Allied Machine Releases T-A Pro Drill High-Speed Steel Geometry
Allied Machine and Engineering proudly announces the newest expansion of the T-A Pro high penetration drilling system—the high-speed steel geometry insert, also referred to as the "X" geometry. This super cobalt insert works as a drill-everything insert while significantly lowering the risk for high-dollar value components.
Allied Machine and Engineering, a leading manufacturer of holemaking and finishing cutting tools for the metal-cutting industry, proudly announces the newest expansion of the T-A Pro high penetration drilling system—the high-speed steel geometry insert, also referred to as the "X" geometry. This super cobalt insert works as a drill-everything insert while significantly lowering the risk for high-dollar value components. When functioning in less than ideal conditions, the high-speed steel geometry provides superior performance and chip formation in addition to process security when needed most.
As the most recent addition to the T-A Pro high-penetration drilling system, this insert demonstrates that the best just keeps getting better. Not only are the faster penetration rates maintained, but in using the redesigned body of the T-A Pro, maximum coolant flow and excellent rigidity are also present when utilizing the high-speed steel geometry. This offers machine shops and manufacturers a spade drill that operates at incredible speeds and a cost per hole that averages 25% less than other existing drills.
With a tool life that rivals carbide, the high-speed steel geometry insert works well in almost every material class. Allied Machine's team of engineers developed this insert as the simplest solution for selecting a drill insert when hole quality, tool life and process security are the primary needs of the application. Ultimately, even in the toughest cutting conditions, this insert provides excellent hole quality for use in job shops and large part manufacturers such as heavy equipment and aerospace.
T-A Pro's high-speed steel geometry insert series Z-3 is now available in diameters ranging from 0.437"-1.882" (11.10mm - 47.80mm).
Featured Product
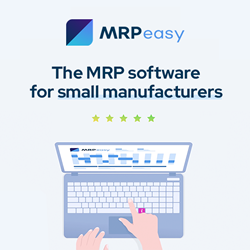