Is Your MRP Going to Cause a Southwest-Style Meltdown?
By Harrison Wells, Director of Value Engineering, LeanDNA
The catastrophic disruptions Southwest Airlines suffered this holiday season revealed that the ‘if it ain't broke, don't fix it' mindset is still alive and well in even some of the most successful companies. Now that the deficiencies in their systems have been laid bare and are facing external scrutiny, it is safe to assume both mindsets and key positions at Southwest will be changing quickly.
Southwest relies on an off-the-shelf crew assignment software called SkySolver which it has customized and updated over the years. The program was developed almost 20 years ago and was identified as outdated by their users 10 years ago. The convergence of widespread extreme weather during the peak of the Christmas holiday travel season was the tipping point that overwhelmed the system's capacity. Since the system could not be reset overnight to reassess the current state of operations, the company was forced to resort to manual processes that were even less capable than the aging software. While both the recovery costs and damages to the company's reputation are still being calculated, there is little doubt this disruption will rank amongst the most costly to date.
After witnessing outdated software taking a huge bite out of a company's profits and reputation, you might be curious if your company has any similar exposure. If you're involved in manufacturing, you likely rely on Material Requirements Planning (MRP) software to ensure the correct components are ordered to support the completion of your customer's orders. MRP is a key element in most Enterprise Resources Planning (ERP) software suites provided by well known heavyweights like Oracle, SAP, Infor, and Microsoft. After a period of growth and expanded offerings in the 1980s and 1990s, the pace of consolidation in the enterprise software arena stepped into high gear in the early 2000s. Customers relying on MRP software developed by a company that was acquired often saw updates stagnate as they were directed to the parent company's flagship products with dizzying price tags. This environment led to decisions to bootstrap existing MRPs well past their due date.
Given the limitations in early MRP systems, custom configurations and development were often needed to meet relatively basic business requirements. Most larger companies became adept at adding features to the MRP with in-house resources or outside contractors. Given this historical precedent, many companies postponed updates and continued incremental MRP enhancements even though software development was far from their core competencies. The complexity and risk associated with updating the MRP grew exponentially as more critical systems and reports relied on extracts from the legacy MRP software. Without guarantees that significant changes would not jeopardize operations, incremental patches and workarounds became the ‘safe' decision even as support for the original software expired long ago.
The end results of years of updates by various development teams is typically an unholy mess of poorly documented code on perpetual life support that few understand and even fewer dare to touch. Worse yet, the tribal knowledge necessary to sustain this zombie MRP becomes more tenuous every year. Although the cost to maintain the obsolete software increases every year, the majority is quick to point out that these costs are trivial relative to implementing a new MRP system. Since few can accurately assess when the risk of inaction overtakes the risk of change, this collective denial often continues even after obvious single points of failure in the hardware, software, and staffing are exposed. Companies must move quickly once these risks are exposed since time is limited. Southwest apparently decided to kick the can down the road and is paying a steep price for its decisions to postpone prudent updates.
Given that MRP updates are inherently risky, expensive and time-consuming, companies are looking to modern SaaS solutions to replace their homegrown patchwork of legacy MRP enhancements and reports. As more employees work in multiple industries, the mindset that there is something inherently different and unique about a particular company is starting to fade. Companies are recognizing that pursuing mass software customization to replicate current systems will send them down the same dead end path saddled with their existing limitations and antiquated workflows. Migrating to SaaS solutions brings added functionality, capabilities, and stability that effectively breathe new life into their existing MRPs without the risk of disrupting operations.
People often use the analogy that upgrading an MRP is like trying to replace a tire on a moving bus. MRP systems, like the bus, need to run routinely to support factory operations, making maintenance both challenging and risky. SaaS solutions allow organizations to replace outdated patches without having to ‘stop the bus'. Simply providing SaaS solutions access to existing MRP data tables allows the software to augment features, upgrade reporting, and provide insights without impacting a single refresh. The situation at Southwest is a painful reminder that ignoring warnings and hoping something doesn't break isn't a strategy.
Featured Product
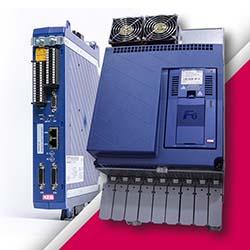
KEB VFDs for High Speed Motor Control
KEB's VFDs are the key to unlocking peak performance in your high-speed machinery. Engineered for precision control, even without feedback sensors, our F6 and S6 drives utilize advanced software and high-frequency output. This ensures smooth operation, reduced vibration, and optimal efficiency. Whether you're building turbo blowers, power generation systems, or other high-speed applications, KEB VFDs deliver the reliability and performance you need.