Many investments made by manufacturers over the past two years delivered new capabilities and efficiencies that should be carried forward as manufacturers look to the future in search of new business growth.
Four Lessons Manufacturers Learned from the Pandemic
Naveen Poonian, CEO, | iBASEt
A year and a half into the pandemic, the manufacturing industry has undergone significant disruption and transformation. For a sector that works primarily on-site in physical spaces, the workflow and production changes were abrupt and highly impactful. Leaning on technology, adapting quickly to new demands and supply chain restrictions, and adopting contactless safety processes—all while maintaining productivity and manufacturing essential items to fight COVID-19—were enormous challenges to overcome.
As we look to the future when work-from-home, restricted travel, and social distancing mandates go away, the technology investments that were made to operate during the pandemic should not be thrown out the window. Many of those investments delivered new capabilities and efficiencies that should be carried forward as manufacturers look to the future. Here are four lessons learned from the coronavirus pandemic that I have observed that can be leveraged to drive new growth opportunities. Given all that has been done to change how we work – is there a way to get more value from all this investment?
Moving from Remote Work to Sharing Expertise and Working Anywhere
During the pandemic, our industry had to come to grips with enforced lockdowns that relegated many of their staff to a work at home or remote working model. Companies that invested in video conferencing, collaboration, and secure networking technologies so technical, support, and supervisory employees could access corporate systems.
As vaccination adoption starts to get us closer to “normal,” avoid the temptation to return to business-as-usual. Manufacturers should leverage this remote access to improve the quality of their workforce as well as making the expertise of their most skilled staff more widely available.
By leveraging remote access, manufacturers can recruit and have access to a much larger pool of potential employees who may not wish to relocate to your location but have the skills you critically need. At the same time, you can leverage your newly developed collaboration platforms to allow the best-of-the-best of your experts to share their expertise across your organization and extended value chain.
Sustaining Safety and Operational Best Practices
Another one of the lessons learned from the coronavirus pandemic is how to operate with greater safety and hygiene. The mandated social distancing, contact tracing, sanitation, and masking requirements we have been practicing led our customers to invest in technologies such as RFID, Wi-Fi, or GPS technologies to enforce social distancing rules. This data helped to aid in contact tracing when positive exposures occurred. Visual recognition technology investments helped to enforce masking requirements in some plants.
Artificial Intelligence (AI) and other technology investments such as robotics helped some manufacturers develop and deploy automation that helped reduce the need for human interaction and reduce sanitation requirements.
All these investments can be leveraged to maintain the labor productivity and safety gains that were achieved during the pandemic. Auto-detection of proper safety equipment use, using tracing technologies to enforce human to automated machine interlocks, and expansion of the use of robots, can all further improve safety and productivity gains.
Leveraging Cloud and Remote Support to Reduce Technical Debt
While Manufacturing Execution Systems (MES) have been migrating to the Cloud for several years, the pandemic accelerated this trend. With travel restrictions precluding on-site installation of upgrades or new systems, Cloud deployment became a way for manufacturers to gain access to the latest capabilities during COVID-19. Those utilizing a cloud-native application architecture not only benefit from their initial Cloud investment, but as each iterative version of the software is deployed in the Cloud, access is immediate to incremental improvements as well.
When coupled with the ability to rely on remote support or a cloud-hosted MES application, technical debt can be minimized. Manufacturers that have not yet migrated to the Cloud should do so as soon as possible. Those that did should strive to take advantage of new product capabilities as they are introduced to foster a continuous improvement culture in their operations – a necessary attribute in the journey to identify future opportunities for growth.
Remaining Resilient and Agile
Perhaps one of the biggest lessons learned from the coronavirus pandemic was that manufacturers had to become far more resilient. The need to adapt quickly to a rapidly evolving environment became paramount. From labor and working situations to supply chain challenges, manufacturers that survived the pandemic had to be more agile as CDC guidance and local regulations continued to change as the pandemic evolved.
When we return to what our new “normalcy” becomes, manufacturers should avoid the temptation to return to “business as usual.” While bringing the entire workforce back to the plant or office may seem like a way to simplify operations and get them back to pre-Covid performance, the odds are that you will forfeit much of the agility your company developed over the last 18 months.
I would propose that the greatest lesson that smart manufacturers will have learned from the pandemic is that they can be more agile and adapt faster to change and challenges – much more so than previously considered. This realization opens the door to new business and growth opportunities that might now be possible with minimal additional new investment. Those that constantly strive to maintain that agility and leverage it will be rewarded, starting by staying ahead of their competition.
The content & opinions in this article are the author’s and do not necessarily represent the views of ManufacturingTomorrow
Comments (0)
This post does not have any comments. Be the first to leave a comment below.
Featured Product
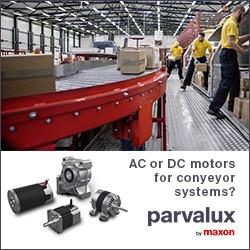