MICROMETAL’S USE OF GLASS PHOTO TOOLING CONTRIBUTES TO UNIQUE LEVELS OF PRECISION IN METAL PART FABRICATION
The use of glass photo tooling is a pioneering approach that surpasses the capabilities of conventional digital photo tooling employed by other PCE service providers.
(February 27th 2024, Muellheim, Germany) micrometal has released details of a critical aspect of its next generation photo chemical etching (PCE ) process. Glass photo tooing makes micrometal's process uniquely precise and contributes to the company's ability to provide precision, geometrically complex metal parts, in volume, with levels of accuracy and repeatability that no other metal fabrication process can match. Our glass tooling, a significant advantage in Photo Chemical Etching (PCE) technology, combined with our advanced process controls sets a new industry standard for precision and repeatability. The use of glass photo tooling is a pioneering approach that surpasses the capabilities of conventional digital photo tooling employed by other PCE service providers.
In an industry where precision is paramount, micrometal's glass photo tooling technology delivers unmatched tolerances in the range of 1-2 microns. Our tooling is printed at 100k dpi, nearly 10x the resolution of conventional film-based photomasks. This level of detail is crucial for applications requiring microscopic accuracy, and micrometal's process ensures that these demanding standards are consistently met. Glass tools, compared to conventional film tools, last a lifetime and are impervious to fading, temperature, humidity and other environmental factors. This means that every part is identical, every time, for the life of the project.
Karl Martinson, Sales Director, North America at micrometal says, "micrometal's use of glass photo tooling contributes to our ability to maintain supreme accuracy over extensive etching areas. For instance, over a 700 mm etch span, micrometal's next generation PCE process can achieve a remarkable 5-10 micron tolerance. In contrast, PCE companies relying on traditional film-based tooling struggle to claim tolerances within the 50-60 micron range. This stark difference not only showcases the superiority of glass photo tooling but also underscores micrometal's commitment to pushing the boundaries of what's possible in the area of PCE."
micrometal's use of glass photo tooling, integrated with our one-of-a-kind automated etch line, allows for an unparalleled level of detail in manufacturing of complex, high-precision components that were previously unattainable. As a result, micrometal is not just meeting the existing needs of the market but is also paving the way for new applications and innovations across various industry sectors.
micrometal stands at the peak of precision etching, providing its clients with the confidence that every product manufactured is not only of the highest precision but also produced with the most advanced and reliable technology available. Through the use of glass photo tooling, the company has maintained its position as the global leader in photo-chemical etching.
www.micrometal.de
Featured Product
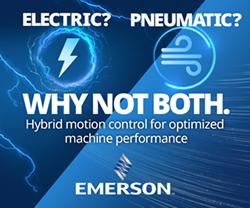