Need for PPE Launches New Non-Profit Manufacturing Firm
“I was disturbed by news of the PPE shortage in the face of this virus and delved into dedicated research on the topic, thinking that Human Solutions Tech’s first product could be dedicated to this mission,” said Dobbs.
[Waterbury, CT - April 29, 2020] Design engineer Glen Dobbs has talent, curiosity, resourcefulness, and perhaps the most important attribute of all - a big heart. Dobbs is the President and CEO of LoganTech, a manufacturer of several lines of communications devices for nonverbal and visually impaired individuals. In his spare time, he's been crystalizing the idea of establishing a separate, non-profit entity, called Human Solutions Tech LLC, to broaden the scope of the work to include other devices to fill unmet, specific needs. Two months ago, he thought the COVID-19 crisis would halt the work he'd been putting into the new organization, but it didn't. It accelerated it.
"I was disturbed by news of the PPE shortage in the face of this virus and delved into dedicated research on the topic, thinking that Human Solutions Tech's first product could be dedicated to this mission," said Dobbs.
To that end, Dobbs and his staff networked with local medical facilities to better understand the shortage and learned that the face shields seemed to be most in need. The plastic shields act as the first line of defense for the N95 respirators and masks. With many large volume manufacturers already producing these, Dobbs wanted to make sure his company could really be of service in that endeavor. As it turned out, the backlog in the larger manufacturing and healthcare supply chains was rather long and cumbersome. As a low volume manufacturer by design, Dobbs felt his team could ramp up and at least provide local organizations face shields in the interim, before the larger orders the institutions had placed would be delivered. They could also supply the smaller, independent practices that simply didn't have the buying clout to get in line with the larger purchasing networks. Practically overnight, Dobbs and his staff secured the equipment they needed in house such as rapid prototyping and 3D printing equipment, laser cutters, vacuum forming machinery, CNC metalcutting machines and software. Within the last month, Human Tech Solutions has made and delivered hundreds of shields to various healthcare sites, primarily in Connecticut, at no cost.
"Once this urgent push for face shields subsides, we will apply for non-profit status," said Dobbs. We also want to be generous with the rewards that doing good offers. We envision this concept at Human Solutions Tech as something inclusive so that other manufacturers in the region can join us in any number of ways - perhaps dedicate their extra design and production time, donate equipment and software, provide training on how to get the most out of the machinery, and other resources. Many responsible companies love to get involved in supporting worthwhile endeavors and have team-building experiences with their employees. Human Solutions Tech could be one of those causes that embrace their manufacturing talents as well."
While the company wants to be agile, Dobbs and his team have already discussed some possible product areas they could pursue such as mobility devices, prosthetics, human/machine interfaces, and the like.
"The main goal is to identify a need as it arises, that isn't currently being met," said Dobbs. "Then, we quickly evaluate the need, determine if we are in a position to help out, and if so - find a way to make it. That's exactly how it all happened with the PPE just a handful of weeks ago."
For more information, contact Human Solutions Tech at 866-962-0966, or fill out the contact form at www.humansolutionstech.com. For more information about LoganTech, visit www.logantech.com.
Featured Product
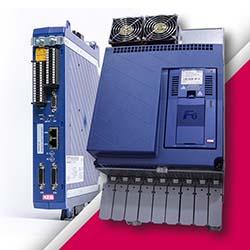