The demands on manufacturers are enormous: it is not only a matter of producing large quantities quickly, but also of maintaining particularly high quality standards. At the same time, increasing production capacity is usually time and capital intensive.
Vial Check - Intelligent Multi-camera System for Quality Control of Vaccine Bottles
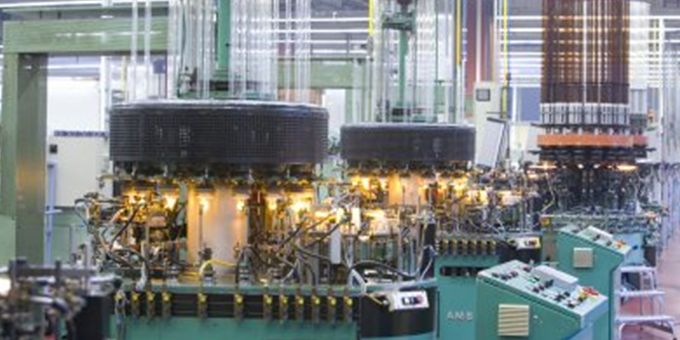
Article from | IDS Imaging Development Systems
Combating the Covid-19 pandemic is at the top of the global agenda. Around the world, efforts are being made to supply the population with vaccine as quickly as possible. But providing around 8 billion doses - at least one for every person in the world - is no easy task. Glass vials are a crucial factor in the delivery of the billions of doses of vaccine. About 50 billion of them are produced worldwide every year. Currently the producers of the vials are massively ramping up their production so as not to become the proverbial bottleneck in the supply chain. However, medical-grade vaccine vials are not standard glass tubes. Whether rolled-rim bottles, threaded bottles or ampoules, they are all made of the special glass borosilicate and require customized production lines. Any interaction between the container and the liquid inside must be prevented, as any chemical interference could affect the vaccine. Even the smallest scratch, crack or fissure can render an entire batch unusable, contaminate the line during the filling process or even lead to a machine standstill.
The demands on manufacturers are enormous: it is not only a matter of producing large quantities quickly, but also of maintaining particularly high quality standards. At the same time, increasing production capacity is usually time and capital intensive. A cost-effective, quickly integrated, extremely reliable solution for inspecting vaccine vials comes from Bad Königshofen in Germany: Isotronic GmbH, has developed the automatic tubular glass inspection system "VialChecker". IDS industrial cameras from the uEye CP camera family are used as image processing components for dimensional and surface inspection.
Application
Vaccine vials usually hold between 2 ml and 100 ml of liquid. They are on average 45 mm high and 11.5 mm wide. Manufacturers use borosilicate glass for this purpose to keep the vaccines in the required stable condition during storage and transport - even at extreme temperatures. The small containers for the precious contents are subject to high quality requirements. At the same time, large quantities currently have to be produced in the shortest possible time. What is needed is very fast quality control with high reliability in defect detection - how can that work?
Rolled rim bottles, threaded bottles or ampoules made of borosilicate glass for vaccines are subject to the highest quality requirements
Take high-performance cameras that have high-resolution sensors while enabling high frame rates and combine the GigE industrial cameras from the IDS uEye CP family with industrial-grade touchscreen monitors, control cabinet, connection to the respective production system and intelligent software. VialChecker is the name of the all-in-one inspection system for automatic dimensional and surface inspection of vaccine vials, available in two versions. Compliance with the dimensions is checked by the "VialChecker Geometry", while the "VialChecker Cosmetic" checks the surface of each individual bottle for flawlessness. The latter can optionally be used as part of the geometry inspection or take on more demanding tasks as a separate system.
The VialChecker Geometry contains more than 50 dimensional checks and performs tests for both standard and non-standard tubular glass products with a measurement accuracy of up to 0.01 millimeters. Defects such as cracks, scratches, chips, inclusions or stains, on the other hand, are detected with an accuracy of 0.1 square millimeters thanks to the powerful cameras. Intelligent software enables accurate fault description analysis and classification.
Testing takes place at various points in the manufacturing process, such as directly after the bottles have been formed or shortly before packaging. A system usually supports between three and eight cameras, so that different measuring stations can be integrated along the production line. "Depending on customer requirements, the system is specified or supplemented with appropriate sensors or cameras, for example to measure glass thickness," explains Valentin Mayer-Eichberger, Chief Operating Officer at Isotronic. "If more than eight cameras are needed, several computers are sent into action." For example, they observe the laterally rotating tube glass or the glass bottom and provide high-resolution images.
The multi-camera system "VialChecker" enables high-speed processing in the quality control of vaccine bottles.
The cameras capture at least 20 images per rotation, allowing the VialChecker to check up to 120 vials per minute with a very high degree of accuracy. It is up to 0.01 millimeters for dimensional tests and 0.1 square millimeters for cosmetic tests. In addition to real-time, low-latency processing, there is detailed logging of system operation. The high reliability of the software ensures that the products are within the geometric product specification and are error-free, while meeting the quality requirements.
Depending on the requirements and the testing task, different camera models are needed for the measuring station. Currently, Isotronic mainly uses the IDS camera family GigE uEye CP. They offer maximum functionality with extensive pixel pre-processing and are perfect for multi-camera systems such as the VialChecker thanks to the internal 120 MB image memory for buffering image sequences. The cameras deliver data at full GigE speed and, thanks to PoE ("Power over Ethernet"), also allow single-cable operation up to 100 meters.
One of the preferred models is the UI-5250CP-M-GL with a 2 megapixel CMOS sensor, one of the most sensitive sensors in the IDS portfolio. It is available in two versions, mono and color, and is characterized by outstanding light sensitivity. In addition, it offers various switchable shutter modes that enable the image-true capture of moving subjects or the particularly noise-free recording of high contrasts. "This is particularly important for the fast, reliable detection of defects on the glass surface," says Valentin Mayer-Eichberger, explaining the choice of the uEye+ camera from IDS. This allows either several characteristics to be checked simultaneously or the AOIs to be captured in an exposure series with different parameters.
This small powerhouse with a frame rate of 52 fps is thus predestined for the various inspection tasks along the production line - at high speed: "The system enables high-speed processing, it manages up to 120 cycles per minute," Valentin Mayer-Eichberger underlines. Besides the convincing performance of the cameras, however, other factors play a role: "We appreciate the uniformity and durability of the IDS cameras. And the service," says Gregor Fabritius, Managing Director of Isotronic, explaining the historically grown, long-standing relationship with IDS.
Software
The IDS cameras are directly connected to the system using C++. A software algorithm developed by Isotronic GmbH detects errors and outputs the error message via the monitor. "We not only have a measurement system that reports good/bad, but also records the quality of each product and displays statistics over time. The machine adjuster uses this to check that everything is still correct and that the bottle has been adjusted well."
Left: Rough environments in the moulding process place special demands on the protection of the cameras. Right: Modern software that is also intuitive to use. The machine operators appreciate that.
The Isotronic software has an intuitive, user-friendly interface that has been developed to meet the needs of customers. In addition, the VialChecker is optimized for remote support with continuous updates and software improvements. Valentin Mayer Eichberger is convinced: "This is the basis for a dynamic, sustainable system. We use machine learning for demanding tasks such as error classification.” On-site or cloud-based solutions for handling large amounts of data, as well as detailed analytics and process optimization are part of the scope of services. It is possible, for example, to analyze the frequency of faults over time as well as to monitor tool wear and raise alarms. The cloud service for production monitoring is extensive: "At the end of production, we calculate charts per quality measure. Certificates on the accuracy of the measurements can be issued for the acceptance of the measurement system."
Outlook
Experts estimate that global demand for vaccine vials will further increase by one to two billion over the next two years. The head of AstraZeneca, one of the major vaccine producers, also warned early in the pandemic: "There are not enough vials in the world." Vaccine vial manufacturers worldwide are ramping up production of the glass that is supposed to protect the precious liquid. To ensure that this valuable liquid is protected accordingly, automatic, high-performance testing systems are more in demand than ever to guarantee the immense demand for quality. "In addition, there is a general growth in the industry and in demand from the Asian region - and that even before the pandemic," notes Valentin Mayer Eichberger. Good prospects for systems like the VialChecker: It helps producers avoid becoming a bottleneck in the vaccine supply chain.
The content & opinions in this article are the author’s and do not necessarily represent the views of ManufacturingTomorrow
Comments (0)
This post does not have any comments. Be the first to leave a comment below.
Featured Product
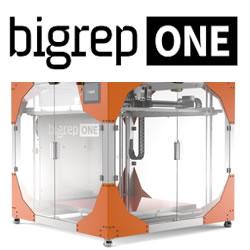