A lot has been said about “digital transformations,” and with good reason. Companies that want to survive realistically in a world with global competition and pressures require a paradigm shift to move forward.
The Rise of Smart Data in Manufacturing
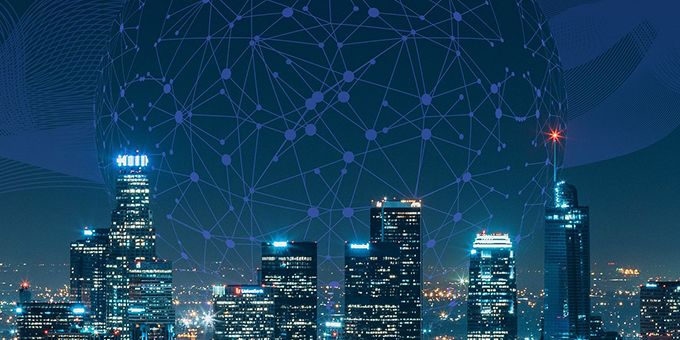
Martin Banks | Modded
But what is smart data, and why is it so significant in the manufacturing world right now?
What Is Smart Data?
Smart data and smart data analytics are major components of Industry 4.0, or the Fourth Industrial Revolution. Digitization enables the capture and transmission of data between processes and personnel across the modern manufacturing environment.
Data typically follows a path along these lines as it travels through a smart factory:
-
Data collection: Sensors throughout facilities and onboard vehicles collect data on equipment condition, workforce productivity and workflow metrics, such as pace and defect rates.
-
Data organization: Information technology (IT) and enterprise resource planning (ERP) platforms capture and organize this incoming data to draw insights, usually with the help of machine learning to automate the process.
-
Data utilization: Decision-makers use this organized data to plan equipment maintenance and upgrade cycles, make workforce adjustments, anticipate delays or demand, synchronize with partners or other plants and fine-tune their energy consumption.
If you’re connecting the dots, you can see smart data allows a higher level of virtual integration between the factory floor and the C-suite, the supply chain and business partners like vendors and distributors. Smart data is detailed, plentiful, real-time and, most importantly, actionable. It provides intel to help all the parts of the modern industry work better together.
Let’s look at some practical ways the rise of smart data is positively impacting the manufacturing sector.
Realizing the Benefits of Smart Data for Manufacturing
Manufacturers must become more agile if they wish to remain competitive. Companies must produce a variety of increasingly sophisticated products for numerous audiences, all while under tightening regulatory and consumer expectations. Then, they must get them to end-users as quickly as possible in an ever-more-complicated world.
Smart data unlocks the productivity, efficiency and equipment reliability manufacturers require to meet these ever-higher expectations. According to analysts, the advantage and head start enjoyed by the world’s top manufacturing performers is dissolving. A big part of the reason for this is that technology has democratized the industry and nearly leveled the playing field for smaller competitors.
Specifically, smart data provides the following opportunities for manufacturers:
1. Better Product Quality and Defect Management
Manufacturers can leverage their historical defect and quality assurance (QA) data to train machine vision stations to carry out product inspections. Machine vision isn’t susceptible to fatigue after long shifts and is more accurate than human QA personnel.
Better still, adopting automated inspection can upskill rather than displace the human workforce. It’s an answer to high defect rates and low numbers of skilled applicants, not to mention an additional layer of protection against problematic products, recalls and reputational fallout.
2. More Effective Maintenance and Longer Machine Life
Downtime after equipment failure is costly in any type of manufacturing environment. In the automotive sector, the cost of downtime can run as high as $22,000 per minute for every machine that’s out of commission.
In a smart factory, sensors on production equipment feed data on the machine’s operation — including energy used, sound and vibration and takt time elapsed — into algorithms. These smart systems compare the real-time performance of machines and components against benchmarks, thereby predicting when failure is likely or pinning down the optimal time to perform maintenance or replace parts.
The result is a more effective equipment budget, longer-lasting assets and far less worry about unforeseen downtime impacting profitability.
3. Fine-Tuned Workflows
Automated and manual manufacturing, assembly and material handling equipment can yield valuable process data. This data helps decision-makers and stakeholders make more targeted, specific and effective decisions concerning personnel, investments and workflow design.
Access to enterprise-wide smart data shows which processes experience bottlenecks, when they occur and why. It can uncover opportunities as well as hidden, specific and impactful problems, such as poor synergy between two departments during a shift, or a particular freight company that’s delivering materials later and later each month.
Just like monitoring a piece of equipment for parts failure, monitoring processing times, throughput and other “human” metrics shows which parts of the process no longer suit the application.
4. Improved Design and Circular Economy
If you’re not already familiar with the concept of a circular economy, you soon will be. This is an economic model for the future that prioritizes long-lasting products, sustainability and a healthy third- and first-party marketplace for secondhand, refurbished, recycled or otherwise reused products.
Even at the component level, complex products like powered equipment and electronics generate a considerable amount of data on how a product is used and what conditions it must withstand in the field to perform well.
Some major manufacturers, including Philips, have received recognition for their efforts in building this circular economy. Using product and customer data in this way improves merchandise longevity, keeps raw materials in the earth, generates brand loyalty among eco-conscious consumers and builds robust marketplaces for refurbished products. Each of these factors reduces the pervasive problem of e-waste and the conflict and exploitation surrounding the mining of precious metals and other resources.
5. Enhanced Energy Usage and Sustainability
Finally, smart data and smart machines pave the way to smart energy usage. Smart machines provide detailed telemetry on how much energy each department within a facility uses and when they tend to use it. Industrial activity consumes some 54%of delivered electricity across the globe, making this an ideal time to manage supply and demand using smart data.
Anything that uses motors or pumps or manipulates temperatures, including heating, refrigeration, washing, mixing, processing and material handling processes, consumes considerable energy. Smart factories spot which machines use more energy over time, a factor which might signify impending component failure.
They also pinpoint periods where energy is being used and paid for unnecessarily, plus opportunities for fine-tuning the performance or runtime of major equipment or infrastructure.
With all of these clear benefits, interest in smart data and the Internet of Things (IoT) among manufacturers is set to explode in the coming years. Between 2017 and 2022, analysts expect the manufacturing IoT market to grow by 29% per year and reach $45.3 billion in value.
A Booming Market for Smart Data in Manufacturing
Given the competitive advantages we’ve been exploring, it’s easy to see why smart data is growing exponentially in manufacturing. Companies that invest in smart data infrastructure today will be more flexible and competitive tomorrow and better able to remain stable in a world that’s anything but.
The content & opinions in this article are the author’s and do not necessarily represent the views of ManufacturingTomorrow
Comments (0)
This post does not have any comments. Be the first to leave a comment below.
Featured Product
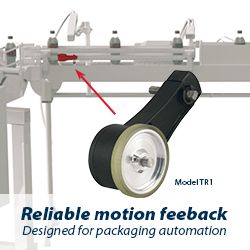