Research continues to develop regarding how the die casting process can improve in speed and efficiency. 3D printing for die repair is a notable focus, with die casters and the North American Die Casting Association embracing additive manufacturing technologies such as 3D printing for efficiency and accuracy purposes.
Can Manufacturers Use 3D Printing for Die Repair?
Megan Ray Nichols | Schooled By Science
The development of 3D printing methods that aim to extend the life of machine dies continues to have an impact on die casting, forging and extrusion dies. Despite such developments, additive manufacturing won't replace traditional manufacturing processes like die, since both have their strengths and can combine for optimal results.
3D Printing and Die Repair
3D printing is one of the several areas of research for optimizing methods for tools, with cold plasma spraying and cladding also providing alternative methods. 3D printing integration is at full speed with various research teams. At Case Western Reserve University, work is underway with a project led by Professor David Schwam, whose team is aiming to work with rough die forms and restore their worn or damaged surface details with 3D printing processes.
The rough die process reduces the limitations of 3D printing regarding handling the dimensions of the build box, the typical obstacle for additive manufacturing and one example of why additive manufacturing will not replace traditional manufacturing processes. Combined, however, the methods can produce exciting results that save costs for manufacturers while providing consumers with a more accurate, durable mold or die replacement.
Additive manufacturing has also helped increase structural resistance to thermal fatigue, resulting from cyclic thermal influences. 3D printers can design the mold with compliance for thermal expansion, at a faster rate and while using fewer materials than traditional methods. The printers can also incorporate lattice structures to serve as crack stoppers, helping prevent fluid leakage.
The project at Case Western Reserve University projects that additive manufacturing integration can save die casters up to $500 million in annual repair costs. This integration involves using cladding, cold plasma spraying and other welding technologies alongside 3D printing to optimize methods and materials for various tools. Once restored, these tools' performance will compare with new tools, the findings being a basis for specifications in future integrations.
Case Western Reserve University is taking the lead on two of seven related projects earning funding from the National Additive Manufacturing Innovation Institute (NAMII), established in August 2002 and whose aim is to “to accelerate additive manufacturing technologies to the U.S. manufacturing sector and increase domestic manufacturing competitiveness.” Governmental, scholarly and industrial support combine for a strong and durable research process that isn’t going away anytime soon.
Continuing Development with Additive Manufacturing
Naturally, with involvement from government labs, academic partners and industrial companies, there has been accelerating development in how 3D printing can help with die repair. In addition to the research from CWRU, there is a collaboration with Twin City Die Casting, NADCA, General Die Casters, Nebraska Aluminum Casting, DCD Technology and Delaware Dynamics, the latter two producing die casting molds.
Welding processes provide a great foundation for research due to the parallel between the joining process, the principles of phase transformation and the concept of attaching new material to a die surface. There are some esteemed partners aiding with integrating the welding process, including Lincoln Electric Co., the U.S. Army Research Laboratory and the Department of Army Research's Benet Laboratories, and Deformation Control Technology Inc.
There are a variety of casting methods, both expandable and nonexpendable. The efficiency and cost-saving nature of additive manufacturing are appealing in many cases, though the vast array of casting methods, which include sand casting, aluminum die casting, investment casting and V-casting, make integration of additive manufacturing methods more practical than serving as an outright replacement. Just as blending workplace materials can result in greater part performance and manufacturing efficiency, integrating additive manufacturing into the process can also increase performance and efficiency.
Die casters will benefit even more if researchers can successfully integrate 3D printing since the result will be an increase in the lifespan of each die. As a result, there's no doubt that many in the die casting industry will be paying close attention to research from the likes of CWRU. Additive manufacturing integration will continue to become more abundant, resulting in die casters producing material with a longer lifespan, consequently giving the die more value.
The content & opinions in this article are the author’s and do not necessarily represent the views of ManufacturingTomorrow
Comments (0)
This post does not have any comments. Be the first to leave a comment below.
Featured Product
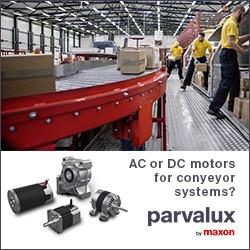