps minimize noise. The product is available in a range of custom design options, providing lightweight applications, shorter heights, and larger diameters to meet specific end-use requirements.
Bison is excited to offer the patented RAM™ Blower Motor Technology. Whether for fume evacuation, residential and commercial vacuums, paint sprayers or other end uses, RAM™ technology is designed to elevate device performance by reducing operating temperatures and noise while extending motor lifespan.
To learn more about Bison's products, visit BisonAMETEK.com.
ABOUT Bison®
For more than 100 years, Bison®, an AMETEK business, has helped customers differentiate their products by developing robust, flexible and durable motors, blowers, and pumps under the brand names - Bison® Gear Motors, Lamb® Vacuum Motors, Nautilair® Combustion Blowers, Prestolite Motors Brushed DC Motors, ROTRON® Regenerative Blowers, ROTRON® Transportation and Windjammer® Brushless Blowers.
Bison® engineers thrive on technical challenges and provide customers with collaborative, customizable and optimized fluid-moving, fractional and integral horsepower solutions.
Bison® has worldwide sales representative support, research facilities and manufacturing facilities in the United States, China, and Mexico. The company is headquartered in Kent, Ohio.
Bison® is a business of AMETEK - a leading global provider of industrial technology solutions serving a diverse set of attractive niche markets with annual sales over $7.0 billion.
Contact:
Christina Thomas
Marketing Manager
Bison®
(330) 677-3830
(440) 263 -3733 Mobile
Christina.M.Thomas@ametek.com
Featured Product
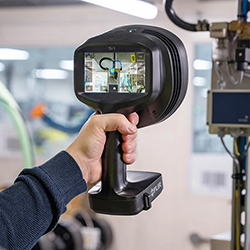