Using vision instead of proximity sensors makes it possible for each fixture to handle a wider range of parts.
Contributed by | Cognex
Volatile organic compound (VOC) free coating systems used for automotive interior components require flame treatment to increase the surface tension and improve coating adhesion. Traditional cells used for flame treating have four stations with a robot in each station applying or flame treating parts mounted on a turntable fixture with proximity sensors. Fitz-Thors Engineering Inc. has improved on this approach by producing a cell that provides the same throughput with a single robot serving all four stations. The vision system views the part prior to flame treating to ensure it is present and properly positioned in the fixture. The robot operates continuously, eliminating the considerable amount of robot idle time seen with conventional cells. The new robot approach also eliminates the need for proximity sensors, making it possible to handle a much wider range of parts and eliminating the time required for wiring the sensors. When running at full production, the new cells require four operators, the same as traditional cells. However, when running at less than full production the new cells can be serviced by two operators loading two cells each.
Traditional flame treating methods
Most plastic parts used in automotive interiors are coated to improve their feel and acoustic performance. Recent regulations have mandated the use of VOC-free coating systems based on polyurethane or ultraviolet coatings that require the substrate to have a high level of surface tension. Flame treatment is an inexpensive and efficient way to provide the surface tension levels that can help promote coating adhesion and eliminate the need for primers.
Flame treatment in the automotive industry is normally applied with a robot to ensure high quality levels. A typical vehicle interior might have several components that require treatment such as steering wheels, dashboards, consoles, glove boxes, etc. A traditional cell used to flame treat these components has individual stations with each station served by an individual robot. Each different part has a custom fixture with proximity sensors to ensure that the part is properly positioned in the fixture. Each fixture is mounted on a turntable to isolate operators from the robot. Operators load each part, then rotate the turntable to put the part and fixture into position for flame treatment by the robot.
Taking a fresh look
Fitz-Thors’ engineers decided to take a fresh look at flame treatment systems. They questioned why a robot was needed for each station when the robots spent much of the time sitting idle. They also asked whether machine vision might be a better approach than proximity sensors to ensure the proper positioning of the part. Fitz-Thors engineers came to the conclusion that a robot enabled with a vision system could move quickly around the cell to each fixture that was ready for flame treatment, verify that the right part was present and properly positioned in the fixture, flame treat the part in the fixture, and then move on to the next.
Fitz-Thors engineers selected the Cognex In-Sight 7010, an entry level vision system developed specifically for inspection tasks where vision sensors are too limited and standard vision systems may not be cost effective. They configured the vision system using the Cognex EasyBuilder user interface by selecting the pattern find vision tool with an angle orientation limit that provides a percentage match to ensure that the right part is positioned correctly in the fixture. The pattern-find function is able to locate the part anywhere in the field of view so the program can consistently detect the presence or absence of the part despite the fact that the fixture might be in a different position.
The In-Sight 7010 is a completely self-contained vision system that includes autofocus optics and integrated lighting in an IP67 rated industrial housing. With autofocus, users can simply set and save the focus values associated with the inspection of each part. Users can also fine-tune focus levels manually with the interactive software, enabling seamless part change over without any manual adjustment of the lens. The compact In-Sight 7010 features integrated white lighting that is suitable for most vision applications. If a specific color light is required to highlight particular parts or features, four optional colored lights are available.
An ABB IRB 2600ID robot fitted with an Enercon Dyne-A-Flame surface treater flame-treats the parts. IRB 2600ID robots route all process cables and hoses inside the robot arm to decrease downtime caused by interference and wear, a feature known as Integrated Dressing. Integrated Dressing also ensures that the maximum achievable acceleration is available at all times without restriction. The IRB 2600ID has a swing base radius of only 337 mm and a base width of only 511 mm. The surface treatment ignites flammable gas to form an intense blue flame and a plasma field. The flame changes the distribution and density of the electrons on the surface of the part and polarizes surface molecules through oxidation. Flame treatment also deposits other functional chemical groups that promote wetting and adhesion.
Cell for Tier 1 supplier
Fitz-Thors Engineering recently built a flame treatment cell for a major Tier 1 automotive supplier. The four station system uses a turntable to handle smaller parts while the other three stations are open to handle larger parts such as dashboards. The ABB SafeMove robot safety option enables operators to safely load parts on the three stations without turntables. Sensors monitor the location of the operators and SaveMove enforces geometrical and speed restrictions to maintain automatic operations while restricting robot motion to maintain a safe distance from the operators. A safe tool zone is continuously calculated based on operator position and the robot motion is restricted to stay inside the defined zone. The operator loads the turntable or loads a part into one of the open fixtures and pushes a green button. The robot control controls the robot based on the availability of parts in fixtures and the position of the operators. Operators can walk in and place parts in cells while robots are working in a different station.
Using vision instead of proximity sensors makes it possible for each fixture to handle a wider range of parts. Design changes can frequently be accommodated without having to make any changes to the fixture. In addition, the elimination of proximity sensors eliminates the need for a substantial amount of wiring when installing the system and also for rewiring when changes are made to the design. The vision systems cost about as much as the proximity sensors but their flexibility to handle future changes is much greater so they reduce the total cost of ownership. The single robot used in the cell continuously treats parts without downtime. The floor space occupied by the cell is considerably smaller than a traditional cell with four robots and four turntables. When the system is running at full capacity, it utilizes four operators to continuously load part for maximum throughput. Another option is to run at a reduced production rate with two operators each of who loads parts for two stations.
Fitz-Thors Engineering uses machine vision in a wide range of other applications. For example, the company recently completed an automated custom vision application for another Tier 1 automotive supplier. These test stands utilize Cognex vision systems and VisionView displays to verify the location and color of the screws and plastic clips on the inside of door panels. Machined fixtures ensure the door panel is positioned correctly by the operator. Once the panel is in position, the operator initiates the test by pressing two buttons. The display alerts the operator of a failed part by displaying a red box around the quadrant that failed as well as placing a red circle around the incorrect or missing fasteners. This visual indication allows the operator to quickly identify why the part has failed. The results are stored in a database, providing traceability in case future defects are found.
The first flame-treat cell shown here has been in successful operation for over one year. Fitz-Thors Engineering recently built a second system for the auto supplier. This new cell is capable of functioning as a backup to the current cell and will also make it possible to treat new components and increase throughput.
Plan view of four station flame treating cell featuring vision-enabled robots.
Station in cell with turntable used to treat smaller parts
One of three stations in the cell without turntable used to treat larger parts
In the two images above, vision-enabled robots apply heat treatment to interior components
For more information, contact Cognex, One Vision Drive, Natick, MA 01760-2059 USA. Tel (Toll Free): 1-877-COGNEX1 (1-877-264-6391), Fax: +1 508 650-3344, Email: pr@cognex.com,Web: http://www.cognex.com/
The content & opinions in this article are the author’s and do not necessarily represent the views of ManufacturingTomorrow
Comments (0)
This post does not have any comments. Be the first to leave a comment below.
Featured Product
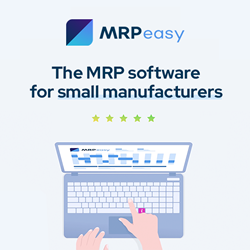