The benefits of automation are widely known, and most manufacturers aim to incorporate it into production to some degree. However, many of these targets have so far only resulted in plans, pilots or small scale automation projects.
Scaling Up Production, Fast - How Manufacturers Can Increase Productivity to Meet Growing Demand
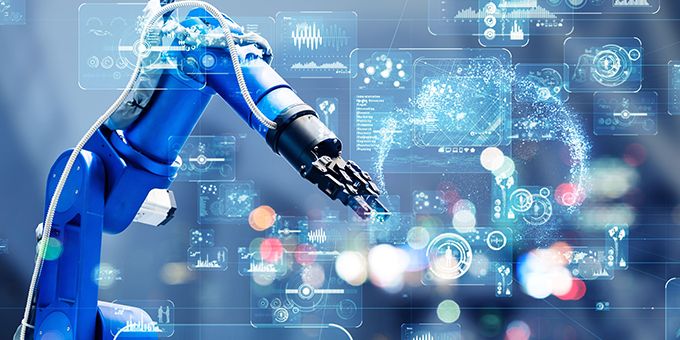
Dave Walsha, Sales Manager | EMS
The IHS Markit/CIPS Manufacturing Purchasing Managers' Index (PMI) value for May 2021 demonstrated that UK manufacturing is growing at its fastest rate in almost 30 years. Manufacturers must increase production to capitalise on the record growth in new orders. However, scaling up production quickly without additional floor space and workers can be challenging. Here Dave Walsha, sales manager at precision drive system supplier EMS, explores how expanding automation holds the answer.
In the PMI, any reading above 50 indicates growth. The value announced for May 2021 was 65.6 — the highest reading since the survey began in 1992. The easing of lockdown has unleashed pent-up demand, causing a steep increase in production volumes.
The plentiful market provides hope for manufacturers to bounce back after the pandemic by using the high demand to make up for lost profit. To make the most of this opportunity, manufacturers must quickly ensure their facilities are ready to accommodate the influx of new orders.
Accelerate automation
Scaling up production requires investment in high quality equipment. The benefits of automation are widely known, and most manufacturers aim to incorporate it into production to some degree. However, many of these targets have so far only resulted in plans, pilots or small scale automation projects.
In fact, research conducted earlier this year by supply chain specialist Balloon One found that the UK lags behind ten other nations with similar levels of manufacturing, including Sweden, USA and Italy, for robot density. The investigation also found that the UK falls behind in productivity levels, which is arguably due to lower levels of automation.
Investing in automated equipment is an efficient way to increase production, as it doesn’t require the company to hire a large number of extra workers. In addition, it’s possible to increase manufacturing productivity in the same floor space.
Select reliable components
In order for UK manufacturers to profit from growing demand, they must widely rollout automation across the supply chain. However, not all automated machines are built equal, and the components engineered into their systems play a large role in their overall performance. Manufacturers must remember that automation is an investment, that must be thought through with care.
When scaling up production, it’s important that manufacturers and design engineers don’t look for quick fixes. The new machines implemented should be not only able to accommodate the recent rise in orders, but also continue to benefit production in the long run.
Therefore, it’s important that automated machinery components, particularly their powering motors, are selected for reliability. An unreliable motor can ultimately lead to failure, but it’s important to note that, before it even reaches that point, a motor can cause inefficiency. In fact, an inefficient motor can result in electricity running costs that account for 97 per cent of its lifetime costing.
Automated equipment should be designed with dependable motors, such as the DMN range of brushed motors, which are renowned for their high quality and long life, while remaining a cost effective solution.
The motors have an optimised brush design that allows intermittent operation over one million cycles, and a continuous operating life of 3,000 hours. This long life cycle is achieved while still delivering a high output due to the range’s enhanced heat dissipation and resistance.
UK motor supplier EMS has a selection of sample stock of the DMN brushed motor range available for express delivery to accelerate development of automated equipment. EMS also has a selection of complementary gear heads, reduction ratios and encoders available to suit a variety of manufacturing applications.
After the challenges of the pandemic, the UK manufacturing sector is now seeing a sharp rise in demand. Manufacturers must prepare their factories to accommodate the increased volume of orders. Facility managers who widely implement automated equipment designed with reliable and cost effective components can quickly scale up production to meet rising demand.
The content & opinions in this article are the author’s and do not necessarily represent the views of ManufacturingTomorrow
Comments (0)
This post does not have any comments. Be the first to leave a comment below.
Featured Product
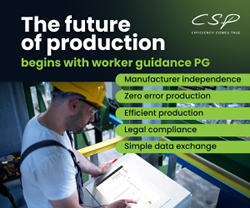