AI Capabilities Your Manufacturing Organization Likely Hasn’t Thought About
Artificial intelligence has certainly taken root in the manufacturing sector as organizations are realizing AI and humans must coexist to function effectively and productively. As AI continues increasing in prominence across the board – with projected growth of 37% until 2030 – now is the time to explore more creative and useful ways to leverage AI in the manufacturing industry.
Aside from its data-rich mining and productivity enhancements, AI can provide advantageous returns to further aid and elevate day-to-day processes. As you start to integrate AI into your manufacturing processes, remember: It doesn’t have to be revolutionary to enhance your current capabilities. There are numerous ways to leverage AI effectively if you have a good grasp of what your organization’s needs are and what your goals are for the future.
Seeing Data as Currency
In a time where AI, electrification, and other progressive frameworks are taking shape to improve workflows and various industries, data is an asset. By soaking up new information that’s added to the system, AI will adjust itself to optimize.
Start by simply collecting any and all information, data, and insights you can – remembering no data is bad data. AI can learn not just from what has gone well, but also from what has gone wrong to help identify and put safeguards on new procedures.
Once you have all your data collected, manage it well: incorporating AI and data management tools into the process to keep your organization up to speed with evolving technology and innovations. Bayes Theorem, named after Thomas Bayes, notes that every piece of knowledge (data) improves the comprehensive understanding of the ground truth – which fully applies to AI, especially when focusing on facts and figures.
Knowledge Transfer + Succession Planning
Armed with the right data, your existing talent pool is proving to be the one-two punch the industry needs, especially when facing increasing labor shortages. With a 28.6% turnover rate, the manufacturing industry is not only losing top talent at an increasing pace but also the knowledge and company-specific expertise that comes along with those individuals. When working with data, numbers, and technological information, this can easily create a gap and suppress innovation and growth. Luckily, AI can be the catalyst for solutions.
By introducing generative AI models to account for data that might be lost through employee turnover, including those retiring from an organization, you can maintain the knowledge gained and enable its transfer to the next expert stepping into the role.
One way to do this is to implement a language model. This model can be trained to absorb a verbal data set from employees and transfer that information into a permanent document to speed up training and onboarding practices. This process empowers and informs new and relatively inexperienced employees to ensure the company’s high standard of quality is maintained.
Beyond turnover and succession planning, this process can take shape between shifts to alleviate manual knowledge transfer. For example, dashboards can inform employees just beginning their shift of what the status is of certain processes and operations – saving time and energy and upping productivity.
Worker Safety
While the importance of knowledge transfer cannot be understated, AI has an equally important role to play in workplace safety. The manufacturing industry relies on strict rules and protocols for keeping team members safe on the job. It is necessary as often those on the manufacturing floor are dealing with powerful and heavy equipment or chemicals that can result in catastrophic circumstances if not managed carefully.
In a world without AI, these safety protocols were the best way to properly manage risk. However, the emergence of AI and the ability to integrate it with robots is proving to be a game-changer. These robots, when programmed with the proper algorithms, can act as a barrier between humans and the machinery needed to bring products to market.
Traditionally, this method was seen as a threat to replace humans and eliminate job opportunities to save costs. However, as the industry becomes more familiar with AI and its use cases, there has been a mind shift in how it can be a benefit. The use of robots is not meant to replace humans. In fact, humans are still needed on the back end to ensure the process runs smoothly logistically —the robots are just an extra precautionary measure to keep teams safe, minimize worker injuries, and decrease production line downtime.
Predictive Maintenance
On a very basic level, AI can ensure your equipment is properly maintained at the right intervals and signal to facilities when an unexpected issue arises in real time with the implementation of sensors and actuators. Without AI, a fault in the production line may go unnoticed for longer periods, impacting business outputs and customer supply chains.
On a broader level, not only is AI helping to improve efficiencies on the line to keep business and customers satisfied, but it is also helping reallocate the time needed by individuals to supervise and potentially troubleshoot solutions to more forward-thinking innovations and other tasks. Gone are the days of immense loads of paperwork and trial-and-error solutions. Today, facilities are more equipped to streamline operations and allow more time and creativity toward the next great invention.
Overall, taking small steps toward AI integration and adoption is the way to go. It is not a tool that should be seen through a vacuum of only being able to help in one area. Leverage it in ways where it will impact everyday practices – taking tasks off human plates so they can focus their creativity and expertise elsewhere.
As companies begin to build out ways humans and AI can work in tandem, keep in mind some of the subtler capabilities will make a world of difference.
Comments (0)
This post does not have any comments. Be the first to leave a comment below.
Featured Product
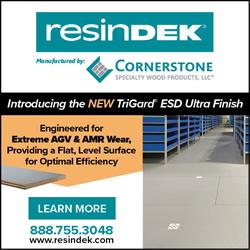