How to Reduce Waste While Ensuring Product Data Compliance
Contributed by | Microscan
Product traceability is a growing concern in industries from medical device manufacturing to consumer packaged goods. It is no longer sufficient for a manufacturer to produce high-quality products to ensure good standing with their customers and avoid rejects, fines, or recalls. Today, these costs are regularly incurred by the simple absence, inaccuracy, or illegibility of product data. Label verification systems can be implemented to safe-guard against these issues, but even misuse or misplacement of a verification system can cause loss in time and materials within internal operations. A systematic approach to label verification should be observed for the leanest labeling processes, with verification implemented at three critical steps during manufacturing:
Step 1: Verify label data structure offline after code creation
Step 2: Verify label compliance and readability offline after final artwork
Step 3: Verify label print quality inline directly after printing or applying to product
Label Standardization: Data Structure and Print Quality
Accurately documenting product data on labels and packaging is a critical component of manufacturing in today’s market. Demands for traceability are now enforced not only at the customer level, but through legal directives imposed by the FDA, EU, and other governing bodies. Manufacturers have the obligation to provide unique documentation for each product to ensure that data such as product origin, substrate material, expiration date, manufacturing history, and more, are readily accessible and auditable if problems arise.
Figure 1: A fictitious example of a medical device label that conforms to the requirements of the FDA’s UDI (Unique Device Identifier) initiative for device labels and packaging.
Emerging regulations further dictate that product data must be properly structured according to accepted standards to be accurately and universally interpreted by automated data acquisition systems. GS1 offers the most widely-used specifications for data structuring, which employ alphanumeric codes (called Application Identifiers) within code strings to designate meaningful data segments ranging from product category to manufacturer ID.
Figure 2: A Data Matrix symbol and matching human-readable text string containing data structured according to GS1 requirements. The identification keys in parentheses – (01), (10), and (17) – signify to the data acquisition system that the following segments of data are the product ID, batch number, and expiration date, respectively.
Proper structuring of barcode and human readable data according to GS1 ensures that data acquisition systems, regardless of the system, can obtain full traceability data on each product, regardless of the product or its origin. However, the slightest structuring error, from a missing GS1 Application Identifier to a misplaced numeral, can result in misinterpretation of product traceability data by the system, which may lead to rejects or fines due to noncompliance. These concerns, combined with the pressure to implement compliant codes according to federal schedules, have caused significant strain on manufacturers hoping to stay competitive.
Beyond proper code structuring, labels must comply with print quality requirements to ensure legibility of encoded data. A label whose codes contain all of the information necessary for traceability, which are properly structured per GS1 standards for compliance, is rendered useless if smudges, blemishes, or inconsistent printing prevent data acquisition devices (barcode scanners or cameras) from extracting the data.
Figure 3: The encoded data of this linear barcode may be accurate and properly structured, but inconsistency of the distribution of ink by the printing method may render the code illegible.
Like data structuring standards, print quality standards dictate that labels meet strict parameters for code appearance to ensure full label compliance. Compliant labels are those that have been verified to meet or exceed specific tolerances for print and aesthetic features such as symbol contrast, skew, damage, or other elements. ISO/IEC barcode print quality standards are used widely as a means of determining quality against established parameters and provide grades (A-F) to denote cumulative barcode print quality and legibility. Acceptable print quality tolerances can vary by industry or company, but in most cases a grade of D or lower cannot guarantee long-term readability of a code and will be deemed noncompliant. Labels with this low level of quality may cause rejected products or fines at the cus- tomer when codes are unable to be read or are graded to below the level of acceptable quality.
Figure 4: Verification software containing built-in ISO/IEC parameters for grading barcode print quality to standards-based compliance. The QR Code here has achieve “A” grades for the parameters Contrast, Modulation, Axial Nonuniformity, and Unused Error Correction.
The Cost of Noncompliance
Poor quality labels have the potential to cause huge losses in time and money for a manufacturer. When a shipment of high- quality product is rejected at the customer because of missing or inaccurate product data, a manufacturer stands to lose much more than the potential earnings from the product’s sale. There may also be material costs if products need to be scrapped, or material, shipping, and repalletizing costs if products need to be returned and reworked. Customers may impose fines to their suppliers to ensure manufacturer compliance and account for the resources to handle improperly-labeled product. Or, custom- ers may simply charge back a portion of the manufacturer’s invoice for receiving the noncompliant product.
Figure 5: The accuracy of product label data has serious implications, not only for supplier integrity, but also for consumer safety. For example, consumers with allergies or other medical conditions rely on labels to provide accurate information about a product’s contents. Label accuracy also enables suppliers to recall affect- ed product batches quickly if there is a product safety issue.
Many retailers impose fees per label (for instance, $5 per incorrect label) or per shipment of products (for instance, $200 per shipment). Chargebacks issued to vendors for product label noncompliance can also be incurred for as much as 15-20% of the supplier’s invoice, which for large shipments can yield losses in the tens of thousands ($10-20,000 or more) per invoice. With the adoption of globally-regulated standards like GS1 and ISO, the market has observed a new trend in which retailers issue separate fines for label print quality (missing or unreadable product label data) and code structure (improperly-structured data per standards like GS1). There are even greater long-term risks associated with supplying inaccurate labels, such as the deterioration of customer-supplier relations and the possibility of losing supplier status for repeated compliance violations.
Verification Systems
Verifying product labels for proper data structure and print quality before products ship is a simple insurance policy against loss and fines. By implementing barcode and print quality verification systems in their operations, manufacturers are able to guarantee legibility and standards compliance with precision, rejecting non-compliant labels before they are shipped on product. Verification systems also allow manufacturers to automate the process of label quality-checking, reducing man hours and potential human error to support leaner operations. Using machine vision cameras and sophisticated software, verification systems automatically compare label features to built-in parameters, grading to standards such as GS1 and ISO and providing compliance results at required tolerances for specific labeling requirements. With standards-based grading available within their equipment, manufacturers save additional time and cost associated with training staff for specific standards knowledge, allowing the verification system itself to be the standards expert.
Figure 6: A verification system installed on the packaging line uses a unique camera-and-lighting configuration to capture images of labels, which are verified for ISO/IEC print quality by machine vision inspection software.
Implementing a verification system is the first step to safe-guarding the ROI of goods shipped to customers. But for truly lean labeling operations, manufacturers must look more closely at their internal labeling operations and the advantage of a systematic implementation of verification at critical stages. Label quality issues can emerge at many points throughout the supply chain,
Figure 7: A systematic implementation of label verification can reduce waste at several points along the line, from code creation, to label application, to distribution.
from initial label or package design to product distribution. Data structuring errors may be produced when a barcode or text string is created. Readability issues may result from adjustments made to a code during label artwork design. Print quality issues may occur during inconsistencies at the printer, or damage during the manufacturing and distribution process.
For the leanest operations, verification should be incorporated wherever it has the potential to save cost. Even before product is shipped to the customer, there are several stages in manufacturing operations where time and material loss may occur as a result of label errors. A verifi cation system implemented too far down the line may not catch a labeling error until an improperly- structured code is printed, requiring entire runs of printed labels or packaging to be scrapped. A verification system implemented at the printer may ensure that labels are printed properly, but without additional verification down the line, damage or blemishes incurred as products move throughout manufacturing may allow illegible labels to escape out the door, resulting in customer fines. Establishing a lean labeling process means not only implementing verifi cation, but implementing it in such a way that it effectively eliminates waste at every stage of manufacturing operations. In general, there are three critical steps in manufacturing where verification should be implemented to ensure the leanest labeling operations.
Step 1: Verify Label Data Structure Offline after Code Creation
Ensuring the proper structure of product codes is the first step in the labeling process. According to GS1, there are ten steps to implementing a GS1-compliant barcode: requesting a GS1 company prefix (the manufacturer’s unique ID); assigning numbers; selecting a printing process; selecting a primary scanning environment; selecting a barcode type; choosing a barcode size; structuring the barcode data; choosing a barcode color; choosing barcode placement; and building a barcode quality plan. Each of these choices is limited by the compliance requirements that a manufacturer must meet based on their industry, type of product, or customer and legal obligations. With so many variables involved in the creation of a compliant code, and with such strict requirements per code, there are several places where errors can occur during code creation. Simply missing one GS1 Application Identifi er, data segment, or even a single numeral can cause a code to be deemed noncompliant.
Figure 8: The type of barcode selected for a GS1-compliant label is limited by the scanning environment (where the barcode will be read), among other factors. Once selected, the barcode must adhere to prescribed measurements (code size and bar/element size) to maintain GS1 compliance.
Lean product labeling relies on preventing errors before they result in unnecessary cost. Therefore, it is imperative to verify codes immediately after they are created to ensure that they do not enter the supply chain where valuable resources are at play. For the purposes of verifying data structure, there is no reason to use final label stock and ink to print a newly-created code. This testing process can be accomplished by printing new codes from any desktop printer and verifying code structure using an offline verification system (simply, a verification system that is not directly installed onto the line).
Figure 9: Verifying the structure of data on labels can be accomplished using any printing method. The first priority is to perfect label data, and then to perfect printing quality.
At this stage, print quality is not a concern and can be verified later once the code is finalized. As long as the verification system can read the code on the printout and extract its data, data structure alone can be checked for accuracy and errors can be diagnosed for further testing. Many offline verifiers are able to accomplish this verification step to GS1 compliance to ensure barcodes meet the necessary criteria for production before they are produced at 100% print quality, conserving label stock and printer ink for the final product.
Step 2: Verify Label Compliance and Readability Offline after Final Artwork
Once a code is created and verified to have the necessary structure for compliance, the code’s data and appearance must remain consistent for the final label. In terms of data structure, GS1 has strict requirements for the overall size and resolution of a barcode given its type (UPC, Code 128, QR Code, etc.). In terms of legibility, ISO barcode quality requirements specify that adequate white space (quiet zone) surround the code and that the code have a consistent aspect ratio to avoid skew, in addition to a variety of other attributes. If any of these features change from the time the code is verified, it is possible that the barcode may become noncompliant. It is critical, therefore, that the verified code remain unchanged so as not to print inaccuracies on final label stock – or worse, ship poor-quality codes on product. Why the concern that a barcode may change in the short distance from initial verifi cation to production? The distance may not be as short as it seems. It is fairly uncommon for a code to be applied alone to a product label or package, without the ad- dition of other data or visual elements. It is more often the case that a barcode is incorporated into label or package artwork by a design team in charge of the product aesthetic, from product data to logos and images. This team’s objective is to create a functional and appealing design, which may compete with the real estate that a code must occupy. If a code is reduced in size, distorted, recolored, or squeezed too tightly within the label artwork to accommodate design, the once-perfect features of the code may be lost and the code may fall out of compliance.
Figure 10: During the design of this label, the original Data Matrix code was stretched and resized. These changes may result in readability and compliance issues down the line.
A secondary verification step, therefore, should be incorporated directly after the final label artwork is designed as a final quality check before labels are applied to product. This step will ensure lean use of product materials and will prevent product or material scrap. At this point, the label or package artwork should be printed in final form at the printer, on true stock, to ensure that code resolution can be verified (in case the code has been resized) and that resolution issues are not a result of a poor printing method. An offline verification system can be used to verify the code at this step as well, where labels can be presented to the system for testing purposes. Both data structure and print quality should be verifi ed to ensure complete label compliance. After verifi cation is accomplished at this stage, it is time to begin final label printing and applying labels to product.
Figure 11: An offline verifier is used to scan a length of label artwork to ensure accurate data structure and print quality before applying labels to products on the line.
Step 3: Verify Label Print Quality Inline Directly after Printing or Applying to Product
Now that a perfectly-structured code has been produced and label artwork has been verified, data structure ceases to be a concern for label compliance. At this point, where the printer is the only element affecting label production, ensuring high-quality labels is simply a matter of ensuring print quality. For the lean- est labeling operations, an inline verifi cation system should be implemented as soon as possible after a label is produced to check print quality. An inline verifi cation system is optimal at this stage because operations have now transitioned from performing static tests to running live production. Inline verifi cation systems are uniquely engineered to verify label structure and quality at production speeds and can be directly installed on the line to monitor labels as they are printed and applied.
Figure 12: A label verification system is installed on the line to ensure consistent label codes and print quality at production speeds.
The earliest point at which an inline verification system can be installed on the line is during or directly after label printing. Verification systems that are designed to attach to or be installed inside of label printers ensure optimal waste prevention by catching print quality errors before the label reel passes the point of rewinding.
Figure 13: An inline verification system is attached directly to a Zebra® printer to ensure label accuracy while printing.
Otherwise, a verification system can be installed on the line directly adjacent to the printer to grade labels after they are produced. Labels can be graded against print quality verification parameters (such as those defined by ISO) to meet acceptable tolerances for either custom quality requirements (to ensure the long-term legibility of label codes) or for full standards compli- ance (to meet customer or legal obligations). If quality issues are detected, the manufacturer can be sure that these issues are the result of inconsistencies in the printing method, having already ruled out data structure issues. The manufacturer can then adjust the printing method to ensure compliance.
Figure 14: Verification steps can be added at any point along the line to guarantee label quality wherever errors may result and the verification system may contribute to cost savings.
Manufacturers can further extend lean labeling processes and guarantee label quality throughout operations by implementing additional inline verification steps at any point along the line. These checkpoints ensure that, as products move through each stage of production, any label damage or distortion that may occur is detected and rejected before the associated product ships and results in fines from the customer. These additional verification steps are a particularly valuable investment in fast moving or harsh manufacturing conditions where the variables of production may be harder to control and damage to packaging and labels is more likely.
Figure 15: Harsh manufacturing conditions may result in damage to high quality labels in production, so it is important to re-verify labels after any operational stage where damage is likely.
There is no limit to the number of verification steps a manufacturing line can have, but lean operations should apply verification only where it will capture a significant number of potential issues. It may be most beneficial to install inline verification systems only at points where a product is handled or after significant transitions in product position or environment. Since product codes and artwork have already been verified by this stage, the only concern for maintaining compliance is label print quality verification.
Conclusion
Implementing label verification to ensure accurate product data on shipments supplied to customers yields significant cost savings against noncompliance fees and increasingly strict supplier requirements for product traceability. However, manufacturers should not overlook the cost savings that verification systems are able to provide even further up the supply chain. When implemented at three critical stages of labeling (code creation, art- work design, and printing and application), verification systems provide a means of improving the cost-efficiency of operations to save on material stock, scrap, rework, and production errors to promote lean operations throughout label production. Using a combination of offline testing and inline quality assurance to verify that code structure and print quality are in compliance with quality standards regulated by global agencies like GS1 and ISO, manufacturers can eliminate waste from labeling and safeguard their investments in today’s demanding data-driven market.
References
1. Ten steps to GS1 barcode implementation. (2015, January). Retrieved November 17, 2015 from http://www.gs1.org/ ten-steps-gs1-barcode-implementation
2. The Kroger Co. (2015, January). Standard Vendor Agreement for Merchandise (Products). Retrieved November 17, 2015 from http://www.thekrogerco.com/docs/default-document- library/standard-vendor-agreement-(sva)-document-merchan- dising.pdf
3. [Untitled image of example of a unique device identifier (UDI) on a medical label]. (2013, September 18). Retrieved November 20, 2015 from http://www.fda.gov/MedicalDe- vices/DeviceRegulationandGuidance/UniqueDeviceIdentifi- cation/UDIBasics/default.htm
4. [Untitled image of various GS1 Barcodes]. (2015, July 28). Retrieved November 20, 2015 from http://www.gs1.org/ ten-steps-gs1-barcode-implementation
The content & opinions in this article are the author’s and do not necessarily represent the views of ManufacturingTomorrow
Comments (0)
This post does not have any comments. Be the first to leave a comment below.
Featured Product
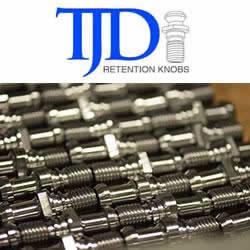