There are a number of manufacturing issues that come up when projection welding fasteners onto hot stamped boron steel components. In most cases, the weld nuts and studs used are considerably softer than the 1500 MPa stamping.
Projection Welding of Fasteners to Hot Boron Stamped Components
Bob Kollins | Amada Miyachi America
Projection welding of fasteners to hot boron stamped components
Automotive component assemblies often incorporate projection welding of fasteners. And more and more manufacturers are using hot stamped boron steel, like Usibor®, resulting in lighter weight components with increased tensile strength (up to 1500 megapascals (MPa). This helps them meet regulatory requirements while maintaining 5-star safety ratings.
There are a number of manufacturing issues that come up when projection welding fasteners onto hot stamped boron steel components. In most cases, the weld nuts and studs used are considerably softer than the 1500 MPa stamping. This large change in hardness can cause the weld projections on the fastener to collapse prior to a successful fusion of the parts. This results in vaporized projections, leading to extended weld times in an effort to forge the materials. The result is weak inconsistent torque and push out values as well as deformed fastener threads.
Also of concern is the consistency of the base material due to in-house processing. Oven temperatures, heat cycle times, water flow rates, water temperatures, and quench times all lead to material variations. This leads to inconsistent interface resistance and in turn leads to inconsistent heat generation.
Comparing processes to achieve success
Researchers have compared mid-frequency direct current (MFDC) processes with capacitor discharge (CD) weld controls to arrive at the best process for the application – and the one that can meet the manufacturing challenges identified.
Typical weld times with MFDC processes are in the range of 6-10 cycles (100 milliseconds (ms)/160ms). These longer weld times make it almost impossible to utilize the high contact resistance present in the hot stamped boron steels. Without being able to capture the heat on the rising edge of the current profile, the weld becomes more of a forging process than a projection welding process. The longer weld times also cause deformation of the nut and damage to any included threads.
CD weld controls can deliver a high peak current in 3ms and total pulse widths on the order of 10-ms. (See Figure 1). These shorter weld times allow concentrated heating at the projection tip with subsequent increases in local deformation. This enhanced localized deformation improves both performance and reliability of the welds.
The process can produce higher than normal pushout and torque values, which meet automotive requirements. It can also extend electrode life. See Figure 2 and Figure 3 for examples.
Making the most of the CD welding process
To get the full benefit of the shorter cycle times associated with CD welding, welder manufactures must properly size the weld cylinders, weld ram, and fast follow-up mechanism to maintain force through the projection collapse. Without this optimization, expulsion is unavoidable.
For each welding application, I would recommend a laboratory study to evaluate the welding parameters using hot stamped parts to determine the optimal fast follow-up system. It is always best to use processed parts and not coupons when evaluating system mechanical response for this part of the process. In addition, the projection welder frame must be able to accommodate the added stresses caused by higher forces and increased rates of acceleration with little or no deflection.
The CD weld process produces a rapid pulse of current that creates instantaneous heating at the weld interface. This is similar to a constant voltage feedback – small changes in current based upon resistance changes, while maintaining appropriate heat generation.
A comprehensive weld monitor is a must-have when using a CD welding process. Once baseline process parameters have been established, high and low windows – or envelope – should be set to ensure the process stays within the limits. Figure 4 shows the most common parameters used in CD welding.
To sum it up
Customer installations and laboratory testing have shown CD welding to produce superior results when projection welding fasteners to hot stamped boron steel. The test results exceed manufacturers’ required push out and torque requirements with no damage to the fasteners threads. Consistent results have virtually eliminated costly post-weld inspections.
In addition, CD welding equipment costs less than the larger MFDC power supplies, with the added additional benefit of lower facilities cost.
But remember, the CD power supply is only the beginning of the process; the complete answer requires high current, high weld force, short weld times, fast follow-up mechanisms, and rigid frame welders. CD systems often use higher forces (compared to MFDC variants) to ensure proper follow-up.
Read the entire white paper Projection Welding of Fasteners to Hot Stamped Boron Steel for more information on this important application.
The content & opinions in this article are the author’s and do not necessarily represent the views of ManufacturingTomorrow
Comments (0)
This post does not have any comments. Be the first to leave a comment below.
Featured Product
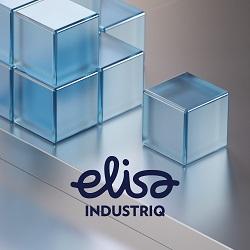