Unpredictable markets, an unstable procurement chain and impatient customers are just a few challenges your supply chain deals with. Balancing supply, demand and capacity has reached such a level of complexity that automation is increasingly sought after.
Automating Materials Handling - Automation to Support Supply Chain Woes
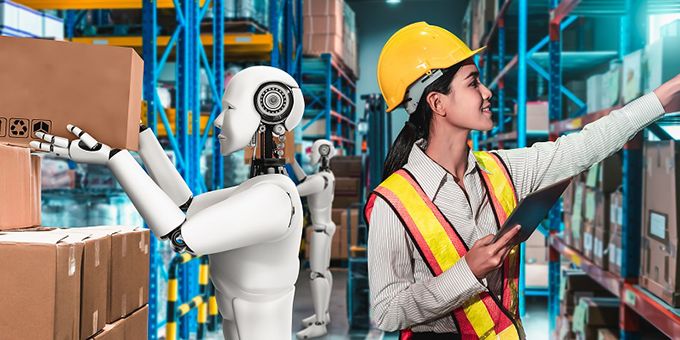
Claudia Jarrett, US country manager | EU Automation
Here, Claudia Jarrett, US country manager at industrial parts supplier EU Automation, explains why warehouse managers should look to increase their investment in automation.
Business Wire reports that more than 80 per cent of the warehouses today have no automation whatsoever. However, it is expected that companies will ramp up investment into warehouse automation in the next few years. In fact, a Gartner survey states that 75 per cent of companies will have integrated intralogistics smart robots into their warehouses by 2026.
Simply put, warehouse automation is the process of replacing repetitive tasks with automated systems. The goal here is for these automation systems to eliminate labor intensive and time consuming duties. Doing so, in turn, frees workers up to focus on more value-added tasks, such as quality control.
Intralogistics smart robots are designed specifically to support warehouses and distribution centres. Automation of this kind is becoming increasingly sought after in response to rising labor costs and the skills shortage. That’s also not to forget the increased demand on warehouses resulting from the COVID-19 pandemic and from recent materials shortages that impacted all sectors of manufacturing.
With smart solutions to fit all budgets, there are several reasons to consider increasing your investment in automation. Investing in them now can be a great step to future-proof your business and gain a competitive edge, so let’s explore why.
Safety first
Safety is one of the key reasons to implement automation in your facility. Robots in warehouses perform inherently dangerous tasks, such as reaching items on high shelves. Secondly, they also help to prevent injury or sickness, resulting from general worker fatigue. Common injury causes range from using improper lifting techniques, to working erratic shifts. These benefits are reinforced by a research article published recently by the Harvard Business Review, where workers cited it as the number one benefit.
Furthermore, the same study cited an additional benefit that is being applied during the era of the pandemic. A stocking associate at a retail chain in Michigan stressed that her warehouse was safer following COVID protocols. “With just the push of a button, the cleaning robots drive around cleaning the floors and wiping everything down the whole night.”
Customer satisfaction
Investing in a fully automated warehouse system will increase operational efficiency and better address growing customer demands. In today’s fast paced world consumer expectations for receiving products and services are higher than ever. Thankfully, today’s smart warehouses have much higher throughout, are immediately restocked and resupplied and allow for services like same-day delivery.
For example, using technologies such as scanning, bar codes, RFID tags, blockchains, IoT, analytics and AI, companies can drive faster order delivery, improved tracking and reduce losses and damage to packages. Better order tracking and real-time updates about in transit and delivery status can also help to enhance customer satisfaction.
In addition, operations can also be automated and simplified, such as validating and sorting packages while unloading with the help of technology, routing them appropriately and minimizing delays in delivery through dispensing accurate information to delivery personnel and customers. Such technology ensures more uniformed and desired results, despite the skill of handlers.
Automation options
One option is automated material handling systems (AMHS), which ensure efficient transport of material from one place to another in the manufacturing area. This machine can be used in the same department or bay, on opposite ends of the manufacturing floor, or even in two separate buildings.
An AMHS uses route and process step information provided by the manufacturing execution system (MES) to move material using conveyers, vertical elevators, and autonomous vehicles. Several other advanced technologies are used for the identification of material. These include radio-frequency identification (RFID), barcoding, optical character recognition (OCR), near-field communication, or ultra-wide band indoor tracking to detect the location of a material or carrier for transport by the AMHS.
No human interaction with carriers, transport systems or material is required with a fully implemented AMHS. The AMHS independently controls the identification, routing and delivery of material to the appropriate tool. The machine even places and removes the material from the load ports on the tool. If this process is done solely by human efforts, it can be costly and even risk worker safety and product damage as manufacturing incorporates many steps at many stations during the lifecycle of the transported material.
There’s more?
The sky is the limit when choosing automation options. Even smaller jobs, such as removing recycling from the shop floor, can be automated. For example, Fetch Robotics’ Autonomous Mobile Robots (AMRs) can be programmed to pick up recycling at custom time intervals, according to a warehouse’s needs. This frees up workers to perform more valuable tasks, resulting in improved employee satisfaction.
A recent article from McKinsey anticipates that investing in integrated solutions across the three main areas of materials handling — warehouse management, shop-floor operations and field operations — may be an effective strategy to future-proof your business. These share a few familiar success drivers, including accuracy, reliability and cost efficiencies.
In warehouse management, crucial success metrics include picking and sorting speed and tracking accuracy. Whereas shop-floor operations value timely delivery of products to production lines and low operating costs. Finally, the field-operations use case benefits from mechanical capabilities such as construction, mining, ports and the flexibility to handle multiple operations simultaneously.
Whatever your automation setup, whether a hybrid mix of new and legacy systems that includes obsolete products, or a new integrated solution, EU Automation can help. If you need obsolete automation equipment to improve your facility, visit the EU Automation website to find out more.
The content & opinions in this article are the author’s and do not necessarily represent the views of ManufacturingTomorrow
Comments (0)
This post does not have any comments. Be the first to leave a comment below.
Featured Product
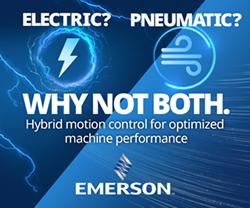