With its flexible multi-product line for rotary encoders, Sensata has developed a sustainable solution. The heart of the precise sensor assembly system: The Smart Function Kit for pressing processes.
Case Study: Plug & Produce in Sensor Production
Tim Voog, Technical Sales | Bosch Rexroth
The complete mechatronic package with preinstalled software reduces the programming to a minimum. Engineering, commissioning and quality assurance become quicker, easier and more cost-effective.
The production of various sensor types in small batches on a single line, the autonomous configuration of production modules, the automatic commissioning and recording of process data: the international manufacturer Sensata was focusing on these futuristic requirements and looking for a set-up for a flexible multi-product line for rotary encoders.
Production of different types of rotary encoders at Sensata: the Smart Function Kit for Pressing reduces engineering, commissioning and quality assurance costs. (Copyright: Sensata)
Easy commissioning, flexible manufacturing
The rotary encoders are used in self-propelled transport shuttles to determine position and distance. On this newly planned line, the circuit board and the disc for the sensor unit are placed in the housing and then fixed with a lid. The mechatronic solution for the critical, product dependent pressing process needed to be not only precise and reliable but also cost-efficient.
“We’re always trying to make our processes simpler and to do as much as we can ourselves – ideally with standard components and without programming effort,” said Jean- Marc Hubsch, Engineering Manager in Sensata’s Industrial Encoders division. According to Hubsch, the idea of a production line which can cost-effectively produce 1,000 or 10,000 versions of a sensor system in small batches is new, but future oriented. Preconfigured modules, which his team merely needs to put together and parametrize for commissioning, are key.
A versatile subsystem which can easily be integrated: the Smart Function Kit with an electromechanical cylinder, a force sensor, a motor, a regulator, a control system and a software package. (Copyright: Bosch Rexroth)
Smart Function Kit for pressing processes
The construction engineer saw the appropriate solution at the Hannover trade fair in 2019: The Smart Function Kit from Bosch Rexroth – a mechatronic package including mechanical, electrical and software, for standardized pressing and joining applications within the force range from 2 to 30 kN.
“This easy-to-use kit is not only interesting for system integrators, but it also benefits end customers like Sensata, who have their own process know-how,” Rexroth Project Manager Laurent Steinmetz explained. The Smart Function Kit for pressing and joining applications combines proven standard components like an electromechanical cylinder (EMC), a force sensor, a servo motor, a drive controller and an industrial PC with an intuitive HMI software, running device-independently on the browser and can be operated via tablet.
Zero programming
The Sensata engineers made use of visual programming: instead of coding line by line, they selected predefined software blocks and created a sequential workflow via drag and drop. In order to define the individual processes in the joining procedure, they simply enter the associated parameters. The drive controller is automatically parametrized and commissioning is supported by a wizard.
“Compared to the previous practice, the engineering time is reduced by up to 95 percent,” said Steinmetz. The simple analysis of the pressing process with validation elements ensures time savings within the operation phase.
For monitoring purposes, status information and process results including a force displacement curve are shown and recorded live. “All data are transferred straight to our IT system where they are stored and analyzed for quality assurance purposes,” reported Hubsch. “This means much greater transparency during production.”
Precise individual processes
The high quality and precision of each individual hardware component were also reasons why Sensata engineers chose the Smart Function Kit. It’s current task of pressing in the housing flange with the help of three distance bolts, is carried out with a maximum force of 800 daN and +/-0.02 mm accuracy. Although the configuration of the products on the line varies considerably, the solution is 100 percent reliable. In the final stage of the production line, the Smart Function Kit obtains the individual production parameters from a chip on the workpiece pallet via an RFID solution.
Versatile all-rounder: the modular TS 2plus transfer system performs a wide range of transport tasks with standardized modules. (Copyright: Bosch Rexroth)
Scope for line integration
To further simplify the engineering of the line, Sensata also opted for a modular transfer system from Bosch Rexroth. The Rexroth TS 2plus system likewise comprises standard components which can be combined flexibly. The line is also controlled by the XM21 embedded control system from Rexroth. Thanks to open interfaces, the Smart Function Kit can even be integrated easily into line control systems from third-party providers if necessary.
Smart from dimensioning to maintenance
Hubsch explained that with the flexible transport system and the integrated Smart Function Kit, Sensata has found an easy-to-use system kit which allows high-quality and cost-effective joining applications. Thanks to Rexroth’s LinSelect software tool, the dimensioning process is straightforward. The convenient online configurator helps with finding the appropriate composition and enables the download of the CAD files before ordering the final system via the Rexroth e-shop.
“All components were supplied already preconfigured in a single package,” said Hubsch. Bosch Rexroth is now looking to further develop the software by adding additional function blocks, e.g. a predictive maintenance module for optimizing maintenance.
In the next step, Hubsch would like to increase the number of sensor types on the line. There are also plans to duplicate the line and install it at other international sites. With the help of Bosch Rexroth’s global support, the solution will be internationally scaled and will continue to grow step by step.
Smart MechatroniX for the Factory of the Future
The Smart Function Kit from Bosch Rexroth is the first of three innovative solution packages offered as part of the new Smart MechatroniX solutions platform. According to the motto “Plug & Produce, Perform, Proceed” pre-configured and ready-to-use system solutions comprising proven hardware and intelligent software are paving the way for the Factory of the Future.
The Smart Function Kit for pressing and joining tasks is followed by one for handling tasks: a Cartesian single or multi-axis system that’s combined with proven linear motion technology components, innovative control systems and software to form a perfectly tailored complete package.
Another Smart MechatroniX solution, the Smart Flex Effector, will follow later. This is a sensor-supported compensation module with independent kinematics in six degrees of freedom which is designed to increase handling accuracy. The compensation module will also allow entirely new areas of use and applications for robots and Cartesian systems.
The content & opinions in this article are the author’s and do not necessarily represent the views of ManufacturingTomorrow
Comments (0)
This post does not have any comments. Be the first to leave a comment below.
Featured Product
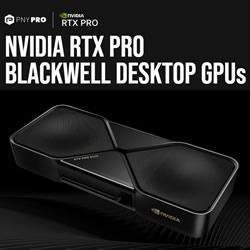