Imagine we have access to a time machine. Engineers could travel three shifts back in time, when production seemed stable. Once there, they could run a simulation to determine which parameter was responsible for causing the performance issue.
Expectations for the Industrial Metaverse - The Next Big Thing is Becoming a Big Thing
Jan Burian | IDC Manufacturing Insights EMEA
Can you imagine a time machine being a real thing? This futurist dream is becoming real — if only in the digital environment.
What if the performance of a production line falls slightly, but operators don’t immediately see a big issue? They check the parameters and try to adjust the process back to a state of stable performance. It seems they are successful, at least initially. Everything appears fine. But then product quality issues begin to crop up in the subsequent steps.
Unfortunately, the engineers were not able to identify the root cause of the problem. The challenges they face include a highly complex production process, inexperienced line and engineering personnel, and incoming raw material that does not meet specifications.
This is a situation that occurs in many manufacturing environments.
But imagine we have access to a time machine. Engineers could travel three shifts back in time, when production seemed stable. Once there, they could run a simulation to determine which parameter was responsible for causing the performance issue. They could run a complex simulation involving asset performance and parameters like temperature, vibration, and pressure. A CO2 parameter could be added to determine to what extent it differed from the planned value.
The engineers are pleased: The simulation succeeds in identifying the root cause. The software is updated, enabling an upgrade of the robot’s program. Production processes are tweaked.
All of this, of course, has occurred in a virtual world — but a virtual world that, like the real-world production environment, is powered by real-time data.
What about the lack of experienced personnel? Our virtual world can be entered at any point in the process. Gaps in employee experience can thus be bridged by calling in an expert to provide guidance remotely. AI-powered tools and extra computing power can be brought to bear to perform engineering and production planning simulations.
How realistic is this concept? First, we can stop using the term “time machine.” The solution already has a name: the industrial metaverse.
IDC defines the industrial metaverse as a highly immersive future environment that blends the physical and digital to enable a shared sense of presence, interaction, and continuity across multiple spheres of operations, supply chain, and business.
Distinct from the social metaverse (which may have little relation to the real world), the industrial metaverse is a physically based virtual platform that fuses data from all software, electronic, and mechanical modalities, including assets, the Internet of Things (IoT), social media, enterprise systems, and business apps.
The industrial metaverse enables users to travel back and forth in time to simulate the virtual and physical worlds — creating a place where innovation can be achieved at the speed of software.
The industrial metaverse is reminiscent of digital twin technology, defined by IDC as “a virtual representation of a physical product, component, asset, or even process.” Digital twins visualize data flows and provide collaboration across engineering, operations, supply chain, and servicing.
But the industrial metaverse goes far beyond digital twins. It can provide users with photorealistic visualizations supported by AI, cloud, and IoT. By enabling the entire life cycle to be accessed in one virtual world, the industrial metaverse indeed offers a kind of time travel.
However, my encounters with people in business and technology have shown me that many still do not recognize the difference between the social metaverse and the industrial metaverse. It is crucial for leaders to understand the essence of the industrial metaverse and to begin thinking about the tremendous opportunities it can bring to the industrial world.
Off to a Great Start
Manufacturing companies that have been early technology adopters are developing immersive digital twins in collaboration with technology partners. In 2022, Siemens and NVIDIA, and Renault Group and Atos, announced partnerships. Manufacturers like Mercedes-Benz, BMW, and Hyundai, and technology giants like Microsoft, AWS, Google Cloud, and Infosys, are also pursuing opportunities in the industrial metaverse.
I am confident that pioneering and adoption of the industrial metaverse will grow — and hard data supports my optimism. In IDC’s 2022 Commercial AR/VR Survey, nearly half of respondents across industries said they found the concept of the industrial metaverse both interesting and applicable to their company. Another 17% found it somewhat interesting and applicable. Just 7% said it was not interesting and applicable.
The survey findings buttress IDC’s prediction that in 2025, 20% of G2000 manufacturers will include the industrial metaverse in their digital road maps to address advanced simulations, cross-domain collaboration, and safety. The timeline for broader industrial metaverse adoption is likely well beyond 2025 — but this is a great start.
Toward a Greener Planet
Recent research I conducted with sustainability expert Gunjan Bassi showed that the industrial metaverse can revamp how “being green” is integrated into an organization’s DNA.
Manufacturing organizations face the challenge of meeting key sustainability goals such as shrinking their carbon footprints in operations and the supply chain, decreasing the energy used for operations, optimizing logistics, and reducing costs related to employee travel. The industrial metaverse can help the realization of these goals by enabling manufacturers to build virtual factories to improve product design and development. It can also strengthen supplier relationship management and social sustainability policies.
I am sure readers can come up with many more potential uses. This is the beauty of modern technology: The opportunities are almost endless.
Hands-On Now — and Eyes on the Future
Hype around the industrial metaverse is becoming ever more concrete, driven by the need of manufacturing organizations to be more efficient, flexible, transparent, sustainable, and profitable.
It is clear that deploying immersive digital twins, for example, can provide the manufacturing world, its ecosystem, and its customers with digital experiences that can transform how people produce, communicate, develop, and collaborate.
And organizations are setting ambitious goals. In November 2022, Renault Group announced that by 2025, it expects the industrial metaverse to have helped it generate savings of €320 million. This includes €260 million worth of inventory, a 60% reduction in vehicle delivery time, a 50% reduction in the carbon footprint of vehicle manufacturing, and a substantial reduction in warranty costs. With these goals, Renault has thrown down the gauntlet — and we can expect the rest of the highly competitive automotive industry to respond.
Once an industrial metaverse platform is created, manufacturers are free to add use cases that cover simulations of layouts, assets, products, and processes, and the interactions of these areas. The platform can also be used for simulations of human behavior, assessments of service suppliers, supply chain and asset management, virtual testing, and more.
To benefit from such deployments, manufacturers need only align the use case with the business case — and have the courage to take a big step into the digital-first environment.
The ability to create communities is another major potential offered by the industrial metaverse (but not, in contrast, by traditional digital twins). Communities can be formed around particular processes (e.g., quality or maintenance management), problem-solving (material and process engineering), research and development (collaborative research), technology (building and training AI models), and training and people development (upskilling and reskilling).
The bottom line: Unlocking the full potential of the industrial metaverse needs more than the deployment of single use cases. Because the future of operations is hyper-connected, single universes of immersive digital twins must converge into one digital, hyper-connected world — the industrial metaverse.
The industrial metaverse is still under construction, but organizations should maintain awareness of its development — and be ready to jump in!
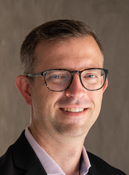
About Jan Burian, Associate Vice President, Head of IDC Manufacturing Insights EMEA.
Jan’s core research coverage includes Industry 4.0, IT/OT convergence strategies, Industrial Metaverse, sustainable manufacturing, and digital transformation across manufacturing subindustries.
(Before joining IDC, Jan worked as a consultant in Big 4 firms for 11 years. He led a Supply Chain and Operations team in the EY Czech Republic and provided consulting services including performance improvement, digital strategy, and enterprise asset management. Before his consulting career, Jan was working in manufacturing companies, holding positions in R&D project management and quality management)
The content & opinions in this article are the author’s and do not necessarily represent the views of ManufacturingTomorrow
Comments (0)
This post does not have any comments. Be the first to leave a comment below.
Featured Product
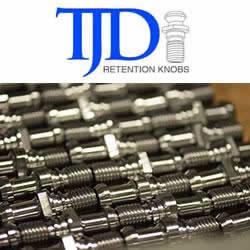