Tübingen-based precision tools manufacturer Paul Horn GmbH is testing the boundaries of additive manufacturing. Behind this venture is a push to gain the competitive edge and offer customers the best possible solutions.
Precision Tools Hot Off the Press at Paul Horn
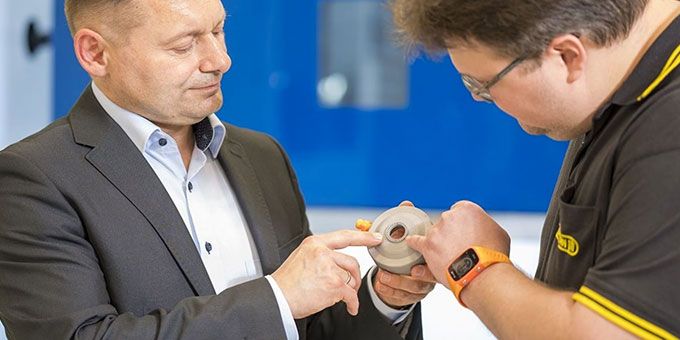
Case Study from | Trumpf
The glossy white floor reflects the gleam of the LED lighting. The CNC machines are lined up like mini rockets ready to blast off. In the inner workings of the machine, carbide metal blanks are transformed into brand new tools, carefully cooled with continuously freshly prepared coolant. Only once the machine has removed the last micrometer of material exactly according to plan do the tools leave the build area.
Every product that leaves the production hall at Horn must meet the standards of a Swiss watch manufacturer, medical technology or the aerospace industry. Founded back in 1969 by Paul Horn, the company has since grown into one of the leading global manufacturers of precision tools for demanding machining. Put simply, only a small number of companies understand how to remove material down to the last µ as well as Horn.
LEARNING THE HARD WAY
It's even more surprising, then, that the strength of one machine at Horn has proven to be precisely its weakness. On the second floor of plant 2 in Tübingen, Horn is refining its additive manufacturing with a 3D printer supplied by TRUMPF. Two 500 watt lasers work around the clock to bring the ideas generated by the developers and engineers to life from fine metal powder in the TRUMPF TruPrint 3000.
"Only those willing to strike out on new paths can enrich their knowledge," stated the recently passed CEO of Horn, Lothar Horn in an interview back in 2019. Matthias Luik, Head of Research and Development at the company since 2010, continued: "Whoever claims the title of technology leader in a certain field must be open to exploring new technologies." It may therefore come as no surprise that exploring the boundaries and possibilities offered by 3D printing by creating a dedicated Additive Manufacturing (AM) department at the Tübingen HQ back in 2018 was the logical next step for the precision tools expert. "We already possessed the required materials knowledge in-house and can analyze the powder used ourselves," explains Matthias Luik. "Everything else we had to learn the hard way." An arduous path for some, but not for Matthias Luik, who celebrates "learning from mistakes" as a key element of the Horn company culture.
Matthias Luik, Head of Research and Development at Horn (left) with the Additive Manufacturing team: Dr. Konrad Bartkowiak, Head of the Additive Manufacturing dept. (center) and Michael Schäfer, Additive Manufacturing Engineer and principal operator of the new TRUMPF system at Horn (right).
NOT UP TO SCRATCH
After three long years of intensive testing and meticulous analyses with powders, process parameters, printing processes and prototyping, the initial machine purchased from another manufacturer was simply no longer up for the job for the Additive Manufacturing team. It was time for a new one to take its place. Half a year later, after structured benchmark testing, including long-term testing, evaluating service quality and communications, Horn finally settled on TRUMPF. "Everything just works," added Dr. Konrad Bartkowiak, Head of the Additive Manufacturing dept. at Horn with a nod to the reliability and consistent quality produced by the system. Minimal downtime and process stability offered by the TruPrint 3000 have positively improved work-life balance for the Additive Manufacturing team: "Ever since we've started working with the TruPrint 3000, I find it far easier to head off for the weekend with a clear mind," explained Michael Schäfer, an Additive Manufacturing Engineer at Horn and the principal operator for the new TRUMPF system. In the past, he was often required to put in extra hours to get the machine running again after error messages or aborted build jobs.
The dozens of channels within the coolant nozzles wouldn't have been possible were it not for 3D printing.
As Matthias Luik (right), Head of Research and Development at Horn, sees it, including additive manufacturing in the company's portfolio with an additively manufactured coolant nozzle is critical for technology leadership.
GO LIVE IN NO TIME
Bartkowiak and Schäfer's "baby" went live in May 2022 and the team has been working with the system in a productive environment since September. In the first seven months, the team completed over 20 internal and external projects, including custom jobs for customers, prototypes for the tool catalog and components for the production system, to get the most out of their machines. One project involved creating a coolant nozzle for a machine on which employees perform internal cylindrical grinding to produce tools. Dozens of channels on the inside of the coolant nozzle facilitate cooling for the mounted point and tool with pinpoint accuracy. This increases the life span of the mounted point and the quality of the machined tool. "It wouldn't have been possible to create this component using conventional manufacturing methods due to the extremely delicate structures found within," explains Matthias Luik.
TESTING THE LIMITS
Moving forward, Horn plans to further boost the machine's utilization. A prototype for a turning tool previously manufactured using conventional methods is currently in testing and could soon make the leap into the pages of Horn's product catalog. Then there are no other barriers to series production. "In the Additive Manufacturing department, series production isn't our main focus right now," explains Head of Development Luik. "Our main priority lies in testing the limits of technological advancement offered by additive manufacturing with the TRUMPF system. Ultimately, this has the power to give Horn the competitive edge and provide our customers with better tools for their business. In terms of prototyping, weight reduction and cooling are the two main advantages we see in 3D printing." Looking forward, the company also plans to delve into hybrid tool manufacturing. The idea is to produce conventionally manufactured tool blanks onto which a tool head with internal cooling channels is 3D printed. Once complete, insert tips made of various cutting materials can then be fitted. Horn also produces 3D-printed components for its customers, taking care of the entire process chain – including full post-processing.
The first additively manufactured turning tool may soon be added to Horn's product range of over 25,000 standard tools.
INVESTING IN THE FUTURE
At Horn, additive manufacturing is here to stay. The company has already successfully attracted junior Additive Manufacturing staff with its initial trainee projects on the TRUMPF system. The company also has all bases covered in case demand for Additive Manufacturing suddenly sky-rockets: Horn has kept plenty of space available next to the TruPrint 3000 for other additive manufacturing systems in plant 2.
The content & opinions in this article are the author’s and do not necessarily represent the views of ManufacturingTomorrow
Comments (0)
This post does not have any comments. Be the first to leave a comment below.
Featured Product
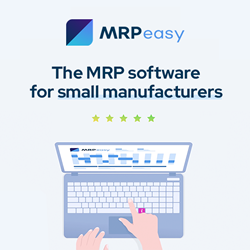