If your products have regular and stable characteristics, hard automation makes sense. If however each product is different, flexible automation or robotics should be favored.
Contributed by | Axium
4 Things That Will Help You Make a More Informed Decision About Automating or Robotizing Your Operations
1. Why do you want to automate or robotize?
Is it to increase throughput, reduce cost, lower waste, improve quality, add flexibility or avoid safety issues? There is no “perfect” automation project that will solve all of those problems at once. A choice has to be made. Of course, all manufacturers want to improve their OEE, which reflects productivity and quality. The main objective of your project needs to be determined in advance in order to give you a direction for the following steps and help you to choose the best technologies.
2. In what phase of the lifecycle is your product?
Your product’s lifecycle phase is usually a good place to start. If it’s in the “introduction” or “growth” phases, your motive for automation is probably to increase throughput to fuel the upward path of sales. If your products are in the “maturity” phase, where profit margins drop as competition increases, automation is usually done to reduce costs.
3. What is the lifecycle time of your product or task?
In the case where your product does not change much (or very little) over time, hard automation might be an appropriate approach. If you’re in the opposite situation where your products need regular updates or improvements, flexible automation or robotics should be considered.
For example, a company that always palletizes the same size of box will first consider a standard automated palletizer. They are efficient and well known, but they can be a pain when you decide to change your box’s format.
At the other end of the spectrum, let’s say you’re operating a distribution center and have to palletize various products; flexible automation based on robotics is the only practical solution. In this later case, a mixed load-palletizing cell provides the flexibility to handle the wide variety of products.
4. Are your products always the same (geometry, dimensions, weight) or are they different from one to the other?
If your products have regular and stable characteristics, hard automation makes sense. If however each product is different, flexible automation or robotics should be favored.
For example, if a plastic fuel tank manufacturer produces the same model in its production line for a few years, it should probably consider a dedicated approach using hard automation. It’s normally less expensive and easier to implement. Solutions offered by B+R Maschinenbau meet these characteristics.
Other plastic tank manufacturers that produce various models on the same line will want a robotized approach where simple parameter change enables the system to switch easily to another model. Such robotized cell are offered by Axium.
The content & opinions in this article are the author’s and do not necessarily represent the views of ManufacturingTomorrow
Comments (0)
This post does not have any comments. Be the first to leave a comment below.
Featured Product
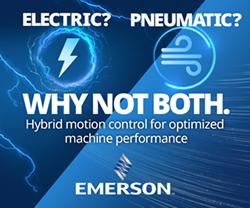