Quality is not something that you can add into your product in the last step of your process. Quality is the outcome of all your processes and efforts.
The Monetary Impact of Quality and Quality Management
Q&A with Gerben de Haan, CPO and Co-founder | AlisQI
Tell us about yourself and what led you to begin AlisQI.
I’m the Co-founder and Chief Product Officer at AlisQI, the no-code Quality Management system for manufacturing. Together with our CTO, we started AlisQI when we were still in university. Back then, we ran into manufacturing companies that were really struggling with their quality management operations. It was all paper or Excel-based. There were commercial solutions, but we were not too impressed with them. That’s when we decided to develop a better solution for quality management in the process and batch industry. One key flaw we saw in all the competitor solutions was that they did not provide an integrated solution that spans the whole of quality management. They either focus on the lab process, or on the quality manual or on the incident and CAPA handling. You cannot do one without the other, so for us there was only one way: develop a QMS that seamlessly integrates these three silos.
How do manufacturers look at the monetary impact of quality and quality management?
Well, to be honest, many manufacturers still consider quality management a regulatory must have and not so much an opportunity to differentiate. In many companies, it is a rather immature business function. Quality leaders often have a hard time proving the value of their team and department in the context of the bottom line - let alone the impact on the top line revenue stream.
What are the benefits of a holistic view on the cost of quality?
I would like to counter this question and ask ‘How can you operate a business with a limited understanding of the impact of quality?’ Quality is not something that you can add into your product in the last step of your process. Quality is the outcome of all your processes and efforts. Every step and every individual contributor in the organization plays a role in this quality operation and thus impacts quality. As a result, you can only think about quality as a whole. There is no such thing as focussing on internal failure or customer complaints, as they are only the visible and tangible results of a lack of prevention and appraisal activities. The desire to change the outcome, should lead to analysing the process as a whole and making deliberate decisions on where to interfere. Only with this approach one can expect significant improvements in the cost of quality.
How could manufacturers improve their understanding of the cost of quality?
It starts with the awareness that the cost of quality can be measures and/or estimated. As in many cases, perfect is the enemy of good. Your numbers do not need to be perfect, as long as they indicate the right trend you are already in a much better position than without that insight.
Is there a role for QMS in the cost of quality?
Absolutely! If you look at the PAF model by Feigenbaum, the quality guru that developed the Total Quality Management approach, you see that the total cost of quality is broken down into prevention, appraisal, and failure costs. A mature QMS is your system of records for all your prevention, appraisal, and failure activities. As a result, a QMS should be able to dashboard your operational Cost of Quality.
How can a good QMS help with the labor shortages issues manufacturers are facing?
If we look at our customer base, almost half of them have open positions in their quality departments. So, there is a huge shortage of skilled personnel. We also see that there is a lot of inefficiency in the market due to a lack of proper tooling. Think about manual data entry, manual validation, manual reporting, manual communication. There is a world to win with proper automation. Please don’t understand me wrong, we are not helping our customers to reduce the head count. We help them to free up time and brain power to do more advanced and intelligent stuff than all these manual data management activities. We empower organizations to do more with the same squad and drive continuous improvement without the need to hire new Quality personnel.
Additionally, another rare species out there is IT personnel within manufacturing companies. They are overloaded as well. Which means that implementing and integrating a QMS in their IT landscape is probably something pretty low on their priority list, looking at all the security threats they face today. So, enabling the quality organization with a solution they can implement and maintain themselves, makes it much easier to move forward. The quality teams are highly motivated as they benefit from the improved quality improvement and reduced time. While the IT team contributes as a SME in the vendor selection process and support from the side line, this is not consuming too much of their resources, neither during the initial implementation nor during day-to-day operations.
What do you see as the biggest hurdles companies face in implementing a QMS?
We see two big hurdles. Leadership support and a lack of resources in the team. As we discussed before, quite some quality leaders struggle to get management support. This is changing for the better. The new generation of leadership and macro-economic developments have improved the understanding of the relevance of quality management for any business. We support quality leaders in getting their message across internally. We developed a ROI workshop to quantify the business case for a QMS or any quality investment. This helps them to translate their vision into concrete and direct savings.
The second hurdle we see is a lack of resources, time, in the quality teams. With the ever-increasing requirements in quality management, quality teams are overloaded. At the same time, it is hard to find new skilled Q personnel. That makes it harder for companies to implement a QMS. We offer a solution to this with an easy to implement software and a battle tested project plan that allows for an implementation project in one month. We standardized our implementation approach to a large extent, allowing us to get to value quickly.
And then, once the first QMS processes are live, customers benefit from the operational efficiency they gain. This freed up time can be invested in continuous improvement programs, further driving direct and indirect savings.
How do you advance the domain?
We are very ambitious when it comes to our mission of transforming manufacturers’ operations with smart quality management software to unlock their full potential. We are not in business to just build a QMS, we want to be a leading player redefining the category. I think our unique integrated quality platform is really challenging this status quo of pretty old and tried QMS solutions. This is highly appreciated by the market, looking at our consistent 50% growth YoY. With clever features like our traceability reports or QMS visualization, you have an immediate helicopter view on your quality operation, which was unheard before we shipped them in the market. These features and many more are what makes us proud and AlisQI unique.
About Gerben de Haan
Gerben de Haan is Co-founder and CPO of AlisQI, the no-code Quality Management platform for manufacturing. AlisQI helps manufacturers to make their quality management smart and integrated. The no-code approach enables key users to deploy their own processes and workflows, allowing them to embed quality management in their day-to-day operations. Gerben led multiple QMS implementation projects across the globe and is now focusing on AlisQI’s international expansion. Gerben holds a MSc in Business Information Technology from Twente University, Netherlands.
About AlisQI
AlisQI is the no-code Quality Management system for manufacturing. We empower manufacturing companies to transform their operations with easy-to-implement, cloud-based software. This data-driven approach to Quality Management allows manufacturers to unlock their factory’s full potential, and become more profitable, smart, and fully integrated.
The content & opinions in this article are the author’s and do not necessarily represent the views of ManufacturingTomorrow
Comments (0)
This post does not have any comments. Be the first to leave a comment below.
Featured Product
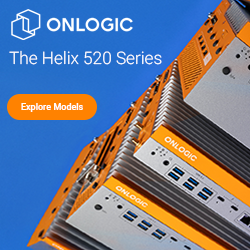